The four largest polyamide oil pans that have gone into production to date are made of Ultramid A3HG7 Q17 (PA 66) from BASF and in what is called off-highway service. Developed and produced in small series by Hummel Formen GmbH in Lenningen, they are used on engines from the 1600 Series manufactured by Tognum subsidiary MTU Friedrichshafen for stationary generators and later on for agricultural and construction machinery.
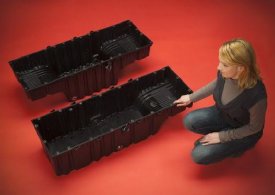
These represent the first time that die-cast or sand cast aluminum oil pans were replaced by polyamide oil pans in such applications . Compared to their metal counterparts, they provide a weight savings of 40 to 50 percent .
To meet the demanding requirements, the resin must not only exhibit good flow properties, but withstand 24,000 hours in a variety of oils at 120°C . Moreover, s ince the engine must sometimes be rested on the oil pan, the material is required to offer sufficient rigidity as well as the ability to absorb impacts and vibrations .
Ultramid oil pans: With simulations and a multi-purpose mold
BASF contributed to successful development with the aid of their ULTRASIM universal simulation tool : In addition to fill, warpage, creep, natural frequency and modal analyses, the experts also investigated directly via computer the static bursting pressure as well as heating of the oil pan under tension . Component testing was conducted at the same time . Load tests performed on the shaker at BASF demonstrated that the resin was able to satisfy the extremely demanding requirements for resistance to aging in oil : One million shocks per direction in space at different acceleration rates while exposed to hot oil did not affect the oil pans and caused no leaks. Depending for which of the three V-engine versions the oil pan is to be manufactured, the flexible multi-purpose mold from Hummel Formen can be quickly converted from the V-8 to the V-10 or the V-12 oil pan by simply exchanging inserts .
The MTU oil pans represent the next major step in the development of plastic oil pans made of Ultramid from BASF . Their predecessors include the first polyamide truck oil pan for the Mercedes Actros BR 500 (2003), the oil pan for the Avalon series of engines from Cummins and the one for the Ford Scorpio in 2009.
Powerful engines for stationary and mobile service
The engines for which the MTU oil pans are intended include the R6, V-8, V-10 and V-12 diesel units with total displacement of 10.5 to 21 liters and an output of 270 to 730 kW . Full-scale production started in autumn of 2009 with the V-12 version as drive for emergency power and constant current generators . In the next step, construction, agricultural and industrial machinery such as combines, cranes and shredders are to be equipped with these engines .