The push for more efficient designs is encountered not only in automaking: manufacturers of furniture, plumbing supplies and electrical devices are increasingly recognizing the benefits of computer simulation when developing new components, especially when it comes to substituting metal. With the aid of CAE (Computer-Aided Engineering), time and money can be saved when designing new plastic parts, as expensive prototypes can frequently be dispensed with. Multiplast in Austria and BASF have exploited this benefit during the development of a plastic valve for a new generation of fire extinguishers.
The main valve body of the new fire extinguishers is molded from the special polyamide grade Ultramid T KR 4355 G10 from BASF and represents the first volume application of this highly glass-reinforced new grade of plastic. This challenging plastic part replaces a brass predecessor in the main valve of the extinguisher. It was developed by Multiplast for the European fire extinguisher market. Tyco Fire Suppression & Building Products, one of the world's largest manufacturers of fire extinguishers, has cooperated with Multiplast in the early development phase. Directly after the beginning of the serial production, Tyco has switched to the new valve for about 90 percent of its product range. Production in Moosbrunn runs already under full capacity utilization.
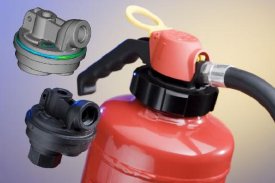
Plastic better than brass
The new valve is in use in the family of cartridge-operated fire extinguishers with a separate pressurized cartridge. The demanding requirements in this type of extinguisher were previously satisfied only by brass valves. The main valve is a multi-function component that integrates the connections for the internal riser pipe, the hose with the spray gun, the trigger mechanism and the handle. To operate reliably, the manufacturer requires that the valve withstand a pressure of 80 bar between minus 30 and 60 degrees Celsius over a service life of 15 to 20 years. Inconsistent quality of the imported metal was one of the major drawbacks of the brass valve for the manufacturer Multiplast.
The common goal was thus to develop a plastic component that could be manufactured efficiently via injection molding, that offered more consistent quality and greater capabilities than the conventional brass component. Such an application requires that the plastic exhibits high heat resistance, high strength and stiffness as well as high dimensional stability. Prior attempts to manufacture the fire extinguisher valve body out of plastic were unsuccessful because of the engineering properties of the materials used. A standard polyamide is unsuitable here. The material must ultimately pass a number of safety tests before it can go into volume use on fire extinguishers. These include investigations of the service life, the burst pressure, the resistance to fire extinguishing agent and the stability after long-term UV-light exposure.
Maximum plastic performance - Not without simulation
To develop the complex component efficiently, fast and reliably, BASF employed its ULTRASIM simulation tool. Classic mold filling simulations are state of the art in the field of CAE today. With ULTRASIM, however, it is also possible to determine the orientation of the fibers as a function of filling pressure and gate location, and then optimize the mechanical performance of the component on the basis of this information. This is no easy task with a glass fiber content of 50 percent and significant anisotropy in the component. Simulation of three load situations was of major importance: the valve's behavior at a gauge pressure of 120 bar, its behavior under a bending load applied by the pressurized cartridge when in horizontal position and the effect of a dynamic load applied by the handle when the fire extinguisher is lifted abruptly.
In case of excessively high pressure, a weak spot had to be designed on the valve that would rupture at a pressure above 105 to 110 bar and in this way prevent uncontrolled bursting of the entire extinguisher. Using ULTRASIM, experts were able to exactly define the function of the intentional rupture location and to fully confirm it experimentally.
When the fire extinguisher is stored in a horizontal position, the fire extinguishing agent - powder or liquid - is in continuous contact with the valve. The Ultramid valve also withstood this load situation in both the simulation and in reality. Finally, the fire extinguisher must not exhibit any failures when lifted abruptly by the handle: a challenge for the lever and for simulation, since strain rate-dependent material properties are involved. Here, too, there was significant agreement between simulation and experiment.
With this knowledge, it was possible to establish the design of the complicated part exactly, with all of its integrated additional functions and without metal inserts, for production in a single injection molding step. Even the four integrated metric threads are plastic, which poses a challenge for both the plastic and the production. The special Ultramid grade used provides such good chemical resistance that the new main valve also received immediate approval for use in maritime environments - a field of application that demands even greater fire extinguisher safety. Furthermore, the final version of the valve, with an operating window of minus 40 to 80 degrees Celsius, achieved a burst pressure increase to 100 bar and resistance to pressure spikes of up to 250 bar, considerably better characteristics than those of the brass part. Resistance to the fire extinguishing agent, environmental factors such as UV radiation and ozone must not be overlooked either. Last, but not least, the carrying characteristics and handle performance of the portable fire extinguisher were distinctly improved.
ULTRASIM - no longer for automotive applications alone
Without a powerful computer tool, this plastic application and replacement of the brass valve would not have been possible. At the same time, working with ULTRASIM at this level requires extensive material data, which must be either available for the particular special resin or established in advance. Both together made it possible for the very extensive methodology and program collection of BASF to pass an extremely crucial test outside the automotive field.
After many successful launches of automotive components in high-load situations such as the first bumper supports, engine mounts and plastic body inserts over the past four years, new opportunities are appearing: the highly accurate predictability offered by the computer simulation, together with the appropriate plastic, eliminates, as in this case, repeated fabrication of prototypes and expensive tests. This allows companies in a variety of sectors to make use of specific materials for efficient and cost-effective production of plastic parts in high-load situations.