Polymer foams are a success story for BASF. This story began in 1952 with the invention of Styropor (EPS: expandable polystyrene). Today, following the successful development of the extruded polystyrene rigid foam panels Styrodur (XPS), the tough-elastic polyolefin range Neopolen, the melamine resin foam Basotect, and the advanced version of EPS for thermal insulation Neopor, BASF has a broad portfolio and unique know-how when it comes to particle and extrusion foams.
Continuous research and the launch of new products on the market open up new applications in a lot of industry sectors: the automotive industry as well as aviation, but also solar technology, construction and of course the packaging industry.
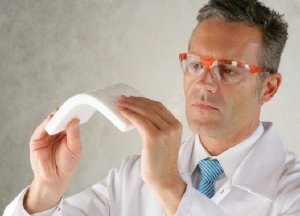
BASF has now succeeded with another innovation: E-por, a material which is based on a new formulation and is manufactured in a new production process. E-por is the first tough-elastic, crack-resistant foam which can be transported, stored, processed and recycled like traditional Styropor. The material is noted for very good fusion of the surface, excellent resistance to solvents, and an appealing look and feel. Because of its high crack-resistance it is multishock-safe and therefore well-suited to being used as transport packaging for high-quality, shock-sensitive electrical and electronic (E/E) products, such as plasma televisions, laptops, refrigerators or washing machines. Thanks to its special property profile, the new BASF granules offer advantages along the entire value chain for transport packaging - from the converter, the appliance manufacturer and the retailer right to the consumer.
Increasing requirements for the packaging of sensitive E/E goods
When it comes to the safe transportation of electrical and electronic devices, the weight and sensitivity to shock of the product are crucial. A protective cardboard packaging is usually adequate for transporting robust and lightweight goods. However, cardboard only absorbs a small amount of energy, so its cushioning effect is limited. This is why cardboard is generally combined with Styropor. Styropor is light and has an excellent cushioning effect. But Styropor is a rigid foam and can break if the packaging is dropped, for example when unloading a truck. Once Styropor has been broken or torn, the cushioning effect diminishes significantly.
As electronic products are becoming lighter and lighter, but electronically more elaborate and thus more sensitive to multiple shocks, the requirements for the packaging are becoming more stringent. This is the reason why valuable and sensitive products are packed in multi-shock safe polyolefin and interpolymer foams. Compared with the standard packaging material Styropor, these foams have a number of disadvantages in processing and are not as easy to recycle as Styropor.
E-por combines the shock resistance and aesthetic appeal of interpolymers with the cost-effective recycling and ease of processing of the standard material Styropor. E-por has a very low blowing agent content of less than 6 percent. Rival products based on interpolymers require a blowing agent content of more than 10 percent. This large amount of blowing agent has to be frozen in the raw material, which means that interpolymers have to be transported and stored in a cold chain. Rival products based on polyolefins have not been capable of containing a blowing agent so far. They are pre-foamed during the production process, which means that it is mainly air that is transported from the raw material producer to the packaging manufacturer. This increases the transport costs considerably.
E-por thus saves transport, storage, and energy costs. It can be transported and stored at room temperature. It is foamed by the packaging manufacturer with a small amount of steam. The material can also be processed on conventional Styropor machines, which is more energy-efficient than processing polyolefins. Ultimately, E-por is the only foam resistant to multiple shocks which can be degased and recycled using Styropor technology: This means that converters do not have to change their machines.
Advantages along the entire value chain
Beyond the converter, E-por offers advantages for the entire value chain right through to the consumer: Appliance manufacturers are provided with a dust-free, flexible packaging material with an appealing look and feel which allows compact packaging with reduced damage and returns, and lower disposal costs. Retailers and consumers can dispose of the reliable transport packaging by the Styropor way, that is cost-efficiently and without additional efforts.
The development of E-por became possible thanks to a new research approach: BASF's researchers no longer regarded foams as a static blend of a polymer and a blowing agent, as is the case with interpolymers, for example. Instead, they developed E-por as a complex formulation of different ingredients which interact both with one another and with the blowing agent pentane. The researchers managed to transfer the concept of the impact-strength modification of polymeric materials to particle foams. This formulation is produced in a new type of BASF process. BASF's direct customer, the converter, is then able to process the granules using conventional Styropor technology. And this produces a foam with a new foam architecture. BASF has been present in the market for almost a year with pilot quantities of E-por. Several customer projects in all regions are running successfully.