With any thermoplastic resin, improved flow characteristics always represent a benefit for processing that offers time and cost as well as energy savings. Without having to mention it explicitly every time, an easier-flowing material during the injection molding process contributes more to sustainability than its harder-flowing counterpart - as long as other properties remain similar.
After having greatly improved the flow characteristics first of PBT (polybutylene terephthalate) - Ultradur High Speed - and then of various polyamide 66 grades - Ultramid A High Speed - BASF has now completed the family: The new High Speed products are polyamide 6 compounds; the first grade will be Ultramid B3WG6 High Speed.
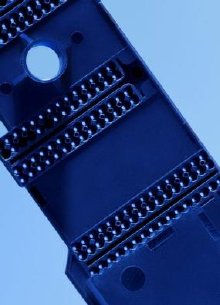
A new member of the family: Ultramid B High Speed
The primary characteristic of this new grade is its flowability. In spiral flow tests, the new Ultramid B High Speed flows at least 50 percent farther than its conventional predecessor: with a spiral flow thickness of 2.5 millimeters, flow path lengths of up to one meter are possible.
The benefits associated with good flowability can basically be exploited in two different situations. Sophisticated structures and thin walls - often encountered in electronic components because of increasing miniaturization - can be filled more easily and reliably; the reject rate drops, especially in the case of complex geometries. The considerably reduced injection pressure means that molds are subject to less wear. This translates into increased uptime and reduced maintenance costs. On the other hand, wall thicknesses can be reduced, which means lower component weight.
In the case of a better-flowing polyamide 6 resin, however, other possibilities open up. Since large under-the-hood parts such as engine covers and intake manifolds but also pedals represent the most important fields of application for polyamide 6, a flow-optimized PA 6 will first demonstrate its cost benefits in these applications. As the result of easier material flow, the injection and filling pressure needed for large parts drops. This, in turn, lowers the clamping force requirement, and the processor can produce parts on smaller machines. This also represents a significant added value, since it is well known that the operating costs of an injection molding machine increase disproportionately with size.
Since, for instance, many intake manifolds are assembled by means of vibration welding, it is important to know that the new Ultramid B High Speed achieves weld joint strengths comparable to those of its classic predecessor. Other mechanical properties of the new material, such as stiffness and strength, also have values similar to those of the standard material. The very good surface of components produced from Ultramid B3WG6 High Speed can also be counted as one of the special characteristics.
Fast and defect-free production:
Greater energy efficiency during injection molding
A great deal of experience regarding the potential energy savings when processing flow-optimized grades has been obtained for Ultradur High Speed, since the easy-flowing PBT from BASF has now been on the market for six years. For this reason, more extensive investigations of the energy efficiency during injection molding have been conducted with this material. A detailed analysis of the injection molding parameters makes it possible to determine exactly the benefits that improved flowability offers the plastics processor.
One of the primary benefits is that better flowability allows the temperature during injection molding to be lowered: the PBT grade Ultradur B4300 G6 High Speed can be processed at a 30 degrees Celsius lower temperature than the corresponding standard material with no other changes in the process or molded part quality. What is important for the plastics processor are the exact energy-savings that result.
On an electric injection molding machine, the heating energy is reduced first, which represents about 80 percent of the overall energy consumption. This translates into a 10 percent reduction of the power consumed by the machine. The lower processing temperature also reduces the cycle time by 20 percent, which means an additional energy savings of 20 percent as well. Thus, in the case investigated here, which is representative of typical injection molding machines, a total energy saving of 30 percent is achieved.
Cycle time reduction:
Why you should not compare apples and oranges
The reduction in cycle time resulting from lowering the processing temperature - at the same injection pressure - is the primary interest when assessing the energy-saving potential of easy-flowing materials. It is essential that the ejection temperature (of the molded part) be the same when comparing cycle times, since only then does the effect associated just with the lower melt viscosity of the new material become apparent. Using a ribbed component as an example, a cycle time reduction of up to 25 percent was measured for Ultramid B3WG6 High Speed.
High-Speed polyamide in automotive electronics
A related grade of the new high-speed polyamide, Ultramid A3WG10 High Speed (PA 66 with 50 percent glass fibers), that has been on the market since 2008 has recently gone into use for volume production at Tyco Electronics, one of the world's leading manufacturers of electronic components. A product called a center plate is used to manufacture electronic circuits for automobiles and is being molded from this easy-flowing material.
The center plate has over 200 openings with a diameter of only 0.5 millimeters and a wall thickness of only 0.2 millimeters. Such a complex, thin-walled design in such a comparatively large part requires a material that flows easily through the narrow separations and fills them reliably. In addition to its flow properties, the benefits of the resin in this demanding part include its high dimensional stability, which ensures that the tiny openings are positioned exactly where they belong, since this plate serves to position many metal contacts perfectly. In addition, this easy-flowing product allows the injection pressure to be reduced by one-half, protecting the mold and reducing the wear on the mold with its many delicate cores while lowering the reject rate at the same time.
Moreover, the High Speed grades in the Ultramid A product line are characterized by very good surface quality, which is a benefit for visible parts in the engine compartment. Ultramid A3WG7 High Speed, for instance, is being used for a cylinder head cover that has been molded in commercial volumes in China since 2009.
Flow-optimized and available in light colors
Flow-optimized PA 66 grades with only minimal inherent color that can be tinted in light shades - possibly even directly by the processor - represent an additional benefit for the electrical and electronics industry. Ultramid A3EG7 and Ultramid A3EG10 High Speed are two examples. These products are useful especially in the automotive electronics industry: it works with a variety of colors and color codes that ensure fast and reliable assembly and assignment of different connectors and sockets.
With Ultramid B High Speed, BASF is now expanding the already existing PA and PBT product lines of easy-flowing materials. The first representative of this group is Ultramid B3WG6 High Speed, a 30 percent glass-reinforced grade. By the K show 2010, it will be available in sample quantities. Additional fiber contents, highly filled special products and impact-modified grades will follow shortly.