With its new Ultrason E Dimension, BASF has succeeded in combining high dimensional stability and ease of processing where previously this was not possible: in the market for high-temperature resistant thermoplastics. The new member of the polyethersulfone (PESU) family exhibits not only very high stiffness at temperatures between 120 and 220 °C, but also exceptional dimensional stability.
Nevertheless, its viscosity is still so low at processing temperatures that it can fill complex injection molds reliably. Thanks to the good flow characteristics, it has also been possible to increase the glass fiber content beyond that achievable with conventional PESU grades. This makes the new material a strong - and economical - alternative to polyetheretherketone (PEEK), for instance.
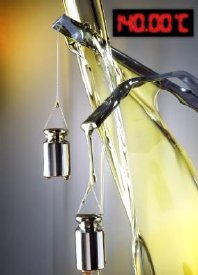
New formulation resolves contradiction: stiff, well-flowing and dimensionally stable
While stiff, semi-crystalline high-temperature polymers such as PEEK or PPS (polyphenylene sulfide) often warp during injection molding, the dimensionally stable amorphous thermoplastics such as PESU are usually more difficult to process. In both product groups, the challenges become more pronounced when glass fibers are incorporated. Whoever tried to increase the stiffness of high-temperature plastics quickly found that there were limits.
A new component in a classic Ultrason E formulation now contributes to increased stiffness at elevated temperatures while simultaneously improving the flow characteristics of the PESU melt significantly without noticeably compromising the dimensional stability of the material: The elastic modulus of Ultrason E Dimension still achieves values of over 10,000 MPa even at 120 °C, making it comparable to PEEK or PPS compounds. The new Ultrason's coefficient of thermal expansion is about as high as that of aluminum, which is an enormous achievement for a plastic. Furthermore, in contrast to semi-crystalline polymers, the new material exhibits almost linear and isotropic thermal expansion between 25 and 200 °C. At similar performance, the new Ultrason also frequently represents a considerably more economical alternative to other high-performance polymers.
Head-to-head with aluminum
Compared to aluminum, the new plastic can exploit its greater ease of processing, since the plastic part does not require subsequent finishing with a drill or milling tool. This translates into economic advantages over a metal counterpart. The material offers potential, e.g., for use in the form of pistons, switches and gears that come into contact with hot oil and must still function reliably above 140°C. The field of application is in no way limited to the automotive sector: Ultrason E Dimension is also suitable for food contact.