On Stand F2, Kistler Instruments will be showing new additions to its extensive range of sensors and systems for automotive development and production.
In particular, new developments of its NC electro-mechanical press system which is widely used in the automotive and supply industry in a wide range of manufacturing and assembly processes, such as gearbox, engine, chassis and pump installation will be shown in the UK for the first time.
Kistler maXYmos® 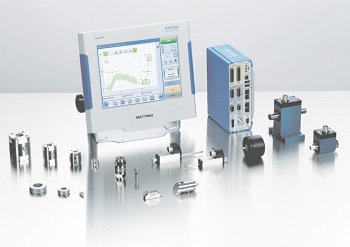
The maXYmos XY monitors make it possible to check and evaluate the quality of all manufactured products on the basis of a force-displacement curve. The user can apply evaluation objects in order to adapt the curve evaluation to the individual monitoring task. Based on this specification, the maXYmos can check each workpiece and decide whether the part is good or bad.
The new maXYmos NC (Numeric Control) replaces the widely used Kistler DMF-P force/displacement monitoring device and is a development of the well proven Kistler maXYmos technology designed specifically for use with the Kistler NCF servo actuators. The new large colour touchscreen used in conjunction with the user friendly menu structure, PLC communications and improved data export facility.
The Kistler NCF electro-mechanical actuators, a cost effective alternative to mechanical and hydraulic systems for press fit production operations, are now available with the Kistler maXYmos to provide real-time monitoring and control of the joining process. Integrated sensor technology and powerful force-displacement evaluation allow complete process monitoring and documentation of all measurement results. Low cost of ownership combined with ease of installation and operational flexibility make the NCF range ideal for a wide range of industrial applications.
Kistler KiBox® To Go
The Kistler KiBox To-Go provides a complete combustion analysis system for mobile and test bed applications.
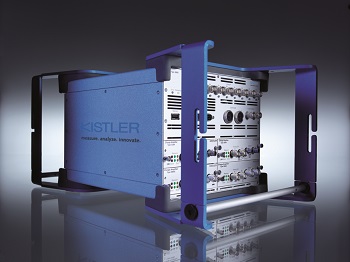
Building on its extensive engine testing and analysis experience, Kistler Instruments developed the KiBox mobile engine combustion analysis system, which integrates with other mobile systems for ECU development and diagnostics.
The KiBox system is compatible with PiezoSmart and TEDS (Transducer Electronic Data Sheet) sensor identification to simplify set-up and operation.
Automatic plausibility checks guarantee prompt measurement availability and high-quality data. Using the signals from the vehicle's sensor, CrankSmart technology provides TDC (top dead centre) crank position to an accuracy of better than 0.1 degree with automatic error indication for both diesel and petrol engines. This simplifies installation and maintenance by eliminating the need for a separate optical crank angle encoder.
KiTorq® for test stand applications
With three new measuring ranges, the Kistler KiTorq measuring flanges now cover 100Nm to 5,000Nm with seven flanges.
The Kistler KiTorq torque sensor system is now available with Profibus, Profinet CANopen, Ethercat and EthernetIP interfaces in addition to the voltage, frequency, USB and RS-232 interfaces. The new stator is fully compatible with all KiTorq type 4550A rotors.
The new communication options allow the KiTorq system to be integrated directly into the user’s test environment through the Fieldbus interfaces. This saves time during installation and eliminates the cost of additional equipment to convert measured data making the new KiTorq stator exceptionally cost effective for test stand design, installation and operation in applications for electric motor, internal combustion engine, transmissions, pump and compressor testing.
The new smart stator can be used with any KiTorq rotor of the same speed rating and will automatically recognise the rotor measuring range. With rotors available with seven measuring ranges from 100 to 5,000 Nm, hardware investment is minimised as one stator may be used with rotors of differing ranges for different applications. Installation is simplified by the contactless, digital telemetry that eliminates the need for an antenna ring whilst maintaining the excellent signal bandwidth of 10 kHz and accuracy of better than 0.05% of range.
A speed measurement of 60 pulses per revolution is integrated in the standard system.
Vehicle dynamics testing systems
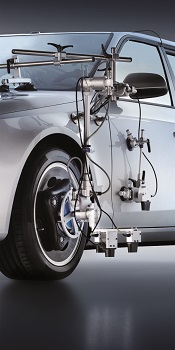
The Kistler RoaDyn® measuring wheel system will be featured in an on-stand video showing the system in use.
RoaDyn® wheel force sensors are now used by most manufacturers of road and track vehicles to predict the durability performance of vehicle chassis and body.
By providing data for CAE tools, realistic service load data can be applied to single suspension components and complete subassemblies during laboratory tests.
Kistler also manufacture a wide range of non-contact optical sensors, GPS, microwave sensors, mechanical sensors, fuel flow meters, data acquisition and evaluation systems and software.
This unique combination of application expertise and specialised equipment provide complete solutions for virtually all vehicle dynamics testing applications.
About Kistler Instruments
The Swiss-based Kistler Group is a leading global supplier of dynamic measurement technology for pressure, force, torque and acceleration. Kistler’s technology is used to analyze physical processes, control industrial processes and optimize product quality.
Kistler has a full range of sensors, electronics and systems for engine development, vehicle technology, assembly technology, plastic and metal processing as well as for biomechanics.
The Group maintains its global presence through 28 sales and manufacturing companies, with tech centers on all continents and more than 30 agencies, enabling the Group to maintain local contact with customers and offer individualized application support.
The Kistler Group employs 1,200 people and generated revenues of CHF 279 million (GBP 193M) in 2012.