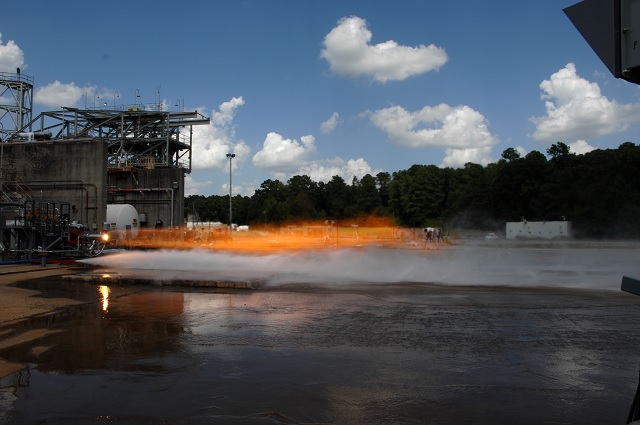
Image Credit: NASA photo / David Olive
Complex 3D-printed rocket engine components have been successfully tested by NASA at its Marshall Space Flight Center located in Huntsville, Alabama.
Using 3D printing, an additive manufacturing technique, NASA engineers have designed highly intricate and complex rocket engine injector components. NASA engineers designed each component and fed the resulting data into the 3D printer’s computer. The printer then created each part by building the design up with layers of metal powder, before fusing them together using a laser in a process known as selective laser melting.
The rocket engine injector was printed with 40 individual spray elements manufactured as a single component. The injector was similar in its design to the injectors used in large engines such as the RS-25 engine, which will be used in the Space Launch System (NASA's heavy-lift, exploration class rocket which is being developed for future manned explorations of Mars).
Using conventional manufacturing techniques, 163 individual components would have to be produced and assembled, compared to the use of 3D printing technology which only requires two parts to be built. This enabled the engineers to rapidly and economically construct highly reliable components which improve the performance of the rocket engine.
3-D Printed Rocket Injector Roars to Life
NASA tested two rocket injectors for five seconds each, generating a thrust of 20,000 pounds. Intricate geometric flow patterns were created to allow hydrogen and oxygen to combine prior to combustion at a pressure of 1400psi and a temperature of 6000˚F.
Increasingly complex rocket engine components such as nozzles and injectors have been tested by NASA engineers at the Marshall Space Flight Center, who are aiming to minimise the complexity involved in production of engine parts, as well as the time and cost of fabricating and assembling future engines.
This News Feature Around the Web