The stationary, multicomponent dynamometer from Kistler Instruments has been designed specifically for measuring forces and moments in all three axes produced during high performance cutting processes with high accuracy and signal quality for the precise analysis of drilling, cutting and grinding at high removal rates.
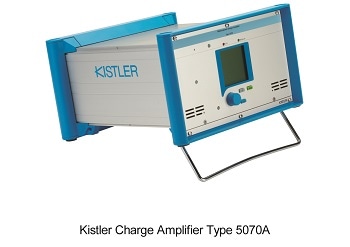
The compact piezoelectric dynamometer has an extremely robust structural design combined with a wide measuring range from a few Newtons to 30kN in all three directions making the Type 9139AA suitable for demanding applications where both low and high cutting forces are developed.
The patented design has integrated temperature compensation which eliminates the effect of heat generated during the cutting process to minimise signal drift. This ensures that forces generated by processes that create large amounts of heat may be measured with great accuracy. A high natural frequency was a key issue in Kistler's development work and extensive FEM analyses were carried out to optimize the design and structure so that natural frequencies of about 3 kHz are achieved despite the dynamometer's size. This ensures that the measurement signals generated by the cutting processes are captured accurately, even at high tooth passing frequencies.
The large number of threaded holes simplify mounting workpieces on the dynamometer whilst the widely used Fischer flange connector concept with the same pin configuration as other Kistler stationary dynamometers make it simple to change the measuring platform using the existing cables and charge amplifiers. The dynamometer is corrosion-resistant and protected against penetration by splashing water or cutting fluid to IP67 when used with the appropriate connecting cable. The Type 5070A multi-channel charge amplifier is especially suited to interface with the dynamometer, although other charge amplifiers with suitable operating parameters may also be used.