Morgan Advanced Materials, a global leader in specially engineered materials, has quadrupled its capacity for the production of co-fired multilayer piezoelectric components (PCMAs) as it prepares to take advantage of attractive projected market growth.
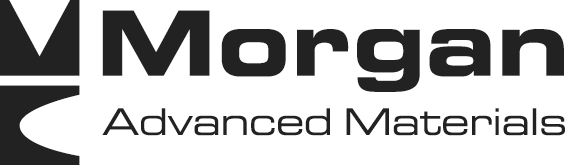
Morgan has upgraded its existing facilities allowing it to produce tens of thousands more PCMA components every month. In addition to enabling the business to achieve a higher output, the upgrade has also enabled Morgan to improve its accuracy of electrode registration to produce a higher quality of multi-layer application. This adds to Morgan’s existing capacity for precision dicing, sputtering, and automated optical inspection, all performed in a cleanroom environment.
The move means Morgan is well poised to take advantage of a piezoelectric industry set for growth between now and 2022, with significant demand for piezoelectric components stemming from industries including industrial control, communication, optics, and micro/nano processing. PCMAs are fast gaining traction in these sectors because their inherently capacitive nature means that they do not require any magnetic coils, therefore providing simple, compact solutions to actuation needs. They are also free of electromagnetic interference, while offering high energy efficiency, allowing Morgan’s engineers to offer customers an extended battery life for their products.
Morgan’s proprietary composition has already demonstrated the capability to produce ultra-thin PCMAs, producing components as thin as 100 microns with aspect ratios as high as 1/100. These components open up the design space for portable device designers to deploy low voltage piezoelectric actuation for ultrasonic motors, and haptic feedback solutions. Morgan’s PCMAs also offer large displacements of the unibody piezoceramic component with low voltages, allowing customers to drive their actuation directly from batteries, without the need for boost circuits. This is particularly significant for in-field service deployment applications, where the application requires a portable or onsite solution.
The increasing use of robotics being deployed in harsh environments is also presenting opportunities for Morgan, as thermal stability begins to present a challenge for industrial control devices. Often, service temperatures can drive limitations in externally amplified benders, such as unimorphs and bimorphs, which lose stamina with increased temperatures, limiting the control assembly’s rating for use. To combat this, Morgan is producing co-fired variants, deployable to 200°C (392°F), reducing the effect of higher temperatures and much of the degradation that is typically associated with standard unimorphs and bimorphs.
Al Metcalfe, General Manager for Technical Ceramics at Morgan Advanced Materials commented: “Our improved PCMA line, which is housed in a class 10,000 cleanroom in our Bedford, OH facility, gives us the capability we need to take advantage of the fast growing PCMA market. We have ensured that our PCMA line is capable of accommodating rapid tool changes, so we can make light work of complex designs and enable faster commercial penetration for our customers, across a wide range of sectors.”
For more information on Morgan’s range of piezoelectric components please visit: www.morgantechnicalceramics.com/cofired-actuator