At Composites Europe in Dusseldorf, Germany (November 29 – December 1) Hexcel will be promoting composite materials for Automotive, Wind Energy and Recreation markets and launching new products and technologies to support customers in their quest for better performance and faster processing.
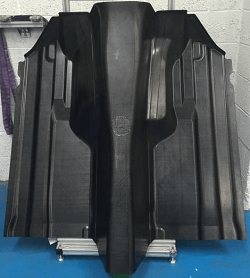
Hexcel’s range of composite materials for the automotive industry now includes the HiMax™ range of multiaxial fabrics manufactured in Leicester, UK.
Hexcel will display a composite floor demonstrator manufactured for Jaguar Land Rover using Hexcel's HiMax™ carbon fiber multiaxial fabrics specifically optimized for high-volume composites manufacturing processes.
For this part Hexcel created a non-crimp fabric with the optimum balance between drape, stability and permeability, using an automotive-grade standard modulus, high tow count carbon fiber. The high drape HiMax™ reinforcement conforms to the complex mold geometry of the part, minimizing the defects typically seen with standard materials, whilst its permeability is optimized to enable fast resin injection and cure times required for high volume manufacturing.
Hexcel will also promote its range of prepregs for automotive structures including HexPly® M77 prepreg stacks that are used in the BMW 7 Series to save weight and reinforce the metal shell
of the B-pillar. HexPly® M77 prepreg cures in just 1.5 minutes at 160°C, meeting volume production requirements.
Hexcel supplies BMW with preform stacks made of unidirectional carbon prepreg plies combined with adhesive.
Also on the automotive theme Hexcel will display a suspension knuckle made by St Jean Industries in which the aluminum structure is stiffened with HexPly® M77 prepreg stacks. This results in a 26% increase in stiffness compared to the aluminum-only knuckle and the greater stiffness is achieved without any increase in part volume. The aluminum/CFRP hybrid version can therefore be incorporated in the current space restrictions, allowing just one part design to be used across all models in the range, for rationalization and cost-saving. The CFRP increases the maximum strength before failure of the part, with optimum load distribution determined by Hexcel’s FEM calculations. Hexcel produces the net shape 2D preform in less than 1min.
The knuckle’s prepreg stacks are bonded to the aluminum with Redux® 677, Hexcel’s new fast curing film adhesive for the high volume processing of metal/CFRP hybrid structures. Redux® 677 is designed for automated compression molding and is ideal for bonding metals, thermosets and thermoplastics with HexPly® M77, having a compatible cure cycle of 2 minutes at 150°C for green strength and 4 minutes at 150°C for full cure (at 3.5 bar).
Redux® 677 provides high temperature resistance and excellent lap shear performance when bonding oily steel (3g/m2) or aluminum to CFRP. The adhesive is resistant to the e-coating process, climate variations and salt spray testing. It is user friendly with a 4 week out life at room temperature and has low tack for ease of handling and positioning. Customers have confirmed that Redux® 677 provides high bonding performance, exceeding automotive standards, and is designed for high volume production.
Hexcel’s HexPly® M77 epoxy resin is also available in the form of HexMC®-i M77, a high performance long fiber carbon/epoxy molding concept developed for compression molding in which the high fiber volume content assures excellent mechanical performance. At Composites Europe Hexcel will display a structural part combining HexMC®-i material co-molded in a one-step process with HexPly® unidirectional carbon prepreg.
The combination of HexMC®-i with UD prepreg produces complex 3D shapes with significantly enhanced mechanical performance that can be optimized by the number of layers of UD prepreg in the construction, with the flexibility to place them on one side only or to lay them either side of the HexMC®-i in a sandwich construction. Tests have proven the increase in flexural modulus that is achieved with this hybrid construction, without increasing the weight of the part.
Polyspeed® Pultruded Carbon Profiles are new technology from Hexcel for pre-cured, thick-ply carbon fiber elements. Pultruded profiles offer an economical way of structurally reinforcing wind turbine blades, and any other industrial application requiring load-carrying performance. Carbon fiber tows are impregnated with a thermoset resin and shaped and cured in a continuous pultrusion process, resulting in perfect fiber alignment and a smooth surface.
The controlled resin and fiber content result in consistent quality, weight and mechanical properties. This technology enables very large parts to be made, with no restrictions on the part length, other than their transportability.
Pultrusion is a cost-effective solution for achieving standardized geometries in high volume production. The production-ready components can be made in a wide range of shapes including L-shaped and rectangular. They are compatible with Hexcel’s epoxy prepregs including HexPly® M79 and HexPly® M77 as well as many commercial thermoset infusion resins.
Key benefits of Polyspeed® Pultruded Carbon Profiles are the consistently high structural properties including impact performance, fracture toughness and shear strength. The low shrinkage behavior ensures excellent surface quality and the pultruded profiles are corrosion and abrasion resistant. High levels of dimensional accuracy are assured.
At Composites Europe Hexcel will display a 2 meter diameter carbon laminate coil made from Polyspeed® carbon fiber pultrusion for the structural reinforcement of a wind turbine blade.