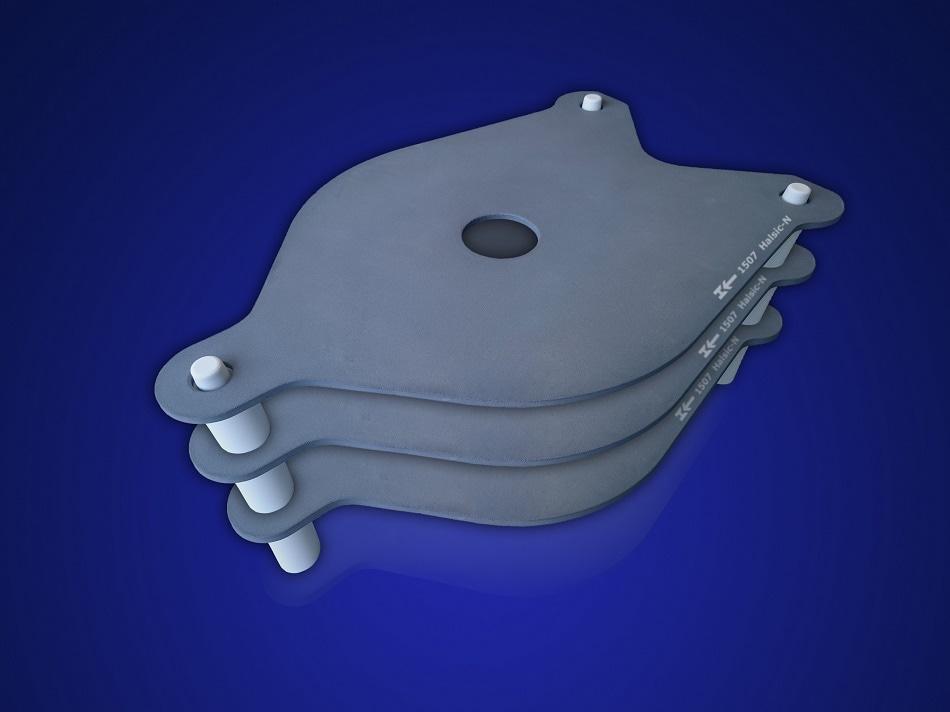
This year’s Ceramics Expo has been chosen for the launch of a brand new range of kiln furniture from Morgan Advanced Materials, suited to the production of catalytic converters and diesel particulate filters (DPFs).
The material, known as Halsic-N, is a nitride-bonded silicon carbide, with a microstructure which offers increased mechanical strength and greater durability than the typical materials used for firing honeycomb structures. It is an advancement of Morgan’s popular Halsic-R range, designed to have an increased lifespan, with enhanced refractory properties including resistance to oxidation, and thermal shock.
The material is already being widely used for the firing of ceramic porcelain throughout Europe, but Ceramics Expo will mark the first time Morgan has made Halsic-N available to the US market, where the production of catalytic converters and DPFs is accelerating.
US legislation concerning vehicle emissions is increasingly making the role of catalytic converters and DPFs more important for diesel vehicles, where the nation is working with the rest of the world to reduce the release of harmful gases in the form of vehicle emissions. Key to the success of these is the dense honeycomb structure, manufactured by firing ceramic material.
This unique structure provides the maximum surface area on which chemical reactions take place, using the least amount of catalyst. This facilitates the conversion of carbon monoxide and hydrocarbons to carbon dioxide, and nitrogen oxide to nitrogen gas. In order to create the honeycomb ceramic structure, the material must be fired in high temperatures of up to 2,732°F (1,500°C), requiring hard wearing, durable refractory materials.
Throughout the US we are seeing an increase in the production of DPFs and catalytic converters, and the design of such components is becoming more sophisticated all the time. These components used to consist of only one filter per catalytic converter, however today’s models have two or three separate discrete filters, prompting demand for the firing process. Halsic-N is our response to this demand. A material with a flexural strength of 160MPa, improved oxidation-resistance and resistance to creep deformation, it delivers all of the key performance attributes demanded by kiln users. Morgan also has the capability to form shapes to the exact dimensions required by customers, delivering a material that can be relied upon for repeated use during rapid heating and cooling.
Dr. Michael Rozumek, R&D Director at Morgan Advanced Materials
Morgan Advanced Materials will be officially launching its Halsic-N material to the US market from booth 325, at Ceramics Expo, which is held at Cleveland, Ohio, from April 25-27 2017.
For more information on Morgan’s range of Halsic materials, please visit: http://www.morgantechnicalceramics.com/halsicN-expo