Deben, a leading provider of in-situ testing stages together with innovative accessories and components for electron microscopy, reports on how the Center for Research in Metallurgy (CRMGroup) in Belgium is using a three point bending stage in their development program to produce new steel and coated steel products for the automotive and other industrial uses.
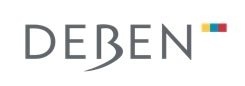
CRMGroup has facilities in Liège and Gent in Belgium where R&D and technology solutions are offered to industrial partners working with metallic materials. The group has skilled and experienced research teams with unparalleled testing facilities covering the whole manufacture chain of metals, from raw materials to advanced steel applications, ranging in size from laboratory scale to pilot and even semi-industrial production lines.
Dr Xavier Vanden Eynde works at CRMGroup in Liège. Part of Xavier’s main goals is to improve the analytic and imaging capabilities for the support for the development of new processes, steel grades or coated products for a wide range of applications such as automotive and appliance industry. The understanding of the local mechanical behaviour during bending is an important issue to evaluate the flexibility of coating and metal bare substrate.
Deben has been chosen by CRMGroup through a competitive tender and the equipment has been financially granted by the 2007-2013 FEDER programs from the EU (funding in the framework of “CLEARZINC/CLEARZINC SEM-FEG” project). CRM want to acknowledge the Walloon Region and the European Fund for Regional Development for this support.
CRMGroup in conjunction with Deben have developed a new micro-machine to investigate this bending behaviour of metal sheet. The set-up of this device is similar to a 3-point bending test but, in this case, the punch or anvil is fixed and the die moves. Using such a tool configuration, it is possible to keep the surface of the sample at the same position during the bending process and then to characterise the evolution in real time of the bend with either an optical microscope or a scanning electron microscope (SEM).
This stage is a prototype. It will be an important tool to understand the flexibility of a large variety of flat products.
In one measurement we can have complete and continuous information about the flexibility. For example, this new microstage offers a high angle for bending and then, we have been able to investigate the origin of crack initiation and propagation.
Dr. Xavier Vanden Eynde - CRMGroup
The work is at an early stage but has shown great promise. Samples investigated to date include the SEM study of changes to a steel surface as a function of bending radius. This is also referred to as the T-bend value as a function of the die position. In the images below, a sample is shown without deformation and after bending caused by the die pushing up.
At each bending radius, the surface on the top of the bend is recorded and from image analysis, the number of cracks and the crack area are determined manually or through an image analysis algorithm. From this work, it is concluded that the characterisation of the bending properties of metal sheet in a one-step experiment, it is possible to determine the number of cracks and their dimension during bending.
The visualisation of crack initiation and propagation will be useful for the next developments of coatings or coating strategies as well as to understand in-depth crack sensitivity and coating flexibility.
This Microtest three point bending stage designed to meet the experimental needs of CRMGroup is an excellent example of the commitment of Deben to provide one-off solutions for their users. For more details of how Deben may help customers to develop a special configuration or to obtain full details of the Deben applications and product portfolio, please visit www.deben.co.uk.