Deben, a leading provider of in-situ testing stages together with innovative accessories and components for microscopy, reports on Stellenbosch University’s research into the production and mechanical properties of microlattice structures.
Stellenbosch University have used both laser-based powder bed fusion (LPBF) and in situ microCT systems to study Ti6A14V microlattice structures. Funded by the South African Collaborative Program in Additive Manufacturing (CPAM), their work focused on the production and mechanical properties of the microlattice structures. They also looked at the in situ deformation of these structures, obtaining in situ microCT images during compression testing. As a result they gained new information regarding both the mechanical properties and manufacturability of such thin-strut lattices.
Professor Du Plessis provides insight into the study: “In this work the ability of the CT500 to precisely control the compression applied to the samples allowed in-situ images of a micro-lattice structure produced by laser powder bed fusion. At the scale of these lattices with struts around 0.1-0.3 mm thick, the production quality of the struts is highly important and is expected to affect the mechanical properties. In this case, it was shown that despite the thin struts with rough surfaces, the deformation under compression occurs as expected for this design and follows the same rules as thicker-strut lattices of the same design. The elastic modulus values obtained in this way will also be useful for future research as this scale of lattice in Ti6Al4V is particularly suitable for medical implants.”
Fig. 1 shows the design of the microlattices.
(a)Diamond type design - single unit
(b)CAD designs of the four lattices
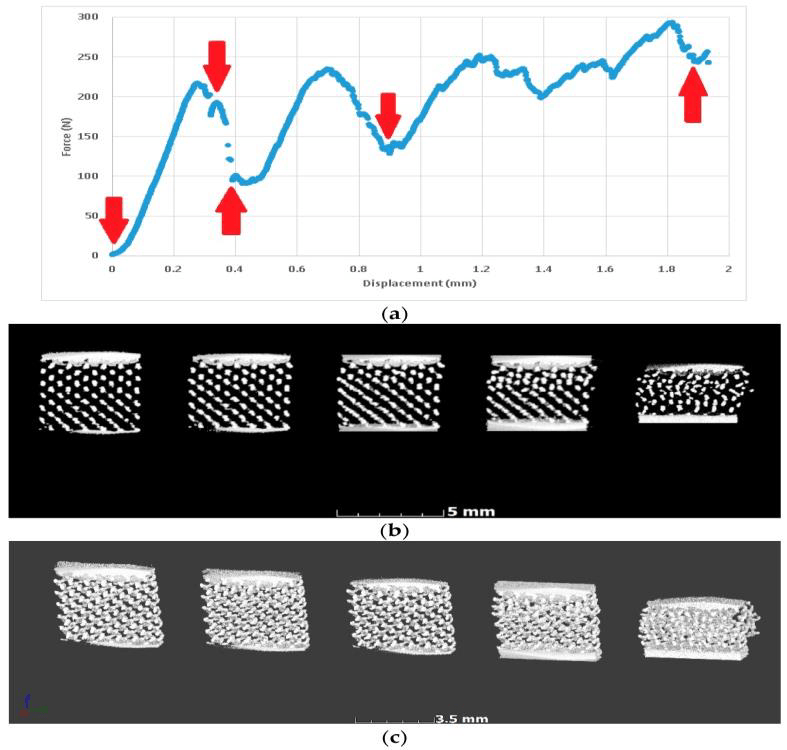
Fig. 2 Images of lattice during deformation
(a)Red arrows showing steps for microCT scans (force-displacement)
(b)Slice images showing collapse (microCT scans)
(c)Corresponding 3-D microCT images
Professor Du Plessis continues: "I am so excited that the CT500 allowed us to image such intricate details of the produced structures under load. 3D printed metal lattice structures such as these have so many exciting applications and this work allows us to better understand their properties and design lattices that can be used in real world applications with confidence in their failure modes, mechanical properties and reliability in general"
The results obtained show that the density of the microlattice played a large part in determining its mechanical properties as expected. This discovery aids the process of making confident predictions in future regarding the mechanical properties of microlattice structures – which have many interesting applications, one of which is in medical implants (e.g. bone replacement). The in situ microCT images are the first of their kind, showing the deformation and yielding behaviour of a full microlattice structure and demonstrated that under compression the largest deformations occur at the strut junctions for this design. For more information please see [1] or visit Professor Du Plessis’ research page: http://blogs.sun.ac.za/duplessis.
References:
https://www.ncbi.nlm.nih.gov/pubmed/30205590
[1] A. Du Plessis, D.-P. Kouprianoff, I. Yadroitsava, I. Yadroitsev, A. Du Plessis, D.-P. Kouprianoff, I. Yadroitsava, I. Yadroitsev, Mechanical Properties and In Situ Deformation Imaging of Microlattices Manufactured by Laser Based Powder Bed Fusion, Mater. 2018, Vol. 11, Page 1663. 11 (2018) 1663. doi:10.3390/MA11091663.