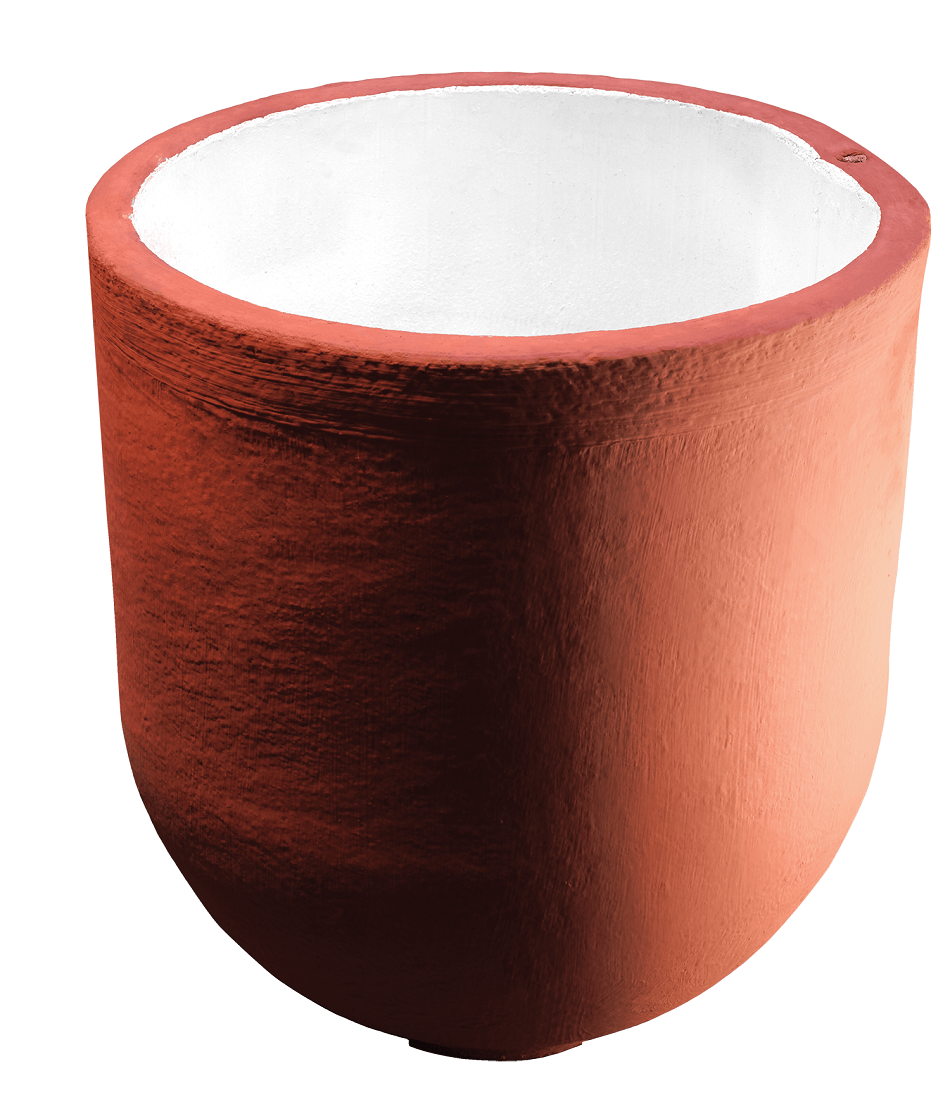
As aluminum becomes the material of choice for automotive manufacturing, a global leader in advanced material development and application is helping aluminum casters to improve quality of output and reduce rejections by avoiding metal contamination in the melting and holding process.
Morgan Advanced Materials is highlighting the consequences of aluminum contamination, as it continues to make strides in the development of two specialist coatings, designed to act as a diffusion barrier during the melting process. Although aluminum is often alloyed with other metals and elements to give the exact mechanical and chemical properties for each application, contamination and impurities caused by chemical reactions with crucibles can affect the overall microstructure of the material post melting.
The presence of impurities and inter-metallic compounds in aluminum melting can reduce the overall ductility of aluminum materials, as well as causing dislocation. The quality of castings is often significantly affected by metal impurities, causing an increase in rejection rates. As the automotive industry continues to favour aluminium where reduced weight is significant for emission control, it is important to ensure that as pure a material as possible is created. The industry is becoming highly competitive with cost pressures mounting every day. This means factors such as higher casting quality, reductions in rejections, and improved crucible life are making a big difference to cost competitiveness.
Mirco Pavoni, Global Technology Director, Molten Metal Systems at Morgan Advanced Materials
Morgan’s answer to this is its PRO and STAR coatings, which have proven particularly effective in reducing impurities in aluminum alloys, preventing contamination of material, and dross build-up in the crucible. These specialist formulas can be applied to the interior surface of a crucible to help prevent chemical reactions between the metal and the crucible, acting as barrier to reduce impurities. PRO coating is relatively simple to apply. It can be mixed with water and applied to the crucible with a brush by a trained manual laborer. It also acts as a mortar, to repair areas that have been damaged or chipped, to maximise crucible life.
STAR coating is more advanced and gives superior results for clay-bonded as well as carbon bonded crucibles. It must be applied by a skilled supervisor using a specific spray gun to form a nano-particle scaled layer inside the crucible. It then needs to be sintered under specific conditions to ensure a strong bond. The result is a reduction of cleaning time, and significantly purer metals than those produced by standard crucibles.
Our PRO and STAR coatings are the result of our expertise in material science, our knowledge of application engineering, and our focus on the requirements of end users. This has enabled us to offer a superior product to customers. We have also boosted our capacity for these in-house, enabling us to serve mass markets where aluminium is increasingly being more heavily adopted, such as automotive and aerospace.
Mirco Pavoni, Global Technology Director, Molten Metal Systems at Morgan Advanced Materials
For further information please visit: http://www.morganmms.com/isopress-crucible