Investment casting businesses can benefit from significantly shorter leaching cycles for core support rods used in the production of turbine engine blades, following the development of a new range of materials which have been specifically optimised for this purpose, over quartz or alumina alternatives.
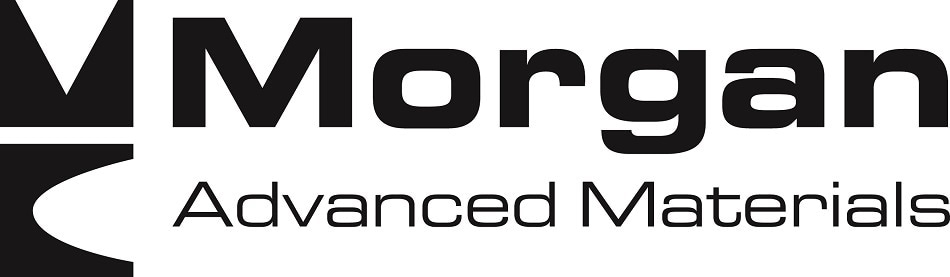
Developed by global materials leader Morgan Advanced Materials, the LEMA™ range of proprietary alumina-based materials will play a vital role in maximising throughput and capacity for turbine blade manufacturers. While typical alumina rods are renowned for their strength and load bearing capabilities, it can take several days to fully leach the materials, resulting in delays within the production process.
At a time when demand for turbine engine blades is expected to grow substantially over the next few years, based on the ramping build schedules of new engine programs such as CFM’s LEAP engine and Pratt and Whitney’s PurePower™ PW1000G family of engines, the enhanced leachability of LEMA™ rods shortens processing times significantly, allowing manufacturers to produce more components.
The improved leachability of LEMA™ compared with alumina, for which the leaching process is typically more challenging, can drive cost and time savings by improving first pass yields. Moreover, it can be used with less aggressive and more user-friendly leaching solutions, helping to overcome the cost and health & safety constraints associated with the use of more aggressive substances.
While quartz offers a cost-effective alternative to alumina in terms of leachability, it lacks the strength of alumina, making it less suitable for applications where part geometries and alloys require higher strength support rods. LEMA™ components are approximately 1.5 times stronger than quartz equivalents, resulting in higher quality castings with fewer defects.
We recognised leaching cycle times to be a pain point for the global investment casting industry and set out to develop materials to overcome this challenge. By carrying out extensive testing, we have optimised support rod materials to deliver enhanced leachability and strength, reducing cycle times and costs in the casting of turbine blades. The result is that users of our material can now better meet growing customer demand with lower costs and improved quality for the aerospace and industrial gas turbine industries. Our world-leading material science and focus on delivering solutions to our customer’s needs place us in a strong position to work with our customers to understand their specific requirements to optimise LEMA™ materials to best support their unique casting requirements.
Mark Forkapa, Global Marketing Director at Morgan Advanced Materials’ Technical Ceramics Business.
Contact our team form more information here