RUCKS Maschinenbau GmbH in Glauchau manufactures a thermoforming press which is used for making composite parts for the aviation industry. Three objectives were essentially taken into consideration, when the plant was designed: realising shortest possible cycle times, achieving reproducible results and a high degree of energy efficiency.
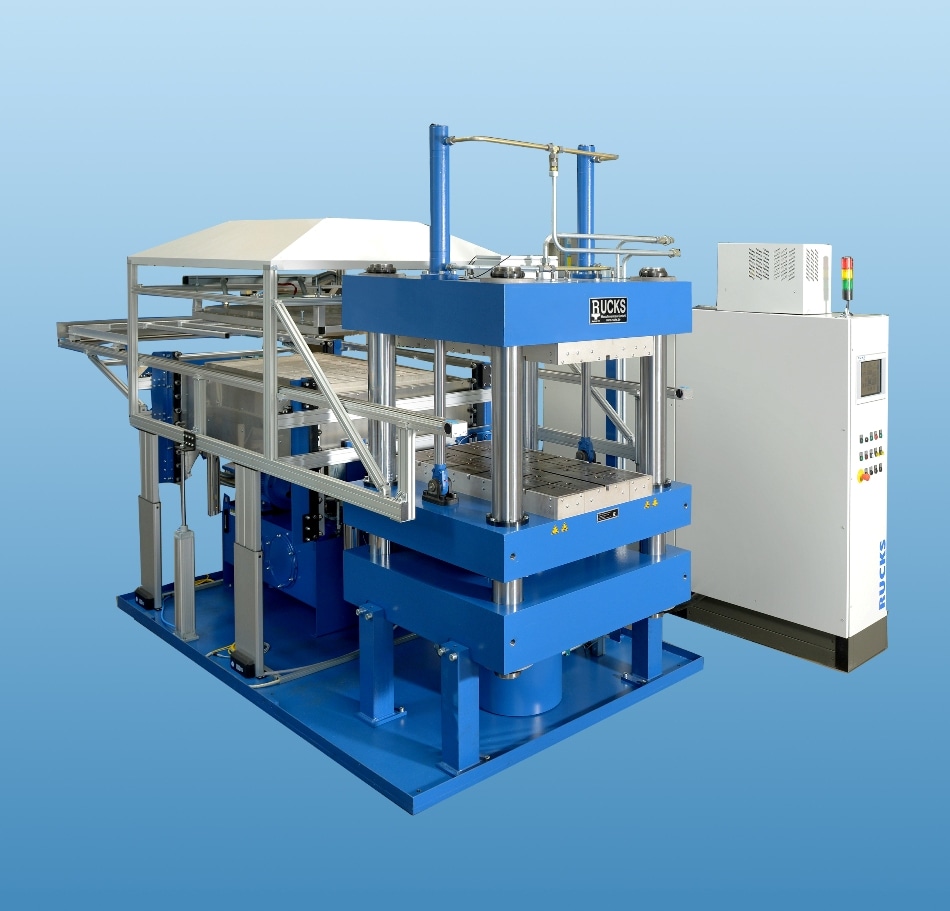
The centre part of the plant - optimised along these objectives - is an upstroke column press with a pressing force of 3000 kN and a closing speed of 200mm/s. In order to reduce the heat emission into the ambient area, the 600 x 1200 mm large press heating plates are divided each into three segments and provided with ample insulation. The division into segments enables the user to heat up exactly those areas that are needed for his tool. Thus he can reduce his heating costs optimally. A further feature of the heating plate installation is that the three segments of the heating plate can be shifted horizontally by 1.5 mm. Top- and bottom tool can therefore be aligned to each other perfectly.
The pre-heating station of the plant is provided with two ceramic infrared heaters. The maximum temperature of the upper and lower heaters is 570°C in order to heat up the prepregs as fast as possible. By electrically adjusting the height of the infrared heater, the heat for the work piece can be dosed precisely. The heaters are encased to become an infrared oven to increase the energy efficiency. As this is only opened for the automatic transport of the prepregs, it contributes further to the energy efficiency.
The loading station is positioned behind the pre-heating station. Here the prepregs are placed in a U-shaped transport frame. So-called “finger-plates“, which can be flexibly adjusted to the different prepregs within the transport frame, ascertain that the material is securely fixed.
A servo-driven linear system transports the material automatically from the loading – to the pressing station. The height-adjustable transport frame can be adjusted to the different tool heights in the press by means of synchronous multi-lifting devices. Due to the optimised coordination of the linear system, loading-, pre-heating-, and pressing station, the thermo-forming process is carried out fully automatic and guarantees reproducible results.
The machine is controlled by the control system “RUxx Logic HP®“ that has proved itself for years and is continuously further developed. With a graphically orientated user surface, touchscreen, online language selection, and internet communication, it fulfills the customers‘ requests for a modern and user-friendly operating concept. All processing parameters are recorded with the assistance of the RUDAS data recording system and can subsequently be evaluated and further processed.
We cordially invite you to visit us at the Composites Engineering UK 2018 (hall 2, booth E16) to obtain further information on this thermoforming press.