By using Ultimaker’s 3D printers, the Royal Netherlands Air Force are able to affordably create tools that fit the specific custom-made parts of an aircraft. Additionally, this technology has provided new opportunities to improve speed and efficiency at the base.
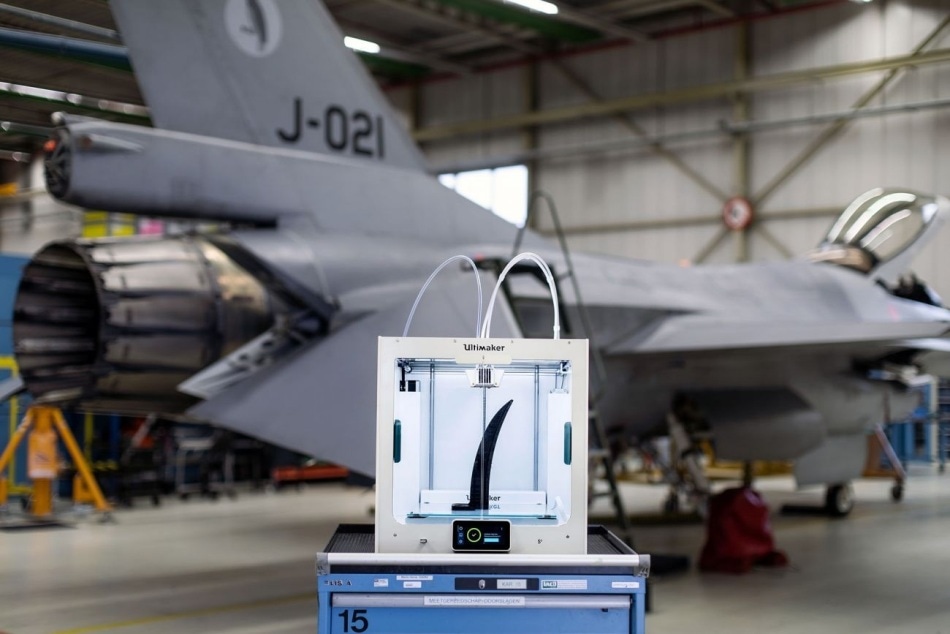
Company: Royal Netherlands Air Force
Industry: Engineering
Royal Netherlands Air Force - Introduction : The Royal Netherlands Air Force is the Netherland’s guardian of the skies. The military base in Woensdrecht is the primary maintenance location of the Air Force. Staff perform regular maintenance and repairs on aircrafts such as Chinooks, Apaches, NH90s, F16s, and many more. The base is also home of the Koninklijke Militaire School Luchtmacht (KMSL) which is the Royal Netherlands Air Force’s academy.
Challenge: The Air Force’s fleet contains a wide range of helicopters, fighter jets and large cargo planes. Performing maintenance on such complex and customised aircrafts can be a huge challenge: there are a lot of uncommon parts and systems to work with. The Air Force wanted a more accurate and simpler way to produce custom-made tools that will keep up with the high volumes of equipment, saving time and money.
Solution: Bas Janseen began to use Ultimaker printers in his workshops, which focus on gaining and sharing knowledge on manufacturing techniques like laser cutting and 3D printing. After seeing how popular this technology has been with the students and engineers, the base began to question how it could benefit maintenance speed and efficiency.
The air base quickly implemented 3D printers across the maintenance department, providing a way to affordably create tools that fit the specific applications in hours and to create special tools to adjust equipment. For example, certain helicopter parts are difficult to configure when they’re installed. By using a part printed on an Ultimaker printer, these adjustments can be made before mounting it into the helicopter.
Furthermore, for the metal parts that have to be CNC machined, the 3D printers are used for prototyping and fit-testing. This way, they can easily and cost-effectively iterate on designs before making the actual part.
Results:
- Time optimisation
- Process flexibility and reliability
- Innovation
Using a workshop of 3D printers means the air base were able to print numerous parts in the past two years, saving valuable time and money. For example, when jet engines are transported, certain openings need to be covered with a special cap. These parts are expensive to purchase and slow to be delivered. However, using the Ultimaker it only takes about two hours to print the part.
This technology has also enabled the Royal Netherlands Air Force to print bigger parts and start working with new, more advanced material. As Bas Janssen, comments: “Our transition to a fifth-generation Air Force can only be done with people who realise that they can be a part of the change now, not later. Ultimaker makes it possible to do just that: help people understand what additive manufacturing can do for them right now - without a long learning curve. The current software and hardware help people to make their ideas come to life.”
Ultimaker enabled the Royal Netherlands Air Force to:
- Improve maintenance speed and efficiency
- Work efficiently to maintain high levels of quality
- Manufacture the right tools, directly and locally
- Support local personnel with printing