Feb 15 2019
The ExOne Company announced its collaboration with Catalysis Additive Tooling (“Catalysis”) in the development of a new process for 3D printed tooling for low-to-medium volume production parts. ExOne is a global provider of three-dimensional (“3D”) printing machines and 3D printed and other products, materials and services to industrial customers. Catalysis, based in Powell, Ohio, is known for providing a complete solution which includes designing and 3D-printing tooling, as well as manufacturing parts.
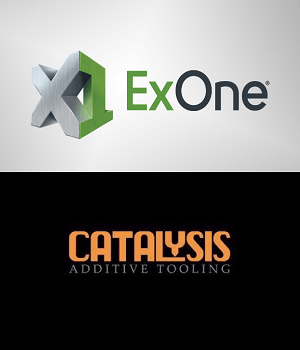
- ExOne’s 3D printing binder jetting technology is expected to provide Catalysis Additive Tooling customers with new and innovative tooling alternatives
- This collaboration presents a new process and go-to-market avenue for ExOne’s 3D printed part
New Tooling Process Developed Using Binder Jetting Technology
The collaboration between the two companies has resulted in the development of a revolutionary new rapid tooling process. The process starts with:
- An ExOne sand mold which is 3D printed using its binder jetting technology, based on a unique customer design
- The mold then receives proprietary coatings and becomes a re-usable tool to make a plastic, fiberglass, foam or other composite part by way of a more traditional injection, vacuum formed or cast process
Speed, cost and the ability to create a uniquely designed and reusable tool for low-to-medium run production are all benefits to Catalysis customers.
“We are pleased to add ExOne’s binder jetting technology to our family of 3D printing offerings. At Catalysis Additive Tooling we take an agnostic approach to 3D printing. We offer a number of different 3D printing technologies and select the best technology to meet and exceed our customers’ needs, based on the specific application. Given its speed and volume capabilities, we are especially interested in binder jetting for production parts. ExOne offers the best solution to satisfy this need,” said Darrell Stafford, Chief Executive Officer and President of Catalysis Additive Tooling. “With an ever-increasing number of applications, we are finding that our go-to technology for development of thermoforming, composite and foam tooling is binder jetting.”
Catalysis’ Process of Prototype-to-Mass Production
Catalysis pursues opportunities from prototype to mass production in a diverse variety of end markets, including automotive, appliance, aerospace, incubators, medical, packaging, recreation and more. Together with their strategic manufacturing partners, Catalysis has developed:
- Tooling and manufacturing processes for metal forming, vacuum forming and plastic injection at a cost and lead time which are often less than half the cost and time required of conventional manufacturing processes
- Additionally, 3D printing allows for the design of more complex tooling, removing constraints inhibited by traditional tooling design
Collaboration of ExOne and Catalysis
“This collaboration with Catalysis represents yet another avenue for us to deliver the benefits of our 3D printing binder jetting technology to the market,” said Rick Lucas, ExOne’s Chief Technology Officer. “Catalysis’ broad and innovative customer base seeks the significant cost and efficiency advantages that our technology provides. We are excited to partner with Catalysis in helping their customers to innovatively differentiate themselves in the marketplace.”
“We selected ExOne as our strategic partner because they are the proven global leader in binder jetting technology for industrial sand and metal components. Additionally, ExOne continues to advance the processes and print mediums to which their technology can be applied, further reducing costs and enhancing print quality,” added Mr. Stafford. “Their machine print resolution is an excellent fit for our thermoforming, composite and foam tooling applications. And, compared with other 3D printing technologies, ExOne’s binder jetting offers the most cost effective and efficient solution for these types of applications.”