The need for superior composite tooling materials is growing with the increasing use of composites in aerospace. Part fabricators are looking for tools with tighter tolerances and longer life. The market is searching for a trusted technology partner that is capable of providing world class innovation, manufacturing, and service.
Toray Advanced Composites has more than two decades of pedigree in composite tooling. The company’s AmberTool® composite tooling prepregs represents a comprehensive range that has been successfully sold and utilized across Europe.
Product Portfolio
Toray AmberTool® |
Resin |
Tg (onset)*1 |
Min cure temp |
Typical cure time and temperature*2 |
Tack life (days) |
Description |
Aerospace |
Industrial |
Motorsport |
Automotive |
Marine |
HX40 |
Epoxy |
203 °C
(397 °F) |
50 °C
(122 °F) |
12 hours at 65 °C (149 °F) |
8 |
Large tooling applications |
Ο |
|
|
|
|
HX42 |
Epoxy |
200 °C
(392 °F) |
50 °C
(122 °F) |
8 hours at 60 °C (140 °F) |
5 |
Proven system for aerospace |
Ο |
Ο |
Ο |
Ο |
|
HX44*3 |
Epoxy |
188 °C
(370 °F) |
50 °C
(122 °F) |
10 hours at 60 °C (140 °F) |
4 |
Industrial all-purpose tooling system |
|
Ο |
|
|
Ο |
HX50*3 |
Epoxy |
190 °C
(374 °F) |
40 °C
(104 °F) |
8.5 hours at 50 °C (122 °F) |
60 hours |
Excellent surface finish |
|
Ο |
Ο |
Ο |
|
HXR56*3 NEW |
Epoxy |
185 °C
(365 °F) |
40 °C
(104 °F) |
8.5 hours at 50 °C (122 °F) |
60 hours |
Two layer product for rapid lamination |
|
Ο |
Ο |
Ο |
|
TC40*4 |
BMI |
213 °C
(415 °F) |
182 °C
(360 °F) |
6 hours at 177 °C (350 °F) |
14 |
High service temperature |
Ο |
|
|
|
|
*1 after post cure *2 followed by post cure | Sourced from: *3 Europe *4 North America
Long term tool durability is achieved by combining low-temperature cure profiles with the high-temperature thermal performance after free-standing post-cure. Under Toray, these products, along with the company’s long term experience and value, have been brought to the North American market. The comprehensive range of Toray tooling products enables its customers to have complete tool design freedom and flexibility.
Toray’s AmberTool® tooling prepregs enable obtaining high precision for all machined and molded tooling applications, with a high degree of accuracy. Customers all over the world are provided complete technical support including bespoke training courses. In Europe, Toray facilitates a single supplier approach to all-composite tooling requirements, from a master pattern to material.
The Master Pattern
Selection of Materials
The selection of ideal materials for the master is very important when striving for optimum surface finish and dimensional accuracy. The following alternative combinations of materials are recommended in order to maximize the benefit of low coefficient of thermal expansion and excellent surface finishes:
(i) A superior epoxy tooling block coated with epoxy or vinyl ester surface coat (see Appendix V for suggested ancillary materials) or;
(ii) Epoxy / wet lay-up splashes. Currently, a number of alternative materials are used with Toray AmberTool®; however, any non-specified materials must be proven by physical testing before use.
Vacuum Integrity
In all instances, the master must be proved before lamination of the mold tool, by performing a “mock cure”. This will enable any potential issues such as lack of vacuum integrity or poor stability under pressure to be checked prior to any actual laminate construction.
Release Coating
An organic solvent such as Chemlease® Mold Cleaner EZ* must be used to thoroughly degrease the surface, thus allowing evaporation of all traces by drying at 60 °C (140 °F) for 30 minutes.
A wipe on, buff off technique is used to apply 1 - 2 coats of Chemlease® MPP 712 EZ, allowing 30 minutes between coats. A minimum of 1 hour should be allowed to cure at room temperature after the final coat.
The appropriate mold release is applied according to the manufacturer’s guidelines1. The tool should be heated to 60 °C (140 °F) for one hour to allow all release solvents to be driven off.
Preparation of Materials
The low temperature curing nature of the prepregs makes it important to optimize out life by keeping it in a frozen state at -18 °C (0 °F) prior to use. At this stage, the customer may find it suitable to construct a series of templates to enable single ply kits of materials to be prepared before lamination. The following points should be noted:
(a) Before opening the sealed packaging, the material must be allowed to reach room temperature. This prevents the formation of condensation on the material surface as it warms up.
(b) Materials should be cut on a clean stable surface that may not introduce any potential contaminants in final layup. Typical surfaces are polypropylene, glass sheet, rubber or nylon.
(c) Individual kits of a single ply should be prepared and stored in a freezer separately. This allows operators to make sure that a minimal amount of material is out of the freezer at any time - refer to Appendices I and III for ply type and orientation.
(d) Material can also be pre-cut into a series of conveniently cut squares, with typical dimensions of 0.5 m2, 0.33 m2 and 0.25 m2 (10, 6 or 2 sq. ft.)
Lamination to Tool
Appendices I and III show examples of work sheets with easy reference for ply type and fibre orientation. Appendix II shows other common laminate constructions.
The first and final plies will be lighter surfacing plies (lower fiber areal weights) with the composite core produced from the heavier material to bulk up the center of the laminate.
The first appropriate kit of materials must be removed from the freezer, and allowed to thaw. This is vital as it will prevent the formation of condensation on surface.
(a) Trim strips – Lay up a series of 45º trim strips into all external corners and tight radii, and make sure the pattern runs in a consistent direction for aesthetic purposes. Strips should be about 40 mm (1 ¼ inch) wide positioned uniformly on center of corner. Lay- up the first ply, carefully cutting and fitting, keeping in mind the following points:
.jpg)
(b) All pieces should be butt joined; no overlaps are permissible at this stage
(c) The weave pattern should be consistent if the fiber orientation is correct
(d) Material should be cut to fit into all corners and external radii, without disturbing the trim strips
.jpg)
(e) On all internal right-angled corners, allow the material to form around angle, but by no more than 5 mm (¼ inch)
.jpg)
(f) On large external radii, the material should be customized to fit in mid-point of the radius
.jpg)
(g) The material should not be pushed into corners with a sharp implement, as this may cause unseen damage to fibers and result in a structurally weakened laminate
This process is repeated throughout the laminate, with the following additional points for the heavier plies (refer to Appendix I):
Heavier Plies
(a) It is essential to stagger all joints between plies with a minimum of 18 mm (¾ inch) spacing for adjacent plies. Overlaps should be avoided if possible.
(b) Gaps should not be left under any circumstance as this is likely to cause voids in the completed tool
(c) The weave pattern should be consistent if the fiber direction is correct
(d) Avoid pushing material into corners with a sharp implement
.jpg)
Integrity Seal
Some tools will be subjected to an increasing number of autoclave cycles in service, and the tool surface may be damaged due to operators cutting on its surface or from impact damage. A leak path may form through the damage site and along a fiber bundle exiting at the tool’s trimmed edge. This can be prevented by laying up the tool laminate in squares. As an additional barrier to this form of leakage, it must be ensured that all fiber bundles are cut at least twice in the area between the tool edge and the strip where the vacuum bag sealant tape will be applied. This will build up a “picture frame” of cut plies around the vacuum bag seal area
.jpg)
Debulking (Reference to Appendices I & III)
The prepreg must be de-bulked at least at the stages stated i.e.:
- After ply 1
- Approximately every subsequent 3 plies
- After the final ply has been completed
This will help ensure uniform consolidation and remove air from the laminate before the final curing process. Sometimes, it is easier to laminate more complex shapes if more frequent debulks are used, but in these cases the time factor must be considered. If a laminate takes more than one day to lay-up, it must be de-bulked overnight to ensure that it remains in place.
.jpg)
(a) Cover the whole laminate surface with a perforated release film type P3, extending beyond the lay-up by about 25 mm (1 inch).
(b) Apply a breather coat of around 350 gsm (10.3 oz./yd2) in total to the surface. Customize to fit to avoid bridging. At this stage, the breather can be omitted from the tightest corners if not practical.
(c) Cover the laminate/assembly with a vacuum bag to ensure that sufficient slack has been provided to pull into all corners without any bridging.
(d) Apply full vacuum and leave for 20 minutes.
(e) Do not to lift up the previously laminated plies when removing materials from the surface afterward.
Preparation for Autoclave
.jpg)
(a) Place a thermocouple underneath the first ply of material on an area that is not a critical mold surface
(b) Lay in strips of glass rovings every 600 mm (24 inches) around the edge of the laminate continuing to the area on the periphery about to be covered with breather and described in (d)
(c) Cover the entire laminate with a non-perforated release film, and extend the edges by about 25 mm (1 inch)
(d) Apply a breather coat of around 700 gsm total weight, usually 2 plies of 350 gsm (10.3 oz./yd2). Customize to fit and ensure that all areas are interlinked. Fit an extra 2 plies around the periphery between the inside of the vacuum seal and the edge of the laminate. It is not advisable to miss a breather from any of the surfaces at this stage.
(e) Cover with a vacuum bag, making sure that sufficient slack has been provided to pull into all corners without bridging. At this stage, the vacuum pack will appear to be extremely bulky, and care must be taken to ensure that all materials remain in position as the vacuum bag pulls down.
(f) Apply full vacuum pressure and leave for 25 minutes before autoclave processing. Check for vacuum integrity and position of tucks in the bag.
Autoclave Cure
Curing must be performed under the strictest control possible because of the highly reactive nature of the resin systems, thus avoiding deviation and possible exotherm during cure:
1. Apply vacuum pressure and hold at 38 °C (100 °F) for 30 minutes
2. Apply 1.45 bar (21 psi) with vacuum
3. Vent to the atmosphere, then increase pressure to between 4.15 bar (60 psi) and 6.20 bar (90 psi)
4. Increase air temperature at 0.5 to 1 °C (1-2 °F) per minute ramp to the preferred curing temperature and cure for the stated minimum time.
Initial Curing Cycles (In Hours)
Important: Time and temperatures shown are minimums assuming a low mass master model/tool. Increase time at temperature for thicker or high mass master models.
For ultimate Tg, initial cure cycles must be followed by a higher temperature post cure. If the master used is thin walled, e.g. epoxy / wet lay-up splash, then an alternative cure should be used to include a dwell at low temperature. To meet this requirement, a dwell should be introduced at 40 °C (104 °F) for 2 hours, and then continue with the standard cure cycle.
Toray Ambertool® Prepregs
Temperature |
HX40 |
HX42 |
HX44 |
HX50 |
HXR56 |
TC40 |
35 °C (95 °F) |
|
|
|
|
|
|
40 °C (104 °F) |
|
|
|
18 |
18 |
|
45 °C (113 °F) |
|
|
|
12½ |
12½ |
|
50 °C (122 °F) |
40 |
18 |
22 |
8½ |
8½ |
|
55 °C (131 °F) |
24 |
11 |
15 |
6 |
6 |
|
60 °C (140 °F) |
18 |
8 |
10 |
|
|
|
65 °C (149 °F) |
12 |
5 |
7 |
|
|
|
70 °C (158 °F) |
9 |
|
5 |
|
|
|
75 °C (167 °F) |
6 |
2½ |
|
|
|
|
80 °C (176 °F) |
|
|
|
Exotherm risk increases |
|
182 °C (360 °F) |
|
|
|
|
|
See section "Toray Ambertool® TC40 BMI Initial Cure & Required Post Cure" |
Toray Ambertool® TC40 BMI Initial Cure & Required Post Cure
1. Hold laminate under minimum 28” Hg vacuum at room temperature for at least 24 hours prior to cure. Maintain a connection to vacuum during transfer to the autoclave.
2. Maintain initial 28” Hg minimum pressure to bag and increase pressure to 95 +/- 5 psi at maximum 1.5 psi/minute while ramping tool to 129 °C (265 °F) ±10 °F at max 1 °C (2 °F) / minute.
3. Hold at 129 °C (265 °F) ±5 °C (10 °F) for 65 ± 5 minutes based upon lagging thermocouple except proceed to next step if lead thermocouple has been at 129 °C (265 °F) ± 5 °C (10 °F) for more than 90 minutes.
4. Ramp part temperature to 182 °C (360 °F) ±5 °C (10 °F) at a maximum 2 °C (4 °F) per minute. Hold part at 182 °C (360 °F) ±5 °C (10 °F) for 120 to 360 minutes based on the lagging thermocouple.
Removal from Master
If the tool requires a backing structure (i.e. to prevent a large tool from distorting under its own weight), it should be fitted at this stage prior to release from the master. Stresses should not be induced when removing the tool from the master, as it will be mechanically weak at this stage. The mold should be gently eased off the master and lifted uniformly all around.
Post Cure
It is essential to set up the tool with appropriate support around the base with its weight distributed as evenly as possible. Perform any one of the following curing schedules from the product data sheet E.g. 120 °C (248 °F) end use = 140 °C (284 °F) maximum post cure temperature plus dwell for 6 hours.
Post-cure schedule A (for Toray AmberTool® HX and HXR series products):
Ramp |
1 °C / min to 60 °C (140 °F) |
Dwell for 2 hours |
Ramp |
1 °C / min to 90 °C (194 °F) |
Dwell for 1 hour |
Ramp |
1 °C / min to 120 °C (248 °F) |
Dwell for 1 hour |
Ramp |
1 °C / min to 150 °C (302 °F) |
Dwell for 1 hour |
Ramp |
1 °C / min to 170 °C (338 °F) |
Dwell for 1 hour |
Ramp |
1 °C / min to 190 °C (374 °F) |
Dwell for 6 hours |
Cool to 50 °C (122 °F) at 2.5 °C (4.5 °F) / min |
.jpg)
In addition, an alternative post-cure schedule can be used as follows for all Toray AmberTool® products.
This is the post-cure schedule proposed for the TC40:
.jpg)
To retain maximum end use properties, post-curing should be carried out as close as possible to the above schedules. In situations where the end use temperature is likely to be lower than 180 °C (356 °F), the post cure can be modified if the final stage is at least 20 °C (68 °F) higher than maximum end use temperature, and held at this temperature for the appropriate final dwell time of 6 hours. E.g. 150 °C (302 °F) end use = 170 °C (338 °F) maximum post cure temperature plus dwell for 6 hours.
Release Preparation / Priming
The correct regime should be considered for coating and releasing the mold at this stage:
(a) Surface should be washed thoroughly with clean water and allowed to dry
(b) Clean surface with mold cleaner2, apply with a clean 100% cotton cloth. While the mold surface is still wet, use a second clean cloth to vigorously wipe the mold dry, until the mold is “squeaky clean” by thumb rub test. Exchange saturated clothes frequently for new ones and repeat several times until the entire residue is removed. Alternatively, test on an “off part” area with a non- silicone adhesive tape.
Mold Preparation and Primer (Follow Manufacturer’s Guidelines for Usage)
(c) For a high-quality finish, apply 1 or 2 coats of mold sealer EZ3 by wipe on / wipe off, allowing 30 minutes between each coat and at least 1 hour at ambient temperature to finally cure. Severe damage could be caused to the mold if this product is used without a release agent.
(d) Apply 1 to 2 coats of mold sealer4 according to manufacturer’s instructions. Saturate a clean cloth and wipe on a smooth film of no more than 0.6 m2 (6.5 sf) at a time. When the film starts to evaporate at the edges, wipe the surface with a second clean cloth using a circular motion. Repeat until the entire mold surface has been covered. Allow 1 hour at ambient temperature to cure before applying for mold release.
(e) Apply 6 wipe on / polish off coats of a release agent allowing 15 minutes between coats and 30 minutes for a full cure at ambient temperature. Follow the manufacturer’s instructions.
(f) For touch up coats of a selected release agent, apply 2 coats as before.
In Service Maintenance
Points in general to note are:
(a) Do not use excessive force when releasing from mold
(b) Avoid cutting into mold surface during lamination
(c) Follow release agent data sheets as recommended
(d) Avoid any aggressive abrasion on the surface, i.e. when removing components from mold
(e) Different release agents and different prepregs can have a wide variation in effects on the surface of the mold
Re-Priming Mold Surface
Surface deposits can be manually removed by fine abrasion with either cutting paste or fine nylon scouring pads. The use of mechanical means is generally not recommended.
For touch up coats, it is best to do preventative maintenance, hence reapply after 15 releases, or as trials determine. Wipe on and polish off 1 coat and allow at least 15 minutes before recommencing lay-up.
(a) The surface should be cleaned with mold cleaner, cloths should be frequently changed, and liberal quantities of cleaner should be used
(b) Take mold to 60 °C (140 °F) for 30 minutes to remove all moisture/solvent
(c) Revert back to 9 (d) for all release preparation/priming
References and Further Reading
* Alternate mold release cleaners can be used based on manufacturer’s recommendations.
1 Europe: Chemlease®2185; North America: Frekote® 44-NC or 770-NC
2 Europe: Chemlease® Mould Cleaner EZ; North America: Frekote PMC Mold Cleaner, or equivalent
3 Europe: Chemlease® MPP 712 EZ Sealer; North America: Frekote CS-123 mold release sealer
4 Europe: Chemlease® 15 Sealer; North America: Frekote B15 sealer
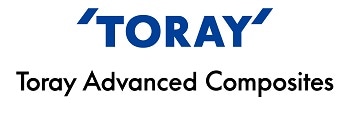
This information has been sourced, reviewed and adapted from materials provided by Toray Advanced Composites.
For more information on this source, please visit Toray Advanced Composites.