As a world leader in the field of polyurethane-based resin systems, Henkel is actively expanding its Loctite MAX polyurethane (PU) matrix resins portfolio by a family of high-performance materials based on epoxy. This resin portfolio is targeting the market of demanding automotive composite high temperature applications, such as wheels. Loctite MAX5 NextGen exhibits exceptional clarity for a rich carbon look, while upcoming Loctite MAX6 combines ultra-high heat resistance with unique toughness.
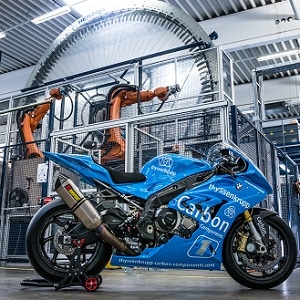
Higher-Performing Composite Solutions for Automotives
At JEC World 2019 in Paris from March 12 to 14, Henkel will highlight the latest developments of its Loctite MAX PU and epoxy matrix resins technology, addressing the continuing need for both lightweighting and cost-effective as well as higher-performing composite solutions for the automotive industry. The trend is particularly evident in the segment of wheels, where besides Loctite MAX5 the new Loctite MAX5 NextGen and MAX6 resin systems can make a significant contribution to weight-savings, enhanced productivity and customization of parts showing superior thermal, mechanical and visual properties.
Most recently, Loctite MAX5 has helped ThyssenKrupp Carbon Components pioneer a new generation of ultra-light braided carbon motorcycle wheels. The matrix resin provides short mold filling times as well as fast curing. Each set of these composite wheels can save up to 1.8 kg of rotating mass vs. conventional forged aluminum designs.
This translates into significant benefits in bike handling and fuel efficiency. The wheels were developed in close collaboration with Henkel to optimize the manufacturing process and meet the extremely tight tolerances specified by the manufacturer. They have already received road clearance by the Federal German Motor Transport Authority for use on various different machine models.
Resins for Leaf Springs and Wheels
“Following the success of our Loctite MAX2 resin for leaf springs and MAX5 resin for wheels, we have been focusing our efforts in this technology on several key challenges especially in the market of high-performance composite and hybrid wheels,” says Konrad Brimo Hayek, Senior Business Development Manager Chassis & Electronic Systems at Henkel.
“Apart from helping OEMs and Tier 1 suppliers reduce weight on modern vehicles and two-wheelers, we had identified a growing need for composite wheel materials that would also provide higher heat resistance and toughness while satisfying demands of greater production volumes and customized surface aspect.”
New Grades with Distinct Added-Value Characteristics
Henkel’s innovative Loctite MAX matrix resin systems exhibited at JEC World 2019 will include two new grades with distinct added-value characteristics:
- Loctite MAX5 NextGen, a 2-component epoxy-based formulation building on the proven MAX5, offers a glass temperature of 200 °C (Tg, measured by differential scanning calorimetry, DSC) and a toughness value of K1C >1.1 for high-temperature applications with outstanding mechanical integrity. In addition, the next-generation material also provides exceptional clarity for a rich carbon look. Loctite MAX5 NextGen can be processed using all common liquid molding techniques, including high-pressure resin transfer molding (HP-RTM) for higher volume production rates.
- Loctite MAX6, designed to meet even higher performance requirements in terms of heat resistance and toughness, offers a superior Tg of >270 °C and a K1C of >1.0 for components operating at ultra-high service temperatures.
Both resins are mainly targeting the OEM and Tier 1 composite wheels market as well as the consumer segment of after-market wheels and are globally available for testing. Wheels manufactured in series production using Loctite MAX5 matrix resin systems will be on display at JEC.
Many Proven Benefits and Series of Application
Major benefits proven in several existing Loctite MAX series applications include rapid mold filling, thorough fiber impregnation and fast curing rates. In contrast to comparable aluminum designs, composite wheels molded with Loctite MAX matrix resins can cut the weight of automotive wheels by as much as 30 to 50 percent per unit.
Notable other applications already on the road include lightweight leaf springs in MAX2 on the suspension of a rear axle concept implemented across various Volvo models.
For component manufacturers, Henkel’s Loctite MAX matrix resin technology shows a particularly flexible, time and energy saving processing window when compared with other PU and epoxy resins. In HP-RTM molding trials for sandwich parts with a 3A Composites AIREX® foam core, glass and carbon reinforced Loctite MAX2 achieved excellent results at significantly lower pressures, higher injection rates and shorter cycle times.
Balancing the Pressure & Curing Temperature
“One of the challenges to meet in these tests was to balance the pressures and curing temperatures at a level low enough to maintain the stability of the foam,” explains Brimo Hayek. “Our Loctite MAX2 matrix resin proved to offer the best solution, with an enormous potential for further minimizing the cycle time.”
Henkel’s advanced matrix resins are part of the company’s strategic approach to build and strengthen its material, process and engineering expertise for large-series structural components across the entire manufacturing chain.
Visit Henkel at hall 6, booth M58, for first-hand information about the supplier’s composites know-how, portfolio and technology during this year’s JEC World at the Paris Nord Villepinte Exhibition Center from March 12 to 14.