Next level in evolution of thermoplastic composites: JEC World 2019, (12–14 March in Paris), saw the roll-out of HUESKER's ready-for-market W8SVR Neolaminate. Improved properties, notably in terms of strength, stiffness and weight, enable it to outperform conventional thermoplastic composites such as organosheets, thereby making it ideal for complex and challenging lightweight applications.
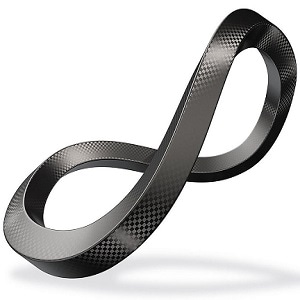
The Evolution of Thermoplastic Composites
It is stiffer, smoother and stronger. W8SVR opens up new options for engineers and designers in a variety of sectors. "W8SVR sets new benchmarks wherever the requirements placed on material properties are particularly stringent," explains Heiko Pintz, Senior Product Developer for Composites at HUESKER. The Neolaminate is a continuous-fiber-reinforced thermoplastic (CFRTP) composite, developed as a refinement of organosheets.
Neolaminate Combining Lower Weight with Higher Strength and Stiffness
W8SVR achieves the same strength and stiffness as existing solutions while being up to 20% lighter. Even with complex geometries, its exceptional surface smoothness unlocks a wealth of new product design options, e.g. through the simple application of film or coated finishes. Where flexural stiffness is the focus of functional requirements, the Neolaminate excels by offering up to 35% less deformation than conventional composites for the same thickness or weight.
Unbeatable Performance with a Light Touch
- The significant improvement in properties is achieved through the use of pre-stretched continuous fibers, unidirectionally arranged in a polymer matrix.
- In producing W8SVR Neolaminate, these so-called "UD tapes" are then processed, as required, practically without undulation (as wovens) or completely without undulation (laid fabrics).
- Added to this is the particularly strong bond between fibers and polymer matrix material.
- Direct mobilization of the unidirectional fibers optimizes resistance to the acting forces.
- Moreover, the fiber orientation can be freely chosen by the customer in order to best resist the expected loads in a particular part or component.
- At the same time, the near-net-shape production of Neolaminates leads to a considerable reduction in waste, compared to the use of conventional organosheets.
- HUESKER uses industrial machinery to manufacture the Neolaminates in widths of up to 2,800mm.
"At the trade show, we are going to flesh out the theory behind our Neolaminates by giving visitors impressive insights into their practical application," says Pintz. "The global premiere at JEC World will therefore include a presentation of samples and end products for lightweight construction." The potential applications of W8SVR are every bit as multi-faceted as its benefits. A wide range of sectors – from aeronautics and transportation to sport and recreation – stand to benefit in equal measure from use of the Neolaminate.