At CHINAPLAS 2019, BASF will introduce more than 20 innovative material solutions to help make the next generation of electric vehicles not only energy efficient but also comfortable and stylish through highly-customizable designs. A range of these solutions will be showcased in concept cars designed by GAC R&D Center, with advanced prototyping support from Creation Center®, BASF’s dedicated touch-point for engaging and inspiring designers.
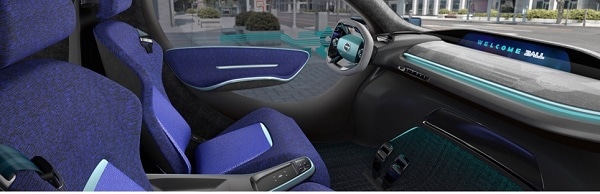
Improved Interior Air Quality throughout the Vehicle
BASF materials throughout the vehicle have been designed to minimize or eliminate emissions volatile organic compounds (VOCs) and avoid organic solvents. At the same time, new BASF technologies installed in the car can actively remove interior pollutants to improve air quality.
Innovative Solutions for Unlimited Design Options
Thanks to new 3D printing solutions for laser sintering and new clearcoat chemistry for anti-scratch exteriors, automotive designers can enjoy unprecedented freedom in customization of electric vehicles for a new generation of drivers and passengers. Additionally, new polyamide materials and new applications can offer a stylish look combined with durability to resist scratches, ultraviolet light, and abrasions such as in car washes.
Materials for Passenger Safety and Comfort
New foam technologies from BASF offer better comfort for drivers and passengers, while also maximizing interior space. Additionally, durable materials for gears enable seat rotation at a wide range of temperatures.
Battery Technologies Boost Mileage and Enhance Safety
BASF’s portfolio of application-specific battery cathode active materials supports high energy density and safety. BASF will also showcase materials and solutions for the battery coolant, the battery cell filler, and pack liner for fire-insulation, all of which contribute to the safety and efficiency of batteries for electric vehicles.
Other innovative automotive applications that will be introduced at CHINAPLAS 2019:
- New safety options include bullet resistant safety glass made with thermoplastic polyurethane in the mid layer to provide optical clarity, as well as body panels made of BASF polyurethane which offer excellent impact resistance.
- Electromagnetic shielding properties can be achieved with parts made with Ultramid® polyamide (PA) and Elastolit® polyurethane (PU).
- Applications that require electromagnetic shielding include the battery upper cover, power control unit and electronic control unit.
- Electromagnetic shielding improves the safety and performance of the components as it reduces disturbances generated from external sources affecting the electrical circuit inside the components.