Volume Graphics has announced the latest generation of its software solutions for non-destructive quality assurance with industrial computed tomography (CT): Version 3.3 of VGSTUDIO MAX, VGSTUDIO, VGMETROLOGY, and VGinLINE.
The company is the leading provider of industrial CT software, according to management consultants Frost & Sullivan (basis: "2018 Global Industrial CT Software Market Leadership Award"). Volume Graphics’ VGSTUDIO MAX software is used for the analysis and visualization of industrial computed tomography (CT) data and covers all requirements related to metrology, defect detection and assessment, material properties, and simulation.
Using the new version, customers can determine the surfaces of multi-material components, export measurement and analysis results to store them centrally in quality-management software, automate inspection processes more flexibly based on text recognition, and translate real CT data into volume meshes for simulation.
To further support their customers, Volume Graphics has also added a new Technical Consulting unit that provides professional consulting and evaluation services.
“With version 3.3 of our software solutions, we are once again laying the foundation for customers to make their processes smarter,” says Christof Reinhart, CEO and co-founder of Volume Graphics GmbH.
“For example, using the new data export, metrology data derived with the tremendous measurement capabilities of our software can be seamlessly shared with QA systems, where the values can then be combined and checked over time. More than ever before, this new feature enables customers to better integrate leading-edge CT technology into their existing software landscape. The new export feature is based on the native support of the widely used Q-DAS format, which makes using results in third-party statistical or analysis software especially easy.”
An overview of the innovations in VGSTUDIO MAX 3.3:
Multi-material surface determination
Multi-material surface determination
- A new mode of the local-adaptive-surface determination enables the simultaneous determination of the surfaces of each material within a volume in one go
- This significantly simplifies the geometric dimensioning and tolerancing of multi-material objects, e.g., the position of metal pins of a connector relative to the plastic housing
- The new mode also facilitates segmentation of multi-material objects
Support of native data export in Q-DAS format
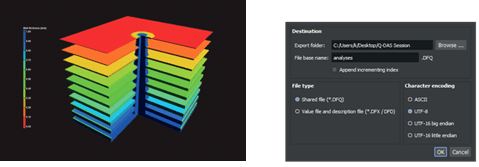
(Left) Wall-thickness analysis: One of the many analyses whose results can now be exported in Q-DAS format. (Right) Q-DAS export dialog.
- There is now native support for data export in Q-DAS format for both VGSTUDIO MAX and the VGMETROLOGY metrology solution, as well as the VGinLINE solution for automated CT inspection
- Companies that still work with traditional measurement systems can switch to this much more comprehensive CT measurement technology without encountering software hurdles or having to forego their established processes for further statistical evaluation
- Export of detailed, CT-based measurement and analysis results (coordinate measurement, nominal/actual comparison, wall thickness analysis, porosity/inclusion analysis, fiber composite material analysis) is now enabled in the common Q-DAS data exchange format
OCR-based automation
- New optical character recognition (OCR) allows customers to read out text in CT scans, such as object identifiers, and store the recognized text in their meta information
- In automated inspection workflows, cavity markers in CT scans of injection molded or cast components can be recognized and the right reference object or the appropriate analysis in VGinLINE jobs can then be selected depending on the respective cavity
- At the same time, the recognized text improves the traceability of the results, since the information about the cavities can be included in the reports
Volume meshing for simulations
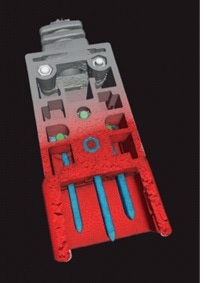
Volume Meshing
- With the new Volume Meshing Module, users can create accurate and high-quality tetrahedral volume meshes from their CT scans for use in mechanical, fluid, thermal, electrical, and other FEM simulations in third party software
- This is based directly on the subvoxel-accurate surface determination for scanned parts or material samples consisting of one or more materials
- The individual components of multi-material objects are translated into volume meshes with congruent tetrahedron faces and shared nodes at material interfaces
- The complete workflow from CT scan to volume mesh is covered
- Generated volume meshes can be exported in common .pat and .inp file formats
- Each cell of the generated volume mesh can be loaded with additional information required for simulation, such as fiber orientations, fiber volume fractions, porosity volume fractions, or gray values
Full service support with technical consulting
- Backed by 20 years’ experience in industrial CT, the new Technical Consulting unit analyzes the specific requirements of each customer’s application(s), creates optimal software configurations and general CT hardware specifications, and offers complete evaluations as a contract service