In collaboration with SGL Carbon, Chinese automotive manufacturer NIO has developed prototypes for battery enclosures made of carbon-fiber reinforced plastic (CFRP) for its NIO high performance electric vehicles. Thanks to CFRP, the battery enclosure is extremely lightweight, stable and safe.
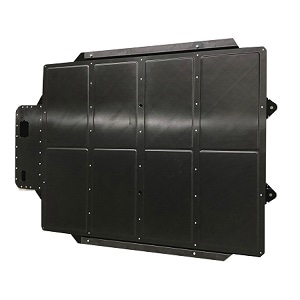
40 Percent Lighter than Comparable Aluminum Solutions
The entire battery enclosure, including the batteries, can be changed at swapping stations of NIO within just three minutes. NIO presented the swap concept at NIO Day in December 2017 for the first time and now demonstrated the actual system along with various technological innovations including the CFRP battery enclosure live at the 2019 Shanghai Auto Show last week.
Battery Enclosures for Electric Vehicles
“Commercial battery enclosures for electric vehicles are mainly made of aluminum and steel. In comparison, the CFRP battery enclosure is around 40 percent lighter. Other benefits include the enclosures’ stiffness and the approximately 200 times lower thermal conductivity of CFRP compared to aluminum, which better shields the battery from heat and cold. Plus, the composite also offers excellent values in terms of water and gas leakage tightness and corrosion resistance,” states Sebastian Grasser, head of market segment Automotive in the Composites – Fibers & Materials business unit at SGL Carbon.
“Lightweight technology is one of the core elements in NIO technology roadmap. Using composite material especially the high-performance carbon fiber in battery enclosure system, our vehicle can achieve better dynamic performance, increase range, and obtain remarkably high energy density of the battery pack (over 180 Wh/kg). These features fit perfectly to the core values of NIO brands of ultimate product and system efficiency” states Bin Wei, Senior Manager of Lightweight Engineering at NIO.
Outstanding Battery Enclosure Characteristics
These outstanding battery enclosure characteristics mainly owe to the bottom and cover plate design, combining a sandwich core with multiple layers of carbon fiber non-crimped fabrics. SGL’s own Lightweight and Application Center was responsible for developing the tool to produce the bottom and cover plate. Along the fully integrated value chain, carbon fiber is produced for these components at the SGL plants in Moses Lake and Muir of Ord, processed into non-crimped fabrics in Wackersdorf. Besides producing the bottom and cover plate, the SGL site in Ried, Austria, also assembled the individual components.
SGL Carbon expects demand for lightweight solutions for battery enclosures in the automotive sector to grow rapidly in the next few years due to increasing electromobility. The company is already working with various partners to continue developing different battery enclosures made of composites with the aim of scaling them for electric vehicle batteries of all sizes and designs.