Centorr Vacuum Industries announced it has added new furnace capability to its APPLIED TECHNOLOGY CENTER for customer use for process proofing, toll work, and process development runs.
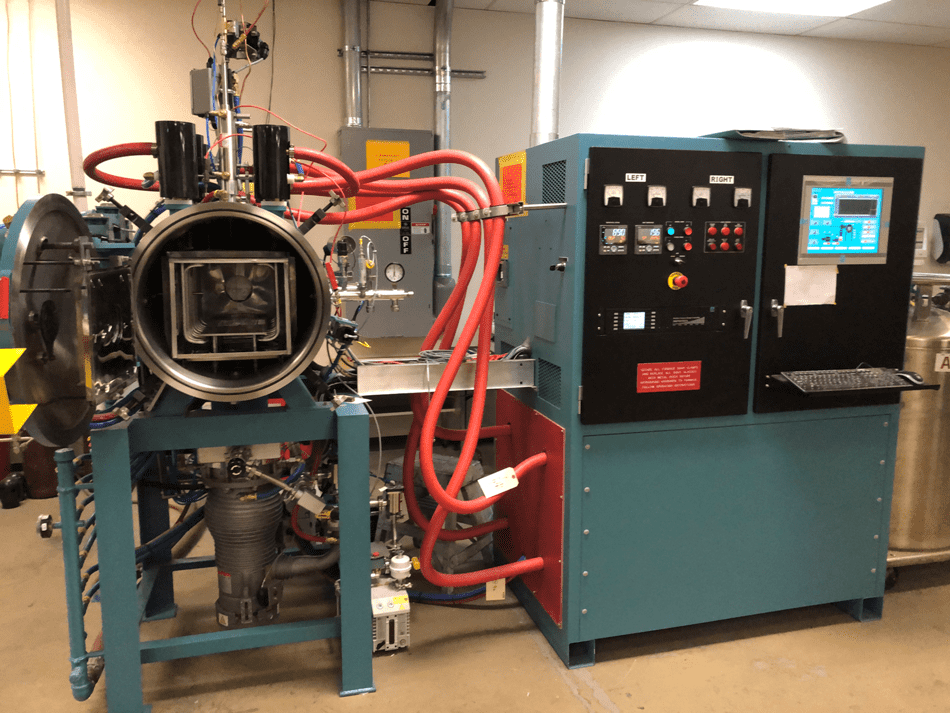
The new furnace is based on Centorr’s successful Super VII platform (8”w x 8”h x 20”d useable volume) and will join two smaller System VII furnaces (6”W x 6”h x 15”d) and induction melting furnace, and a continuous belt furnace already in use.
This newly updated 2nd Generation Super VII design comes with several innovative features to allow the processing of a wide variety of metals, hardmetals, ceramics, and carbon/graphite composites. The furnace can be used for low temperature degassing, heat treating, annealing, brazing, and sintering of a variety of materials.
The new Super VII will be capable of operation with a refractory metal W/Mo hot zone up to 2000 °C in high-vacuum and positive pressures of inert Ar and N2 gases, as well as 2000 °C temperatures in positive pressure Hydrogen and Helium. The system will also be capable of partial pressures of inert gas from 1-1000 microns and partial pressures of H2 gas from 1-10 torr.
Because this new furnace design is built for flexibility, the refractory metal hot zone can be swapped out for a graphite hot zone with graphite heating elements and insulation in less than two (2) hours, allowing operation in vacuum or positive pressures of Ar or N2 gas to 2300 °C.
The unit also comes with a 1.5 HP cooling fan to allow for short furnace profiles and better modeling of heat treat runs requiring faster cooling.