Vacuum instead of muscle power: Packages of various sizes are often still moved manually in internal logistics. A solution at GYMA Deutschland GmbH shows how energy-sapping handling processes can be organized ergonomically with FIPALIFT tube lifters.
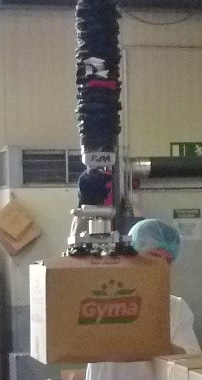
"Two burgers with fries and spicy salsa dip, please." The dip could easily come from GYMA Deutschland GmbH (www.gyma.eu) – an established brand manufacturer with an extensive product range of sauces. Since 1992 the company has been under the ownership of the French GYMA Group, the head office of which is in France. Along with fast food chains, its customers include wholesalers, freeway service areas, snack bars, canteens, caterers, airlines and companies in the food industry. An effective supply chain is required to guarantee all of these customers immediate availability. Customers are supplied promptly with the container size required – from individual portions and small packs, through bottles, to large packaging such as canisters and containers. Around 70 employees work in two shifts at the German headquarters in Kamp-Lintfort to provide smooth manufacturing and internal logistics. Approximately 25,000 tons of sauces leave the German plant every year.
The Task: Palletizing heavy boxes with minimum effort
On the container packaging line, canisters with ready-made sauces are packed in boxes of various sizes and then palletized. A standard box with dimensions of 390 x 270 x 290 mm holds four canisters of 5 kg each. Two canisters of 5 kg each fit in another customized box with dimensions 270 x 190 x 290 mm. The employees are therefore moving up to 20 kg – a heavy load. GYMA Deutschland was therefore looking for an ergonomic solution that would ease the burden on its employees in the packing process and also provide a high level of occupational safety. In addition, the aim was to find a new handling solution that could be converted from one box size to another several times in one shift in just a few steps – as quickly and easily as possible.
The Solution: A complete set with a tube lifter FIPALIFT Smart
The attention of Head of Production Rainer Jacobs was drawn to the tube lifters FIPALIFT by an email campaign. He contacted Mr. Bendrat, Sales Director Germany West, who came up with a solution with his colleagues, in close collaboration with GYMA. The complete set for handling packages consists of a tube lifter FIPALIFT Smart with a load capacity of 35 kg, a dry-running vacuum pump, a column mounted jib crane and a cross beam with four bellows vacuum cups made of the composite material Varioflex®, a special polyurethane with two different hardnesses. The sealing lip is soft and flexible, the stable body allows rapid resetting. With its excellent cycle life and superior gripping force, it is perfect for precise handling of abrasive products.
The advantages: Maximum ergonomics and flexible use
With the tube lifter FIPALIFT, three boxes a minute can be palletized with minimal effort. Rainer Jacobs is a big fan of the new handling solution: "The tube lifter FIPALIFT eases the burden on us considerably. I am now able to use employees in this area who were previously no longer able to do the heavy physical work throughout an entire shift because of their age or physical capabilities. That makes the work a lot more enjoyable."
The smooth implementation was also appreciated: "FIPA gave us professional advice and delivered the project quickly. Above all, we were impressed by the value for money."
GYMA has now ordered a second cross beam so that the tube lifter FIPALIFT can be refitted flexibly for other box sizes.