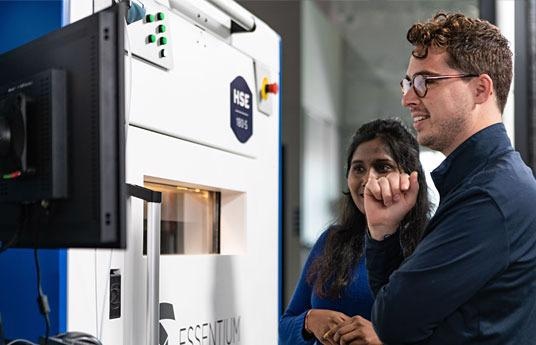
THE HSE 180•S 3D printing platform. Image Credit: Essentium
A new approach to advanced additive manufacturing could deliver faster and more efficient maintenance, repair and overhaul services for aircraft.
The maintenance of aircraft is a significant challenge for aerospace operators. The need to quickly repair machines and get them flightworthy, while also keeping costs low, is a high-pressure business.
Replacement parts for aging aircraft can be difficult to source as manufacturers tend to be reluctant to produce parts for outmoded, no-longer built, vehicles. This is especially true if those manufacturers don't expect to supply such parts more than once or twice every few years.
These demands converge to make a method of manufacturing custom reliable replacement parts quickly and easily, highly desirable. Aircraft operators are beginning to invest in 3D printing platforms that can provide custom-made devices without the need to commit to the creation of molds and specific tooling methods.
An example of such a project is the US Airforce (USAF) and its collaboration with Essentium¹— a Texas-based provider of additive manufacturing solutions. The two have united to pioneer the production of advanced additive manufacturing solutions to be deployed over applications such as tooling, ground support, and crucially maintenance, repair and overhaul (MRO).
We're really doing a deep dive into the applications and providing materials that can be used across the Air Force and the U.S Department of Defense.
Elisa Teipel, Co-founder and Serving Chief Development Officer, Essentium
The project will supply parts for aircraft and ground vehicles, focusing on providing support for older aircraft to sustain them, extend their lifecycle and negate the need for costly replacements.
The USAF estimates that almost 10000 replacement part requests are delayed each year, often because manufacturers can't supply the part. Often these delays cause vital craft to sit in hangers and on runways at critical times. The more creative and custom-based service provided by 3D printing could help make this a thing of the past.
Rapidly Producing Parts When and Where They're Needed
The team spearheading the USAF-Essentium collaboration will develop new materials and processes using the manufacturer's high-speed extrusion (HSE™) 3D printing system. The company says that this platform is up to 15 times as fast as leading competitors.
In addition to producing parts rapidly, the system can slice down the time needed to certify parts. The system also is of sufficient size to allow for the mass production of parts.
"Essentium demonstrated it has the expertise and capabilities to create parts with consistent replication using the Essentium HSE 3D printing platform," adds Teipel. "We'll work together to drive additive manufacturing technology forward and for faster aircraft repairs that massively reduce time to deliver parts to keep our warfighters ready."
The time taken to get aircraft back in the skies will also be vastly reduced because the system being developed by the USAF-Essentium collaboration can be deployed in situ on the ground at bases or hangers where aircraft are serviced.
A Wider-Range of Production Materials
Different aircraft parts perform different functions and therefore require a wide range of physical properties. Fortunately, the HSE printer is an open platform, which means that it can be adapted to use a wide variety of materials.
This includes materials with high temperature and chemical resistance and substances with anti-corrosive properties. All of these are necessary for aircraft parts due to frequent exposure to various lubricants, fuels and additives.
This variety is enabled by what the team calls the HSE Hozzle. The oddly named component is a nozzle that is equipped with both an integrated heating and temperature sensing unit — which can heat materials up to 550⁰C in just 3 seconds — and a sapphire tip that allows for the extrusion of high-performance materials.
The system can also be used to create a variety of molds and tools in addition to parts for immediate use, all without the need to re-tool. This means an unparalleled range of creativity and development.
For the USAF the shift towards the use of additive manufacturing solutions like the HSE 3D printer represents a forward-thinking move away from the dependence on more traditional supply chains.
That’s another key breakthrough. It used to be that you could design things as an engineer, but you couldn’t manufacture. With additive, you can design things that you can print that you could have never made before.
Elisa Teipel, Co-founder and Serving Chief Development Officer, Essentium
References
1. Essentium, [https://www.essentium.com/]
Disclaimer: The views expressed here are those of the author expressed in their private capacity and do not necessarily represent the views of AZoM.com Limited T/A AZoNetwork the owner and operator of this website. This disclaimer forms part of the Terms and conditions of use of this website.