IoT-enabling technology for solutions providers and systems integrators, across smart agriculture, construction and waste management
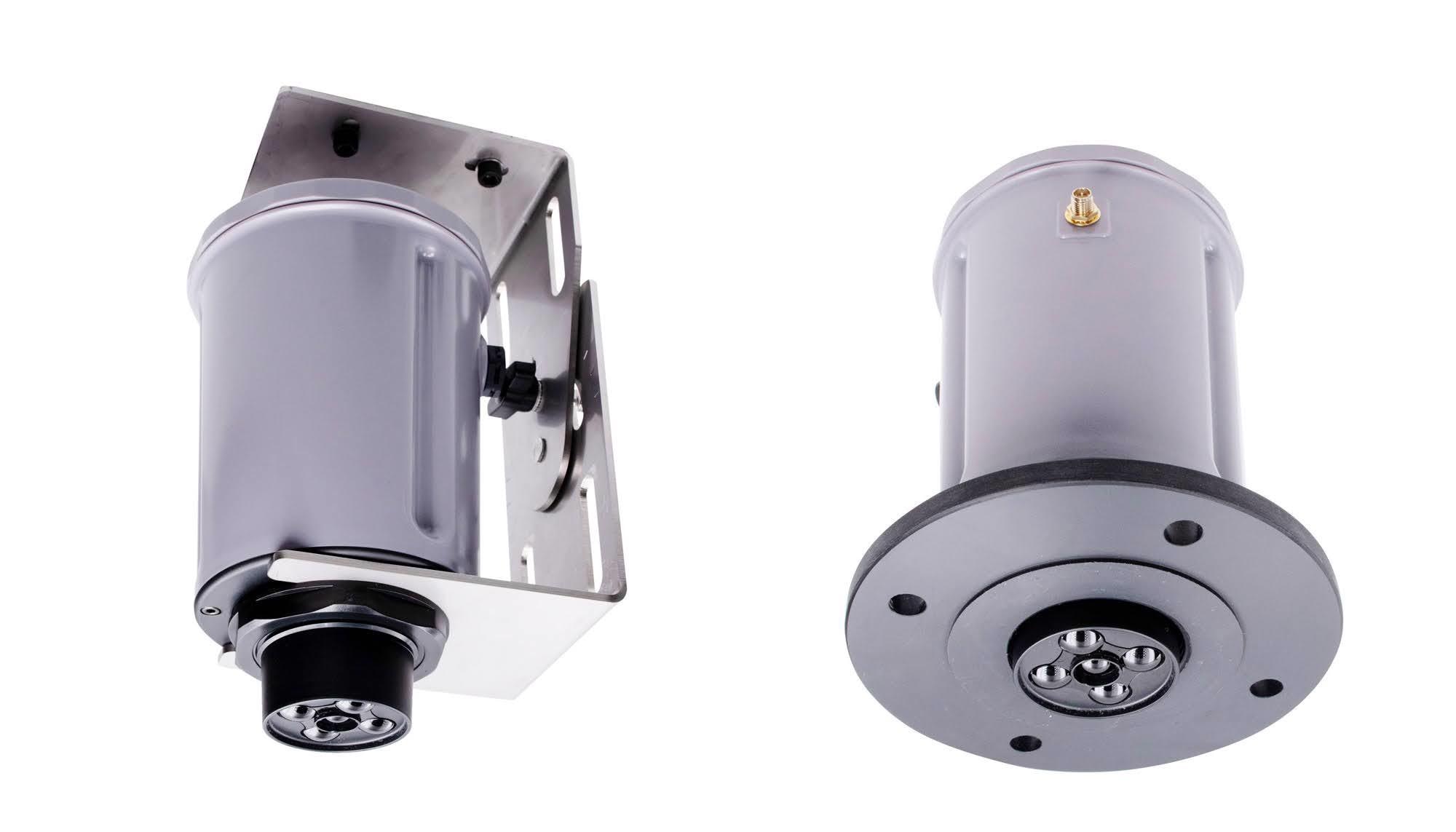
French sensor solutions technology company, Terabee, has launched a new LED Time-of-Fight device for solution providers and systems integrators, for level monitoring solutions in tall silos, vats and tanks.
Terabee’s latest addition to its level monitoring range is the Terabee LoRa Level Monitoring XL, a low-energy, battery-powered sensor – developed for monitoring fill levels of remaining material inside even the largest silos (up to 60 m detection range). It is designed to optimize stock replenishment, cut operational costs and reduce dangerous silo audits at great heights.
Internet of Things device for more efficient and cheaper stock monitoring
Until recent years, monitoring stock and materials levels has been dominated by both contact-based and non-contact transmitters. The Internet of Things has seen an increase in contactless level sensors, capable of providing years of autonomy through their battery powered design, while achieving cost-effectiveness. Moreover kilometers of data transmission coverage is gained through LoRaWAN technology.
Wireless, low-energy, self-powered device
“We’re excited to announce the latest addition to our level monitoring product portfolio, the Terabee LoRa Level Monitoring XL. This new product is a wireless, self-powered IoT device that is conveniently installed on top of silos and tanks, providing over-the-air data about real-time fill levels of stocked materials, whether they are liquids, solids or powders,” said Max Ruffo, CEO and Founder, Terabee.
“Wireless communication and battery-power are features that have been requested frequently by our customers in the past year. We’re glad to be responding to customer and market demand by launching this product. This will now allow our clients to reduce cost, time and complexity during device installation on top of silos. It will also enable easier deployment in remote locations.
“Terabee plans to work with IoT solution providers and integrators, who are looking for third party, ready-to-install devices that will feed existing applications with useful data about material stock in silos and tanks,” said Ruffo.
Key features of Terabee LoRa Level Monitoring XL
- Contactless measurements using optical Time-of-Flight technology
- Low-power, over the air data transmission (LoRaWAN)
- Battery-powered. Years of autonomy
- Supports small to large silos (0.5 to 60 m range)
- Fast, cable free installation
- Free software for easy configuration
- IP65 enclosure for use outdoors

New technology suitable for a wide range of sectors
“We’ve also received interest from a wider range of sectors and organizations than expected — people who are looking for effective ways to digitize material levels in places and in assets not previously digitized. This includes telecommunications companies providing LoRaWAN network infrastructure, silo and farming equipment manufacturers, material transportation and storage companies, to name some,” said Ruffo.
Impact across operations, budget, staffing deployment and planning

Time and cost savings
Installing Terabee IoT sensors on top of silos, eliminates or minimizes time spent by staff to manually inspect remaining content levels in silos and tanks. This results in lower operational costs and enables staff to focus on other critical business functions.
Improved staff safety
With the use of Terabee LoRa Level Monitoring XL sensors regularly measuring and sending (over the air) data about real-time material level in customer silos, there is no need to have people climb and visually audit remaining contents. This often can be a dangerous task and requires specific equipment.
Ensure optimal use of equipment
In some cases, silos are emptied and not re-filled nor used for weeks or months. This mostly happens because silo owners do not know that the silos are empty. Knowing the current fill level of silos will minimize equipment downtime and ensure more efficient use.
Optimize stock replenishment process
With everyday data being gathered from each silo, the overall material restocking process can be better planned and optimized, saving costs and time in the process. This can be done by looking at historic refilling cycles at different periods.
For farmers, this enables leaner material restocking. Material providers, such as animal feed producers or suppliers, will have far more accurate estimations of upcoming production quantities and route optimization for deliveries. As a roll on effect, CO2 emission will be cut too.
Eliminate unreliable approximations
From client discussions Terabee heard a number of old school methods to approximate remaining content quantity in silos or tanks. One that stood out was “banging on the bottom part of the silo and listening for acoustic feedback”. Material in different quantities would produce a different sound and give the user a rough idea on the remaining contents.

Such methods, unfortunately may result in errors in material quantities which may lead to:
(a) running out of stock too fast, which can put farm animals at risk or block production lines
(b) delivering stock too soon and having no space to receive and stock the new delivery before the current stock is consumed. The user either needs to find new, unsecure ways to stock the material or pay extra for a return delivery at a later date.
Modern industry cannot rely on quaint, outdated methods – like banging the bottom of a tank – and remain competitive. Digital stock level monitoring is the new way to get smart and gain efficiency.