Many kinds of garments and wearable products have cushioning materials that provide shock absorption and user safeguards. The journal Polymers considers weft or warp woven spacer textiles that have lately been employed as a substitute for foam materials.
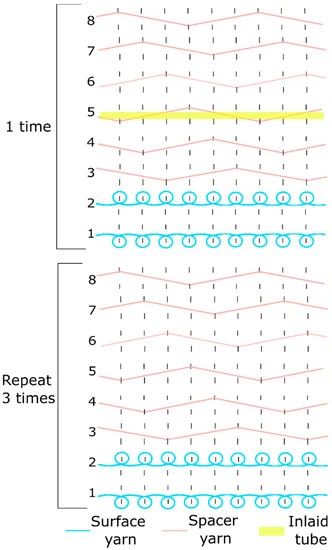
Yarn path diagram of the spacer fabric samples with inlaid tubes. Image Credit: Yu, A., et al., Polymers
Spacer textiles have become a realistic choice due to their distinctive three-dimensional (3D) knitted construction, which allows for greater water and air vapor permeability and breathability in the items. Shoes, couches, car seats, rugs, beds, backpacks, and other everyday objects commonly contain spacer textiles.
Spacer Fabrics
Cushioning fibers such as spacer fabrics can be strengthened by inlaying substances into a connective layer of a material by using a knitting procedure that improves the fabric's structure. Compression behavior is a crucial factor for assessing if a material can provide enough cushioning and ‘hand feel’ for a variety of applications.
The compression characteristics of polymeric foam may be modified by changing the composition and density to meet diverse applications. Spacer fabric is made up of two layers merged by spacer yarns' connective layer.
Any difference in a spacer fabric's material properties and wearing comfort can have an impact. The thickness and compressive stiffness of the spacer fabric may be controlled by the width, composition, thickness, connecting distance, the pattern of the spacer yarns, and inclination angle.
Monofilament and multifilament yarns are often used as spacer yarns, and they can provide the fabric with completely distinct characteristics.
Many studies have been conducted on the compression characteristics of spacer textiles. One of the things contributing to the compression qualities is the elasticity and flexibility of the yarns utilized in the top layer. The amount of tuck stitches inside the surface layers has been discovered to impact the compression characteristics of weft-knitted spacer fabrics.
The compressive characteristics of spacer fabric, on the other hand, have been linked to the connecting layer.
Composite Materials with Silicon-Based Components
Producing a thin fabric with high compression strength and excellent energy absorption might be difficult when employing a traditional spacer fabric structure. In order to improve the cushioning qualities of spacer fabric, a composite construction containing additional silicone-based components was studied.
Previously, a revolutionary sandwich construction with silicone tubes implanted in the connecting layer of spacer fabric was produced. Silicone is a silicon-oxygen primary strand synthetic polymer. Silicone is pliable, fire-resistant, and chemically inert.
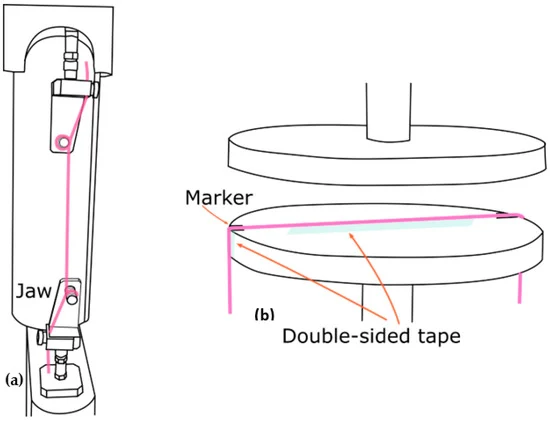
The setting of (a) tensile test and (b) compression test of the tubular samples. Image Credit: Yu, A., et al., Polymers
Silicone inlay tubes provide additional support towards the spacer structure, allowing the fabric to endure pre-stress from the skin without sacrificing its elasticity or energy absorption qualities. Samples manufactured using three kinds of silicone-based tube materials were constructed and measured to examine further the influence of inlaid materials on the qualities of spacer fabric.
The displacement–force curves obtained from the compression test are shown by force at 100 percent and 200 percent elongation of the tubes.
Silicone foam is indeed a porous viscous elastic polymer made of silicone rubbers that are foamed. Silicone foam combines the qualities of silicone with those of foam, resulting in a lightweight product with high elasticity. The mechanical characteristics of tube samples were assessed, as were the compression characteristics of fabric samples and the connection between both.
The implanted tubular materials significantly influence the compression behavior of the spacer fabric. The inclusion of inlaid tubes within the connective layer does not affect the compression behavior of the spacer fabric, albeit at 10% starting compressive strain.
To reach the plateau stage, inlaid spacer textiles require more force than standard spacer fabrics.
The compression stress-strain curve of the material shows no noticeable plateau stage when an inlay substance with stronger tension and compression strength is utilized. The implanted spacer textiles offer a higher compression strength and can collect greater compression energy than standard spacer fabrics.
The spacer fabric is efficiently reinforced by the inlay of ductile material like silicone foam and silicone rods.
The compressive energy and toughness of the resulting textiles can be affected by various inlay materials with varied Young's elastic modulus and tensile behaviors. Because silicone foam also has lesser tensile and compression strength than silicone hollow tubes and silicone rods, the spacer fabric implanted with them may absorb more compression energy.
The material samples with the ultimate compressive rigidity are the spacer fabrics implanted with silicone rods, having high strain and compression strength.
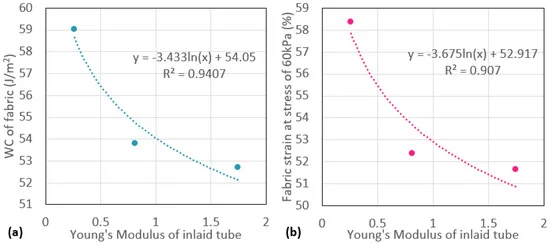
Relationship between Young’s modulus of the inlaid tube, (a) the compression energy of the fabric samples, and (b) the fabric strain at a stress of 60 kPa. Image Credit: Yu, A., et al., Polymers
The results of this study may help in the creation of sandwich-shaped synthetic fibers and the improvement of wearable cushioning items. Inlaid substances can be used as a new parameter in altering the compression and cushioning qualities of knitted spacer textiles, allowing the fabric to deliver the necessary energy absorption for a variety of applications.
Reference:
Yu, A., et al. (2021). Effect of Silicone Inlaid Materials on Reinforcing Compressive Strength of Weft-Knitted Spacer Fabric for Cushioning Applications. Advanced Textile Based Polymer Composites: Synthesis, Characterization and Applications. 22 October 2021. https://www.mdpi.com/2073-4360/13/21/3645
Disclaimer: The views expressed here are those of the author expressed in their private capacity and do not necessarily represent the views of AZoM.com Limited T/A AZoNetwork the owner and operator of this website. This disclaimer forms part of the Terms and conditions of use of this website.