Additively manufacturing materials inevitably impacts both their performance and properties. Now, a research paper published online in the journal Additive Manufacturing considers how the properties of stainless steel are affected by laser additive printing methods.
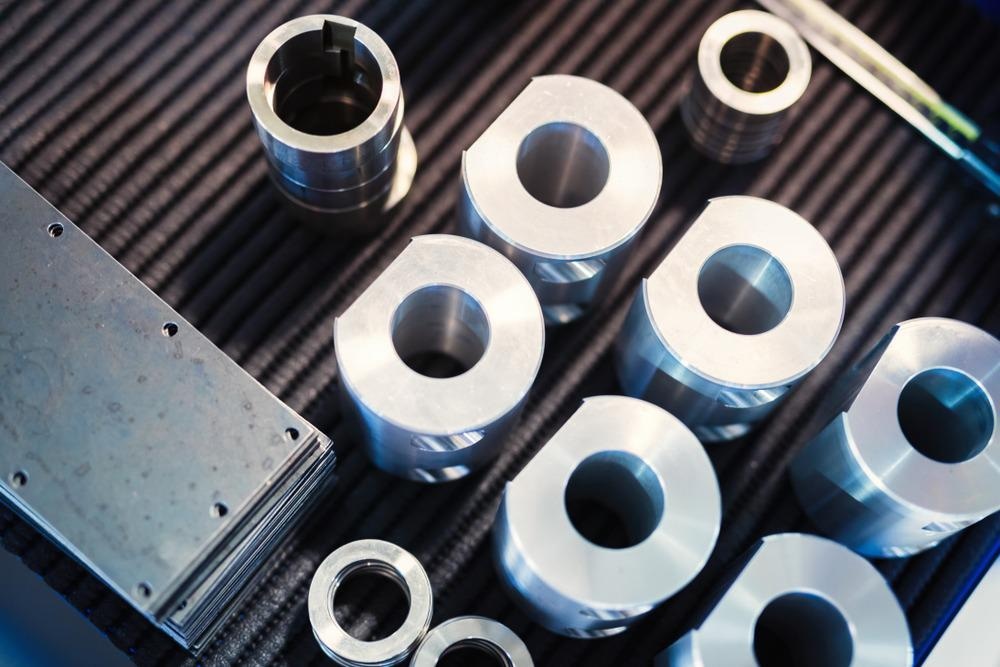
Study: Dislocation microstructure and its influence on corrosion behavior in laser additively manufactured 316L stainless steel. Image Credit: NDAB Creativity/Shutterstock.com
How Additive Manufacturing Affects the Microstructure of Stainless Steel
Additive manufacturing is widely employed in materials fabrication, but it causes changes in microstructural features that can affect the material’s chemical composition and the quality and durability of the finished product.
Laser-based additive manufacturing processes have a layer-by-layer action that causes the formation of highly heterogeneous microstructures. Another aspect of the process that causes this is rapid solidification due to large thermal gradients. Rapid solidification leads to high-density dislocations in steel that are vital for the aerospace, maritime, and vehicle industries.
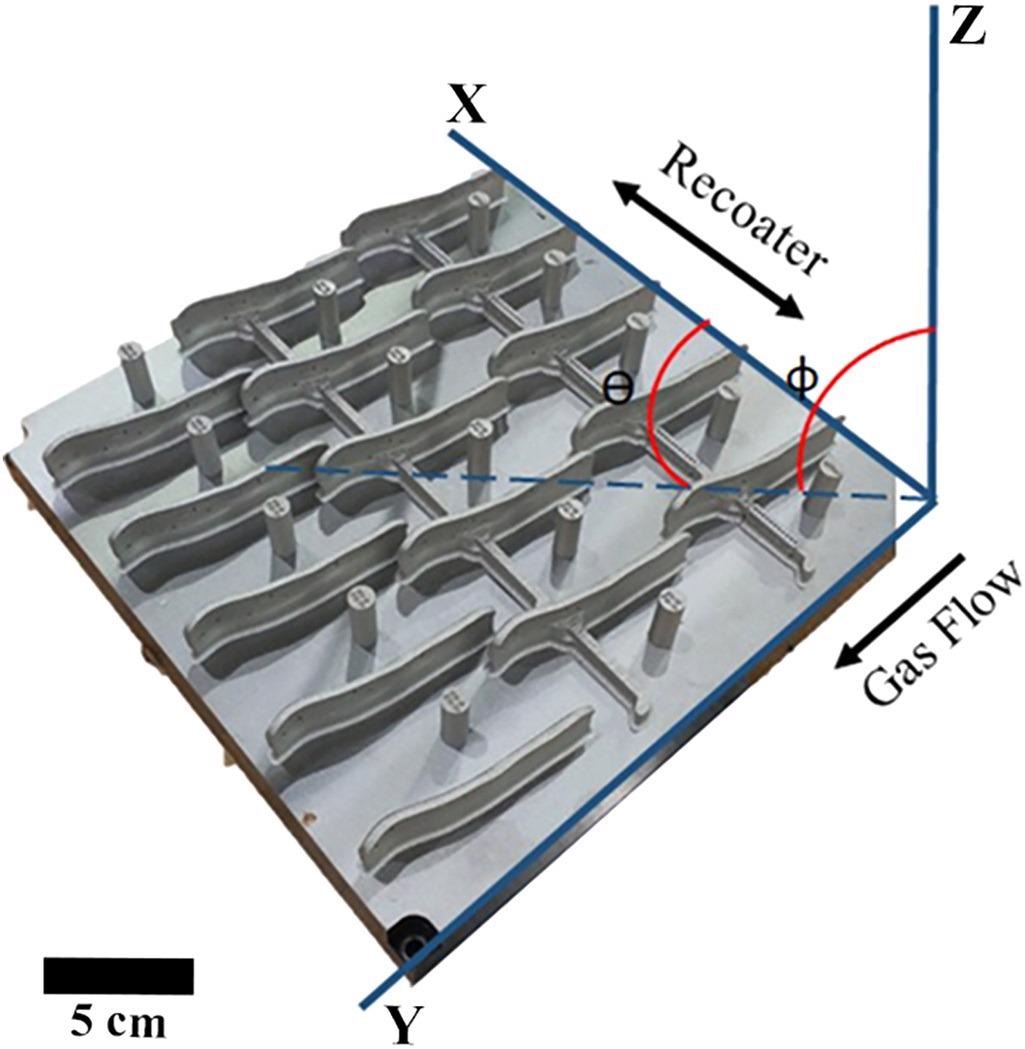
Print orientation demonstrating the recoater direction relative to the gas flow; samples for this study were extracted from the columns, which had systematic variations in the printing speed. Image Credit: Sprouster, D et al. Additive Manufacturing
Common features in industrial-grade steels manufactured with processes such as laser powder-bed fusion are macroscale fusion boundaries and solidification structures, and nanoscale sub-grain cellular structures. The cellular dislocation networks produced have implications for the overall quality and mechanical properties of finished steels. Some specific microstructural features of interest include multiscale interfaces, irregular surface chemistry, and bulk chemical heterogeneities.
Microstructural features are intrinsically intertwined and lead to physical effects such as decreased corrosion resistance, which has implications for structural integrity and longevity of the additively manufactured steels. Defects can lead to the creation of surface electrochemical cells which cause localized corrosion (such as crevice corrosion and pitting) as well as general surface corrosion. The processes that lead to deleterious effects are complex and require intensive research to overcome.
The realization of these features and their effects has spurred much research into additively manufactured steels. Recent studies in the field have included research into titanium alloys, aluminum alloys, stainless steels, and tool steels.
The Research
Understanding microstructural defects and their effects on the chemical structure is necessary to elucidate the potential effects of additive manufacturing on the final product. The team behind the research used several multimodal analytical techniques to achieve the conclusions in the study.
316L powder was used to additively print the sample stainless steel. The system used was a Renishaw AM 250. The primary variable was scan speed, at 550, 650, and 700 mm/s, respectively. The samples produced were 25mm cylindrical rods. Five-millimeter sections were removed for analysis and corrosion measurements.
Laser printed additive manufactured stainless-steel specimens were analyzed with synchrotron x-ray diffraction, imaging techniques, spectroscopic techniques, and TEM. The specimens were L-PBF 316L stainless steels which were printed at different raster speeds. Chemical, atomic, and microstructural information on the fabricated steel was elucidated via analytical techniques.
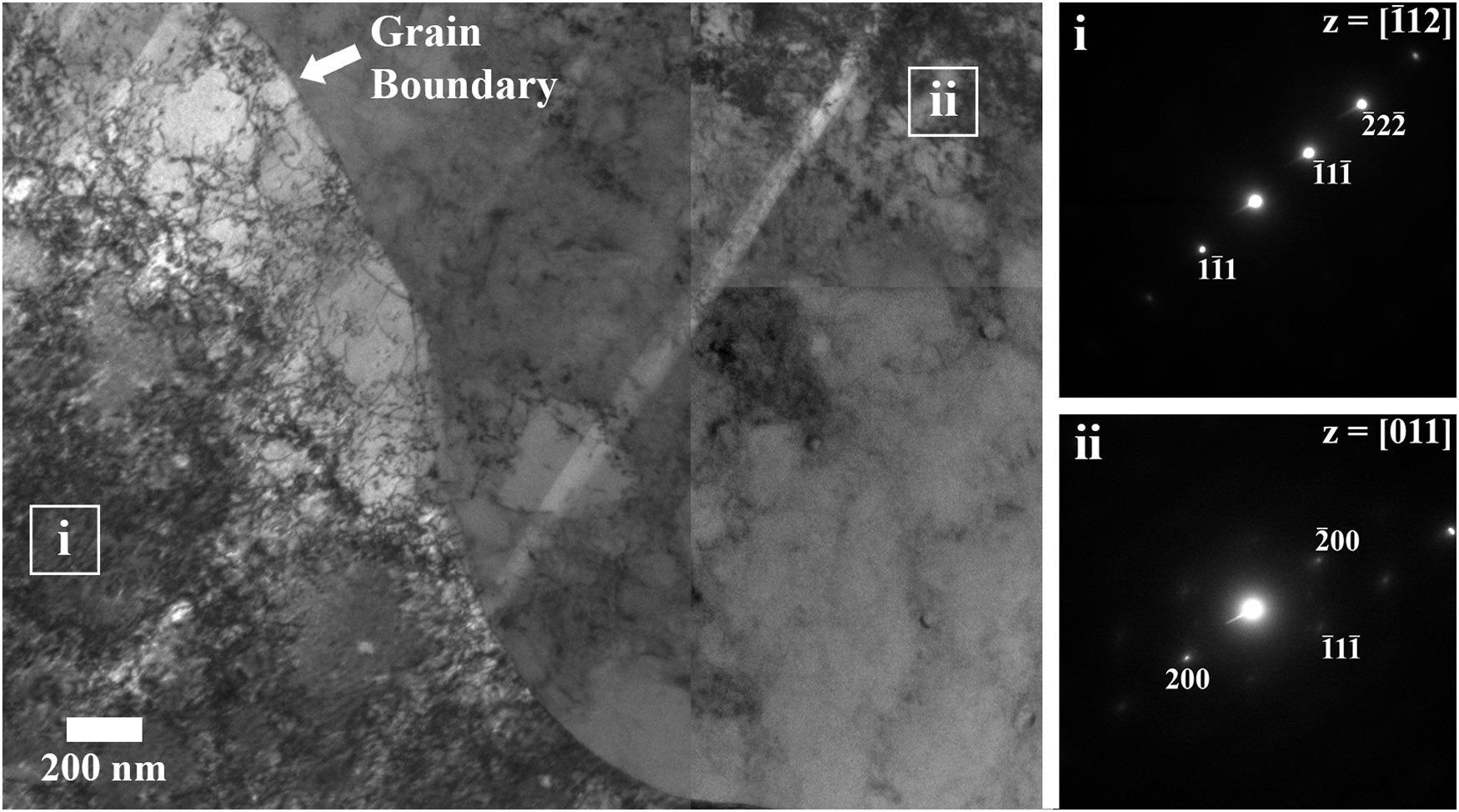
Stitched bright-field TEM micrographs of a selected region containing two adjacent grains near a melt pool boundary on the L-PBF 316L sample printed at 700 mm/s showing the underlying cellular dislocation network. Corresponding selected area diffraction patterns are shown in i and ii. Image Credit: Sprouster, D et al. Additive Manufacturing
Experimental analysis was also carried out to provide information on both localized and uniform corrosion behavior across both single samples and to elucidate variations in corrosion effects across multiple samples at different printing speeds.
Due to the team’s characterization studies, data that quantified the chemical distribution and underlying defects in the microstructure gave insights into the material’s corrosion behavior. Results of the study evidenced that both localized and uniform corrosion behavior was impacted by microstructure and chemical heterogeneities specific to the samples showed dependence on printing speeds.
How Dislocation Microstructure Effects Corrosion Behavior
One of the main results of the study was the implications of defects in microstructure on corrosion behavior of the finished steel product. Corrosion resistance in 316L steel grades is due to the Cr promoting the formation of a bipolar passive film. This film is comprised of an inner Cr2O3 barrier layer and an outer layer that is enriched with metal oxyanions. This forms an electrokinetic barrier that prevents anions from entering.
Microstructural features that are produced during additive manufacturing can prevent the ability of a solute to contribute to passive film layer formation. Some studies on duplex stainless steel using synchrotron methods and electrochemical polarization experiments indicated that there is a correlation between alloy surface structure and nanoscale compositional heterogeneities. These heterogeneities influence passivity behavior such as a breakdown in passivity.
Studies have also indicated that there is a strong correlation between pitting formation and surface defects at the nanoscale. Knowing the nature of defect formation at the nanoscale will help to inform manufacturing strategies that strengthen additive printed stainless steel (and other materials) against the risk of corrosion.
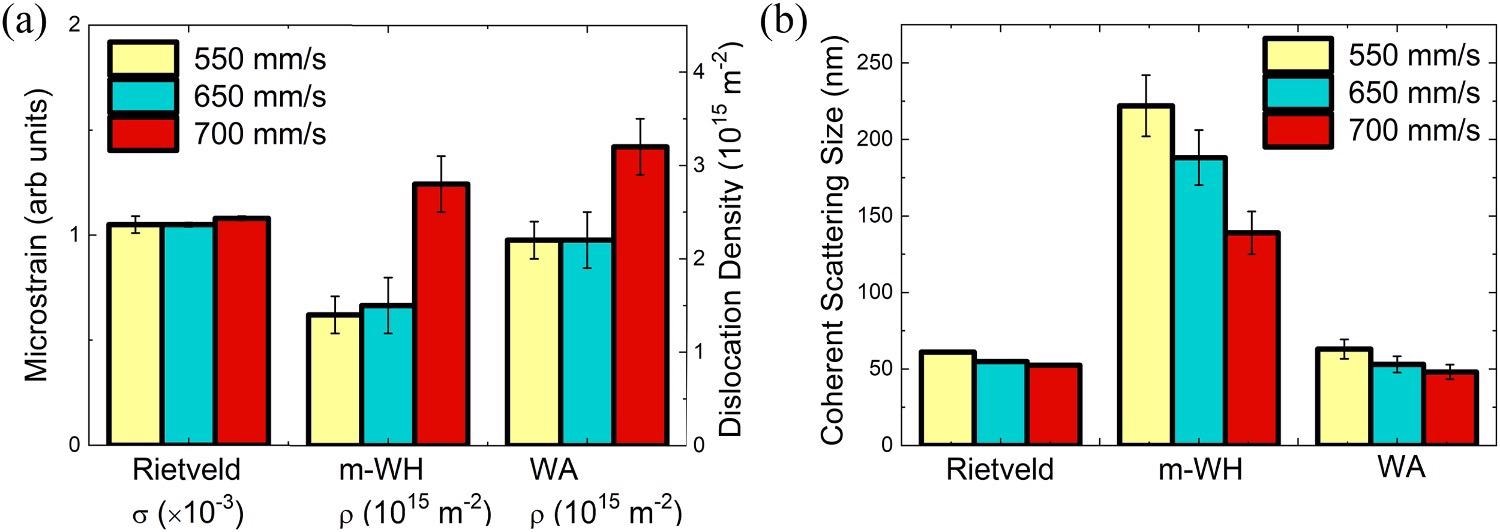
Quantitative structural characterization results as a function of printing speed from the Rietveld, modified Williamson-Hall (m-WH), and Warren-Averbach (WA) analyses including (a) microstrain, σ, and dislocation density, ρ, and (b) coherent scattering size. Image Credit: Sprouster, D et al. Additive Manufacturing
In Conclusion
Defining and categorizing the microstructural and atomic defects that lead to loss of passivity and increased risk of corrosion in additively manufactured materials such as stainless steel is important to the field of materials sciences. Better understanding of how the manufacturing process affects the overall quality and durability of these materials will lead to better grades of industrially important metals in the future.
Further Reading
Sprouster, D et al. (2021) Dislocation microstructure and its influence on corrosion behavior in laser additively manufactured 316L stainless steel [online] Additive Manufacturing 47 102263| Sciencedirect.com. Available at: https://www.sciencedirect.com/science/article/pii/S2214860421004231
Disclaimer: The views expressed here are those of the author expressed in their private capacity and do not necessarily represent the views of AZoM.com Limited T/A AZoNetwork the owner and operator of this website. This disclaimer forms part of the Terms and conditions of use of this website.