Recent attention has focused on how human astronauts will set foot on our closest neighbor, Mars. One main concern is the type and amount of fuel that will be needed to transport people and goods to the Martian surface and get astronauts back to Earth safely. A study published in the journal Nature Communications has presented a novel process to manufacture rocket propellant using biotechnology, providing an innovative approach to one of the major roadblocks to Martian exploration.
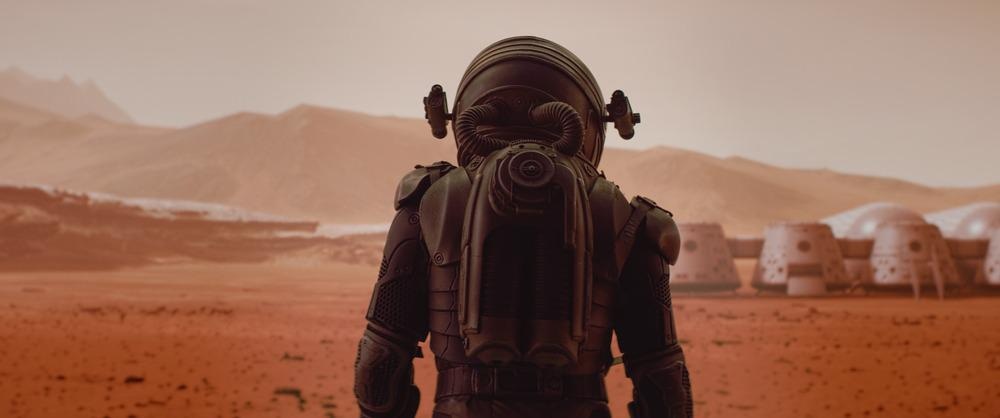
Study: Designing the bioproduction of Martian rocket propellant via a biotechnology-enabled in situ resource utilization strategy. Image Credit: Supamotion/Shutterstock.com
Setting Foot on Mars: Our Next Step in Space Exploration
The success of several projects on Mars such as NASA’s Perseverance has proven that the age of Martian exploration is drawing near. In the not-too-distant future, humankind will set foot on Martian soil, heralding a new era in the exploration of our solar system.
However, there exist several huge challenges to the endeavors of international space agencies and private companies. First and foremost is designing the technology that will get humans and equipment to Mars and, above all, return astronauts safely home so that it is not a one-way trip. Several technologies are already in development, including heavy-lifting-capable rockets and the Orion spacecraft.
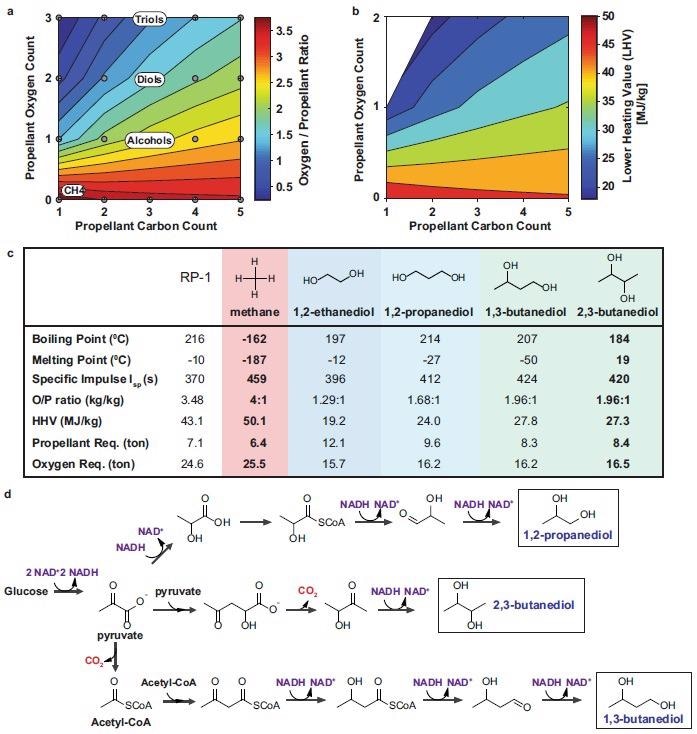
Martian rocket propellant design. a Relationship between increasing the number of oxygen and carbon atoms in the propellants to the mass of oxygen needed for complete combustion, i.e. oxygen/propellant ratio (O/P ratio). Increasing the number of oxygen atoms in the propellant reduces the mass of external oxygen needed for full combustion. b Relationship between increasing the number of oxygen and carbon atoms in the propellant to its lower heating value (LHV). Increasing the number of oxygen atoms in the propellant reduces its LHV. c Propellant relevant properties for Rocket Propellant-1 (RP-1), used for spacecraft launch from Earth, methane, and proposed Martian rocket propellants: 1,2-ethanediol, 1,3-propanediol, 1,3-butanediol, and 2,3-butanediol. Theoretical specific impulses (Isp) were calculated using Eq. (3). Mass of propellant required was calculated using the ideal rocket equation (Eq. (4)). d Short-chain diol metabolic pathways from glucose. Both 1,2-propanediol and 1,3-butanediol require excess NADH. Carbon dioxide evolved: red. NADH consumed: purple. Name of short-chain diols: blue. Source data underlying Fig. 2c are provided as a Source Data file. Image Credit: Kruyer, N.S et al., Nature Communications
Transporting the payload of fuel necessary for the safe return of humans from Mars is a huge logistical task and would prove difficult, requiring huge rockets or infrastructure in space for storage that would be prohibitively expensive. It is estimated that the approximately 30 tons of liquid oxygen and methane required just for the launch of a manned aerial vehicle (MAV) into low-Mars orbit would cost $8 billion dollars and require a 500-ton initial payload for one mission alone.
Now, a team of scientists have presented a method to manufacture vital propellant for the journey home in situ on Mars itself using biotechnology. This research aims to provide several key advantages over other proposed methods for Martian rocket propellant production. It is hoped that large-scale production of biological propellant production will become a key technology for future Martian exploration missions.
Developing New Methods of Propellant Production
Developing an in-situ rocket propellant production method on the surface of Mars has several advantages: aside from vastly reducing the initial payload requirements of Mars missions it would reduce the mass of the Mars lander and solve the safety issues of transporting copious amounts of rocket propellant.
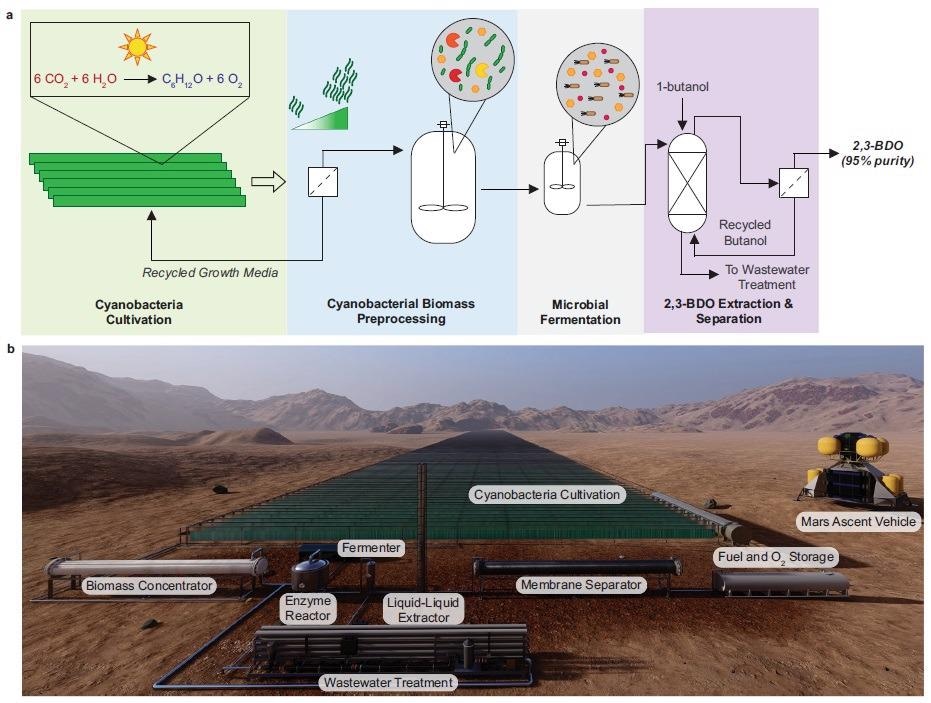
Continuous bio-ISRU production of 2,3-BDO on Mars. a The bio-ISRU production of 2,3-BDO is composed of four modules: (1) Cyanobacterial cultivation in photobioreactors or biofilm growth (shaded green), (2) Cyanobacteria biomass preprocessing composed of biomass concentration via membrane filtration and enzymatic digestion in a stirred tank (shaded blue), (3) Microbial fermentation of the cyanobacterial glucose to produce 2,3-BDO (shaded gray), (4) 2,3-BDO extraction and separation via sequential liquid–liquid extraction and membrane separation to achieve 95% purity (shaded purple). Chemical formula: Red Martian resources. Blue chemicals made on Mars. b Rendering of what the bio-ISRU for 2,3-BDO process might look like on Mars, with a Mars Ascent Vehicle included for scale. The cyanobacterial cultivation module makes up the majority of the material and land footprints. Image Credit: Kruyer, N.S et al., Nature Communications
Methane is an alternative to traditional rocket fuel due to its specific impulse and favorable heating value. Specific impulse is a measure of rocket performance per unit of propellant mass. Strategies proposed to manufacture methane in-situ include transporting methane from Earth and producing O2 on Mars via solid oxygen CO2 electrolysis, or transporting hydrogen from Earth, which would require even bigger payload systems than are currently in use.
Using Biotechnology to Manufacture a Mars Specific Rocket Propellant Manufacturing Technique
By developing a biotechnology-enabled Mars-based method, the specific conditions on the planet can be leveraged. These include low specific gravity, elevated CO2 levels, sunlight, and abundant water. Biological systems convert inorganic atmospheric CO2 into usable oxygen and organic compounds. The Martian atmosphere contains 95% CO2, making it 20 times as abundant as on Earth.
The research, published in 2021, proposed a microbially enabled strategy to produce 2,3-BDO (2,3-butanediol) from sunlight, carbon dioxide, and water found on Mars. The continuous process involves two common bacteria in biotechnology: cyanobacteria and a genetically engineered strain of E. Coli. The cyanobacteria digest Martian CO2 to create nutrients which are then converted into fuel by the E. Coli. Key constraints of the process are the levels of Martian sunlight and water.
Some Key Advantages of the Technology
Refinement of the process is envisaged to have some key advantages over an O2 only strategy. Using existing technologies, this method will require a threefold higher payload but produces excess oxygen, which can be utilized for other missions or for habitation areas of a Mars mission.
Key optimization strategies in both biological processes and materials have been identified. Lighter process materials and improved biological processes are projected to result in a reduced payload and power needs than an oxygen-only strategy. Missions using this method will require 50% less mass for initial payloads.
Full process metrics for the bio-ISRU production of 2,3-BDO. a Water use, b power requirement, and c payload mass accounting for all unit operations in the bio-ISRU for 2,3-BDO production using either biofilm or suspended cyanobacteria growth modes. Results are based on 10 tons of 2,3-BDO produced over 500 sols. Chemical ISRU (DRA 5.0 O2 only strategy) shown in gray. Source data are provided as a Source Data file. Image Credit: Kruyer, N.S et al., Nature Communications
The Future
Landing humans on Mars and returning them home will require innovative approaches like the one laid out in this research paper. Whilst major challenges in biology and materials exist, this microbially enabled in-situ propellant manufacture process may provide the key to truly sustainable Mars exploration and future colonization efforts.
Further Reading
Kruyer, N.S et al. (2021) Designing the bioproduction of Martian rocket propellant via a biotechnology-enabled in situ resource utilization strategy [online] Nature Communications 12 article no. 6166 | nature.com. Available at: https://www.nature.com/articles/s41467-021-26393-7
Disclaimer: The views expressed here are those of the author expressed in their private capacity and do not necessarily represent the views of AZoM.com Limited T/A AZoNetwork the owner and operator of this website. This disclaimer forms part of the Terms and conditions of use of this website.