Nanostructured materials have the potential for several next-generation applications for research and industry. A new study in the journal Accounts of Material Research has considered how to fabricate nanostructured materials with vastly improved properties.
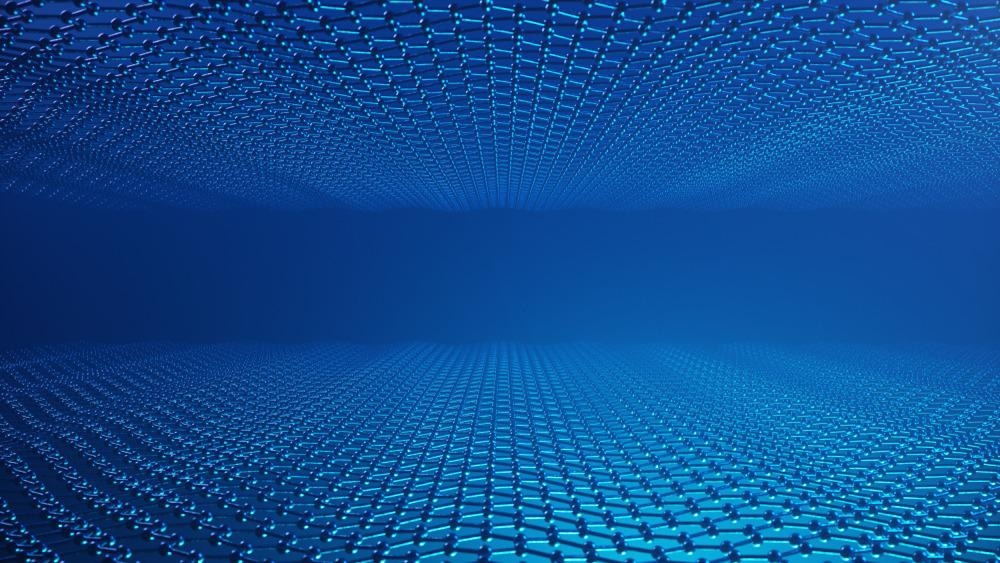
Study: How Can We Efficiently Fabricate Nanostructured Materials with Unprecedented Properties? Image Credit: Rost9/Shutterstock.com
Nanostructured materials have been the focus of research in recent years due to their properties and promising applications for a wide range of industrial, research, and commercial applications. These nanoscale materials include several types, including porous materials, laminates, polycrystals, and single-crystalline wires. Their range of applications is potentially vast, including high-strength structures, drug delivery systems, heterogeneous catalysts, and sensors.
Graphic illustration of self-organization during dealloying of an AgAu alloy into an aqueous electrolyte. a) Selective dissolution of Ag drives the formation of Au-rich islands on the surface. b) These island perturbations trigger an instability that corrugates the surface with a characteristic wavelength. c) This instability grows in amplitude, exposing subsurface Ag, and dealloying proceeds into the material, eventually forming a bicontinuous Au-rich network. Image Credit: McCue, I & Snyder, J., Accounts of Material Research
The interest in these structures is due to their novel and enhanced properties. These properties are conferred by the nanostructured materials' large surface area, complex surface chemistry, and high concentrations of surface defects. Nanoscale heterogeneous catalysts, for example, have surface strains, unique surface electronic states, and increased numbers of dangling bonds that contribute to their elevated activity levels.
Challenges in Fabricating Nanostructured Materials
However, fabricating nanostructured materials is often resource-intensive and issues exist with scalability to commercially viable levels of production. There also exist challenges to turning observations into practical applications. Fabricating nanoscale materials with unprecedented properties requires innovative approaches that are both low-cost and low-resource intensive. Cracking these challenges will realize a new frontier in the fields of nanotechnology and materials science.
Creating Low-Cost, Low-Energy Fabrication Methods
In the paper, McCue & Snyder explored techniques to tackle this challenge and fabricate nanostructured materials which significantly improved qualities. One method that they were particularly interested in was self-organization via dealloying. Self-organization is the process that creates well-defined three-dimensional structures through the spontaneous assembly.
Dealloying has been described as far back as Leonardo Da Vinci, but only in recent years has this process been applied to the engineering of nanoscale features in a material. By creating self-organizing nanoscale structures via a dealloying process, a spontaneous, low-cost, and low-energy method of nanomaterials can be achieved. The initial alloying process still needs an energy input, but beyond that, the energy required is minimized.
Dealloying works by perturbing and roughening the surface of a material, which causes nanoscale surface irregularities (much like corrosion.) A percolating, 3D structure is achieved which has characteristic diameter and morphology if the surface mobility of the remaining elements is high enough. Numerous thermodynamic and kinetic factors can be harnessed to direct nanoscale pattern formation.
The paper considered the current literature on this process to explore any gaps in knowledge that will drive the creation of nanoscale materials with enhanced properties via this process.
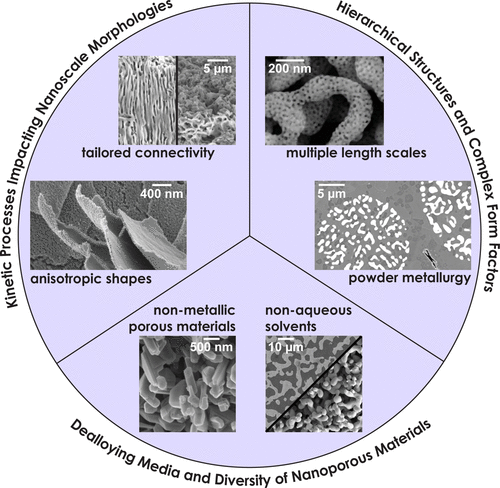
Three key research areas to realize true nanoscale control via self-organization processes: (bottom) extension of these tools to any material class; Image Credit: McCue, I & Snyder, J., Accounts of Material Research
Key Research Areas and Challenges
There are three key research areas that inform the creation of self-organizing nanostructured materials. These are extension of tools to multiple classes of materials, control of nanoscale morphology by manipulating thermodynamic and kinetic factors during the process and post-processing controls, and sequential self-organization to develop multiscale nanocomposites.
The application of selective alloying to all classes of materials will make it a truly universal process. Traditionally, dealloying is limited to noble nanomaterials so they can survive concentrated acid/base environments such as solvents. A breakthrough was achieved that allowed selective dissolution in any liquid solvent. Selective evaporation, gas-phase reactions, and diffusion couples extended the process to non-liquid solvents.
Recent work has also suggested that by changing the initial alloy’s starting composition, the morphology (from globular to bicontinuous and lamellar morphologies) of the material can be altered and tuned. This allows for a wider palette of resultant morphologies in the nanomaterial.
A key manufacturing challenge is the creation of engineered materials with the same internal structural hierarchy as natural ones such as wood or bone. Manufacturing thin-walled materials which resist buckling is a complex challenge. Nanotruss materials have had some success but have issues with scalability and microstructural control. Hierarchical nanoporous materials are the closest materials thus far manufactured that exhibit similar levels of internal complexity as natural structures.
To overcome this, the team suggested developing a multi-step dealloying process. A proposed structure is a macroscopic material with large nanoscale struts that are nanoporous. The study has suggested that bulk composite strategies can be achieved with nanoscale precision via a multi-step process. For example, liquid metal and electrochemical alloying could be combined to achieve the desired results.
Future Opportunities
There are several opportunities that could soon be realized. This includes new classes of nanostructured materials, tailored surfaces for different applications and materials, and the development of designer nanoscale composite materials. Another opportunity for the dealloying process is that it can be used in conjunction with almost any other fabrication technique, such as powder metallurgy, and sol-gel strategies. Whilst this is a scalable process, its adoption will be helped by integrating it with other widespread manufacturing processes.
Further Reading
McCue, I & Snyder, J. (2021) How Can We Efficiently Fabricate Nanostructured Materials with Unprecedented Properties? [online] Acc. Mater. Res. 2021 | pubs.acs.org. Available at: https://pubs.acs.org/doi/full/10.1021/accountsmr.1c00180
Disclaimer: The views expressed here are those of the author expressed in their private capacity and do not necessarily represent the views of AZoM.com Limited T/A AZoNetwork the owner and operator of this website. This disclaimer forms part of the Terms and conditions of use of this website.