Aerogels have received significant attention in recent years due to their unique properties and potential for applications such as thermal insulation. However, traditional silica aerogels can be brittle, which limits their use. Now, a paper published online in Composites Part B: Engineering has explored improving the design of aerogels based on wood, which have their own challenges, to overcome the issues with traditional aerogels.
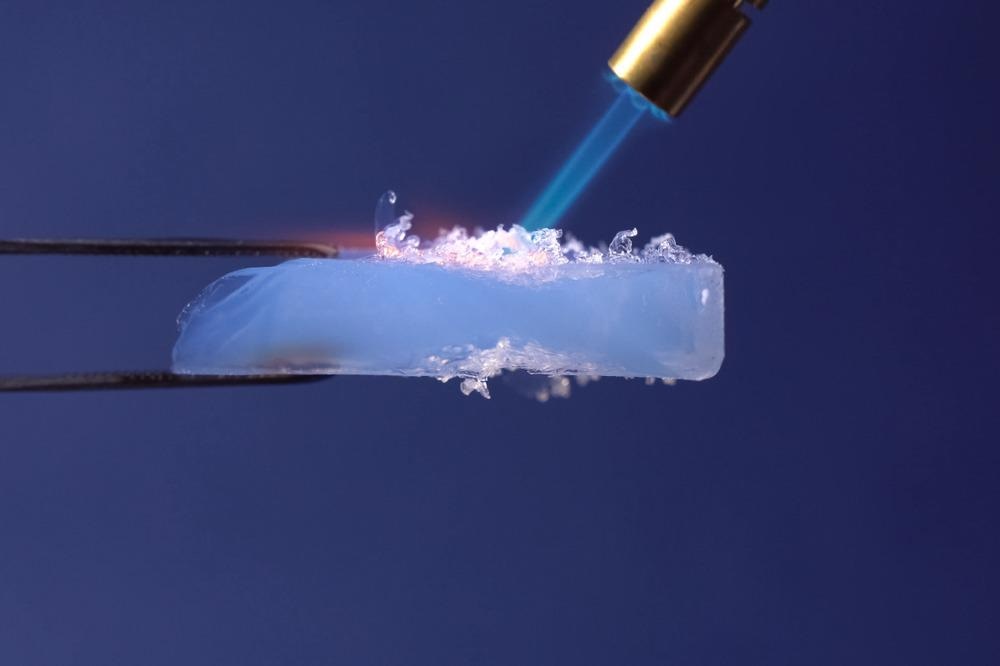
Study: Highly elastic and fatigue resistant wood/silica composite aerogel operated at extremely low temperature. Image Credit: LuYago/Shutterstock.com
What are Aerogels?
Aerogels are a class of synthetic, porous ultralight materials that are derived from a gel that has the liquid component removed and replaced with gas. The process of liquid removal does not cause any significant collapse of the structure of the gel. This process creates a material with low density and thermal conductivity.
Various chemical compounds can be used to make aerogels, the most common being silica. Aerogels are dry, solid, rigid materials but shatter under large amounts of pressure. Despite this, aerogels are structurally strong and display excellent load-bearing capacity.
Their thermal insulation properties are due to the lack of heat conductivity throughout their structure thanks to the replacement of liquid components with gas. However, they are not good radiative insulators.
Aerogels are hydrophilic in nature and when they absorb moisture they can undergo structural changes, but this can be avoided by using chemical treatments to improve their hydrophobicity. Aerogels with hydrophobic interiors do not degrade as much as those with only a hydrophobic outer layer. Nicknames for aerogels include blue smoke, solid air, and solid smoke.
Overcoming the Brittleness Issue
Whilst silica aerogels, the most common form of these substances, display superior thermal insulation properties, their commercial application is limited by their brittleness. Several precursor materials have been proposed and investigated over the years to address this issue and improve the properties of aerogels.
Materials that give aerogels improved elasticity have been studied including cellulose, graphene, polymers, and wood. Among these, wood aerogels have shown significant promise. This is due to the factors such as an abundance of materials, sustainability, cost-effectiveness, and biocompatibility. After delignification, wood aerogels can possess excellent thermal insulation and elevated levels of elasticity, with a strain of 60%.
Further Reading: 3D Super-elastic Graphene-based Aerogels Prepared with Atmospheric Drying
However, despite their advantages, challenges still exist with wood aerogels. They are flammable and possess poor fatigue resistance. This limits their commercial applications. To overcome these issues, composite materials of wood and polymers have been explored.
Wood/polyvinyl alcohol composites have been studied, which improved fatigue resistance, but the material was still flammable. To improve the flame retardancy of the composite materials, organic and inorganic flame retardants have been incorporated into wood aerogels. However, organic reagents can cause environmental or health risks.
Inorganic flame retardants explored include boron nitride and calcium carbonate. Whist these tend to be more environmentally friendly, incorporating them into wood aerogels can cause problems with elasticity and fatigue resistance due to incompatibility issues. Therefore, it is difficult to fabricate a wood-based aerogel with both superior flame-resistant and mechanical properties.
A Different Approach
The paper published in Composites Part B: Engineering has presented a hybrid organic/inorganic approach to fabricate a wood-based aerogel with superior elasticity, fatigue resistance, and flame retardancy properties.
The research used balsa wood as a raw material to prepare the aerogel. Silica was used as the inorganic component, which gave the hybrid wood/silica aerogel superior flame retardant properties with a limiting oxygen index (LOI) of 44%.
The structure of the prepared aerogels was honeycomb-like, which improved the novel hybrid wood/silica aerogel’s fatigue resistance and elasticity. Height retention of 92.8% after 300 cycles of a fatigue test was observed in the material, demonstrating the fatigue resistance of the hybrid organic/inorganic aerogel.
Furthermore, the material has a low coefficient of linear expansion. The advantage of this is that the aerogel is imparted with superior mechanical properties. Compression and recovery actions could be performed, even under extreme conditions such as testing in liquid nitrogen. Consequently, not only could the material perform well under high temperatures, but it also displayed superior performance under extremely low temperatures.
The Future
The novel hybrid aerogel presented in the study is a sustainable, low-cost material that can perform well in extreme environments, making it ideal for applications such as liquid nitrogen and liquefied natural gas pipelines.
The results of the research demonstrated the development of a novel hybrid organic/inorganic wood/silica aerogel with superior mechanical and thermal resistance properties, able to withstand physical and temperature stresses that would otherwise prove challenging for other types of aerogel currently in use.
Further Reading
Yan, M et al. (2021) Highly elastic and fatigue resistant wood/silica composite aerogel operated at extremely low temperature [online] Composites Part B: Engineering 230 109496 | sciencedirect.com. Available at: https://www.sciencedirect.com/science/article/abs/pii/S1359836821008635
Disclaimer: The views expressed here are those of the author expressed in their private capacity and do not necessarily represent the views of AZoM.com Limited T/A AZoNetwork the owner and operator of this website. This disclaimer forms part of the Terms and conditions of use of this website.