Lignin-carbohydrate complexes (LCCs) are biopolymers made up of lignin and carbohydrate monomers that are covalently bonded. LCCs from pulp mills can be a useful biopolymer for polymer film, according to a new breakthrough study published in the journal Frontier Energy Research.
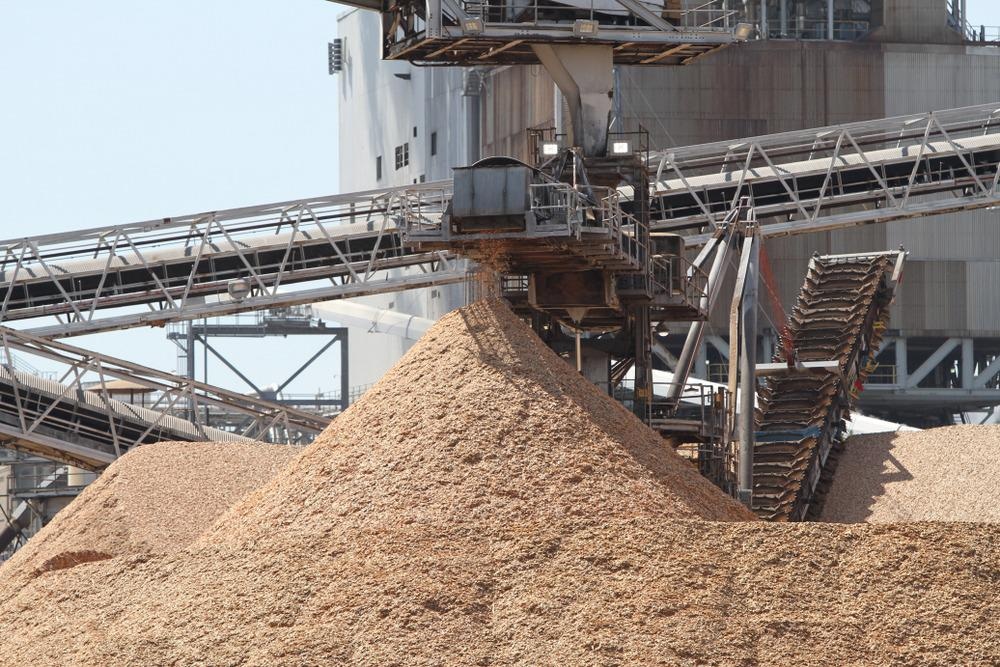
Study: Durable Biopolymer Films From Lignin-Carbohydrate Complex Derived From a Pulp Mill Side Stream. Image Credit: Everett R. Davis/Shutterstock.com
Biopolymers are organic or natural polymers made by living organisms' organelles. Monomeric components are covalently bound to generate bigger molecules in biopolymers. LCCs are generated during the formation of plant tissues and serve to increase the mechanical robustness of plants in an ecosystem.
Lignin is a group of complex organic polymers that make up important structural elements in most plants' support tissues. Lignins play a crucial role in the development of cell walls, especially in wood and epidermis. LCCs have different chemical structures according to the wood source and processing method.
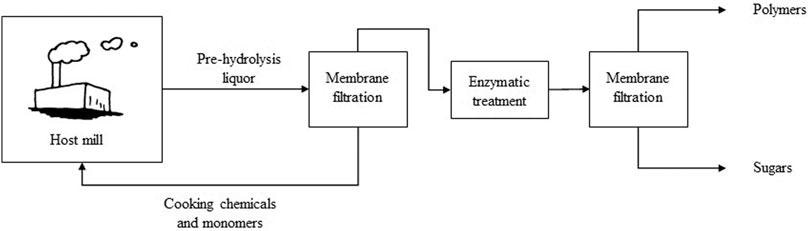
Schematic description of the Ecohelix process for LCC production. Image Credit: Asikanius, B., et al., Frontier Energy Research
The New LCCs Finding
The feedstock comes from a disintegrating pulp mill that uses a sulfite heating method to eliminate LCC and other elements from the cellulose fraction before hydrolysis. Some of the prehydrolysis liquid is recycled into the procedure, but the majority is discarded. Ecohelix technique was used to extract the LCC from this side stream and modify it enzymatically.
The polymer used in this research is water-soluble and anionically charged. The research shows that the LCC has the capability to be used in polymeric film applications. The breaking strain describes a film's capacity to stretch before breaking.
The breaking strain increased as the concentration of LCC 80/20 was raised, however when the concentration was raised further to 30% and higher, the strain decreased. It has the potential to replicate stretchable polymers (the tensile strength of the product is low).
Based on the findings, it can be inferred that the viscoelastic characteristics of composite films may be altered by adjusting the LCC dose. Depending on the polymer content, the ratio of hemicellulose and lignin in LCC appears to alter the strain characteristics of the films.
The cause for the drop in breaking strain at a 30% or greater dose is thought to be the same for both LCC and lignosulfonate, and is related to increased hydrogen bonding. Despite the absence of the hemicellulose component, the lignosulphonate may still form hydrogen bonds. As a result, raising the LCC or lignin content in the films enhanced the frequency of appealing interactions.
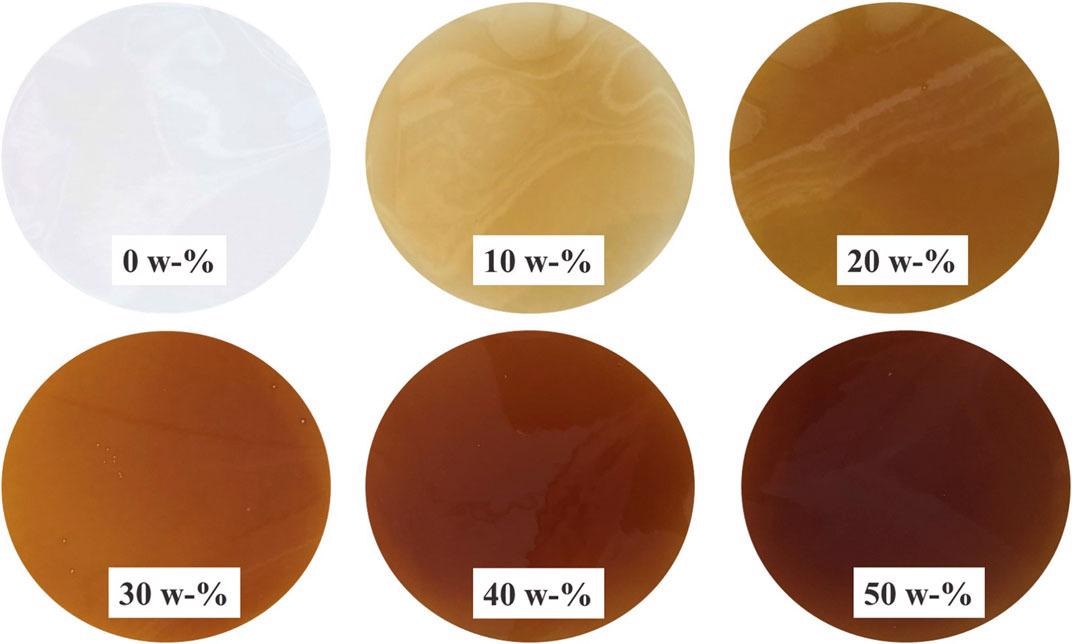
Films with 0–50 w-% LCC 80/20 at 10 w-% interval, 95–45 w-% HEC and 5 w-% glycerol. Image Credit: Asikanius, B., et al., Frontier Energy Research
Applications of the New Findings
The LCC biopolymer has the capability to be employed in packaging applications due to its ability to improve the mechanical characteristics of polymeric films. The oxygen permeabilities of the composite films of HEC-LCC were investigated since renewable barrier films are an intriguing field of research.
Barrier films made from renewable resources are appropriate for a variety of uses and markets. The barrier film is a kind of disposable infection prevention and control solution that helps to prevent germs and fluids from spreading over high-touch surfaces.
Barrier films are impenetrable packaging solutions that are often mainly composed of one or more layers of stretchable film, the material of which varies depending on the purpose. To achieve the required outcomes, barrier films are coated on both sides with various lacquers/resins.
Why the LCCs Barrier Film is Important?
The barrier qualities of the packaging are a significant consideration when choosing food packaging solutions. Permeability of the gases such as oxygen and carbon dioxide, water vapor, fragrance compounds, and light are all examples of barrier qualities. These are critical elements in preserving the quality of packaged meals.
The enhanced Young's modulus of LCC films is thought to be due to the greater energy density of hydrogen bonding, which is aided mostly by the hemicellulose portion in the polymer, according to the research. For specimens with significant levels of sulfonated lignin, the LCCs breaking strain displayed a non-linear relationship with concentration.
The lignosulphonate polymer had the highest breaking strain. The LCC sample had the best mechanical qualities when oxygen permeabilities were measured at 50 and 80 percent relative humidity. At both humidities, oxygen permeability reduced dramatically as LCC content increased.
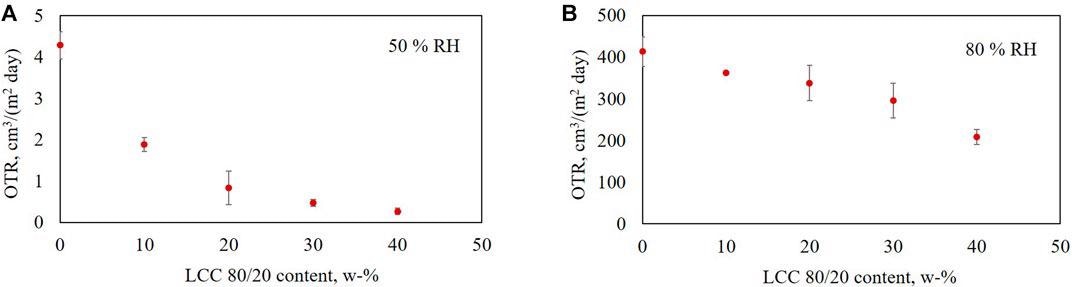
Oxygen transmission rate for films containing 0–40 w-% LCC 80/20, 95–55 w-% HEC and 5 w-% glycerol at 23 °C and (A) 50% and (B) 80% humidity. Image Credit: Asikanius, B., et al., Frontier Energy Research
Future Research
In future research, a more thorough analysis of the combinations of LCCs with some other film-forming polymers and plasticizers is advised in order to determine the best composition for particular purposes. The improved mechanical characteristics of the composite films, as well as their capacity to reduce oxygen permeability, suggest that LCC has possibilities in sectors where biopolymeric films are utilized, such as packaging and paper in barrier films.
As a result, it would be crucial to examine the interactions of LCC with natural fiber in greater depth. The LCC polymers might be employed to improve the end product's characteristics while also allowing for more effective and comprehensive use of biomass.
Reference
Asikanius, B., et al. (2021). Durable Biopolymer Films From Lignin-Carbohydrate Complex Derived From a Pulp Mill Side Stream. Frontier Energy Research. Published Online: 25 November 2021. https://www.frontiersin.org/articles/10.3389/fenrg.2021.782545/full
Disclaimer: The views expressed here are those of the author expressed in their private capacity and do not necessarily represent the views of AZoM.com Limited T/A AZoNetwork the owner and operator of this website. This disclaimer forms part of the Terms and conditions of use of this website.