A new breakthrough in flame retardant composites was made by self-assembling melamine and phytic acid (PA) upon rGO, which was then used to increase the fire resistance of PLA, as written in the journal Polymers.
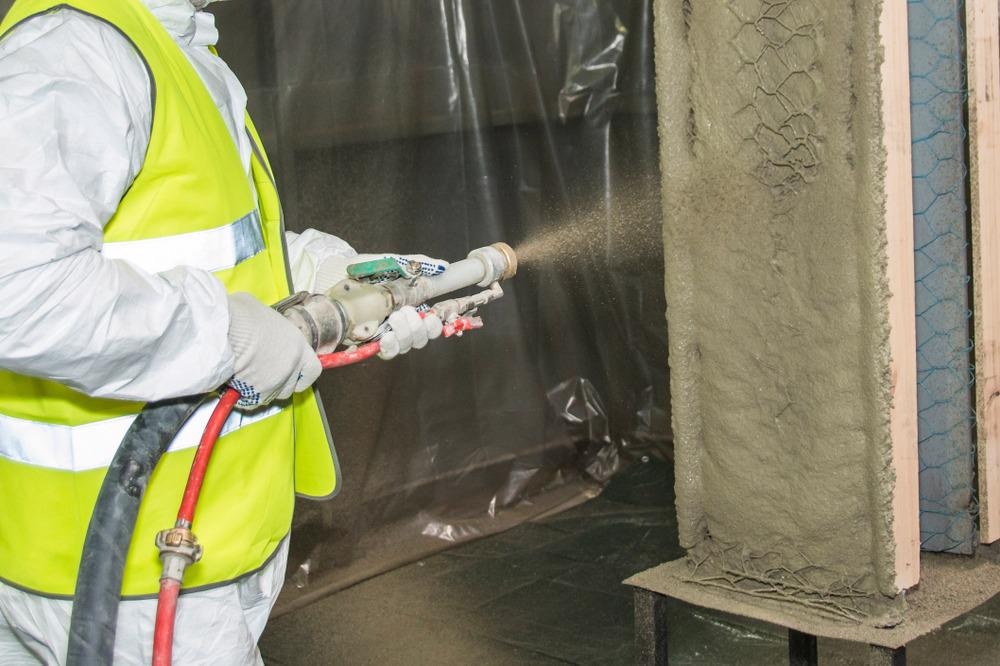
Study: A Novel Self-Assembled Graphene-Based Flame Retardant: Synthesis and Flame Retardant Performance in PLA. Image Credit: Vlad Karavaev/Shutterstock.com
PMrG reduces the composite's maximum burning rate and total heat release during combustion while increasing the LOI ratio and time to ignition, considerably enhancing the composite's flame retardancy.
PLA Broad Range of Applications
Polylactic acid (PLA) has attracted considerable attention due to its wide application in disciplines such as bioengineering, textile products, and electrical devices. It is an outstanding biodegradable material with advanced functionality such as excellent mechanical properties, good processing capability, and biological suitability. PLA, however, has a low flame retardancy.
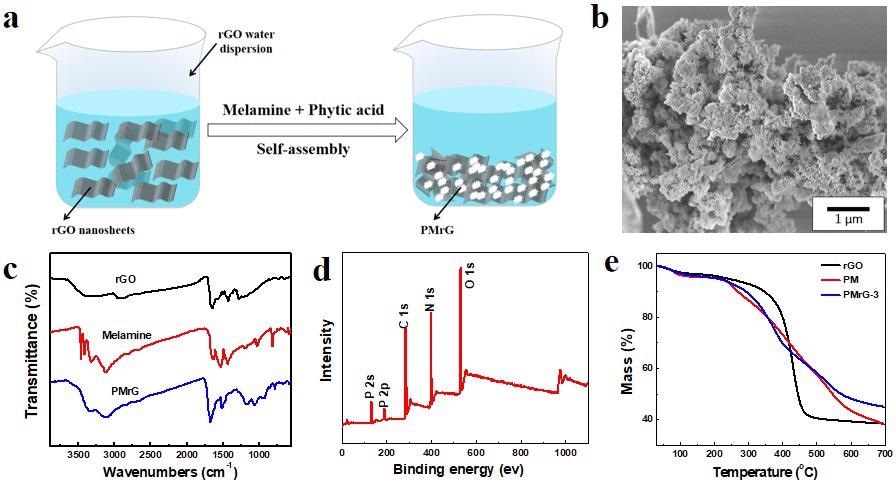
(a) Schematic representation for the preparation of PMrG; (b) SEM images of PMrG; (c) FTIR spectra of rGO, Melamine, and PMrG; (d) XPS spectra for PMrG; and (e) TGA curves of rGO, PM, and PMrG-3. Image Credit: Yang, P., et al., Polymers
PLA's low flame retardancy severely restricts its use, particularly in military applications. PLA goods with increased fire resistance qualities are in high demand in a variety of industries, including electronics, automobiles, and aerospace. To enhance the flame retardancy of PLA, a range of tactics have been explored, including flame-retardant treatment and the inclusion of flame retardants. Other than PLA, there exists phytic acid (PA).
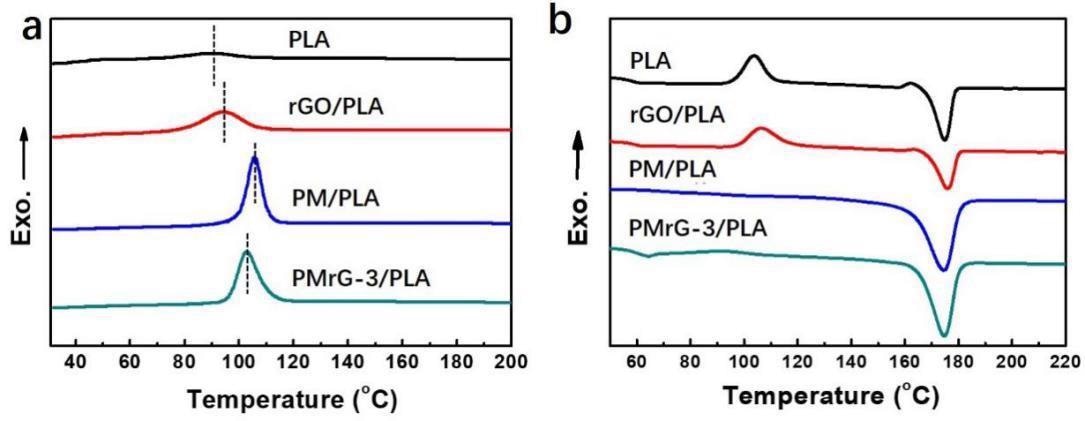
DSC curves of PLA, rGO/PLA composite, PM/PLA composite, and PMrG-3/PLA composite: (a) cooling process; (b) heating process (the mass fractions of the additives in the composites are all 10%). Image Credit: Yang, P., et al., Polymers
Applications of PA
When applied on its own as a flame retardant, PA, on the other hand, causes the composite to decompose, reducing the igniting time. As a result, PA is widely used to manufacture flame retardants following reconfiguration or in combination with other materials in terms of increasing flame retardant efficacy.
Melamine is a common component in thermochromic flame retardant systems, and it is often used in conjunction with phosphorus-based fire retardants to enhance their fire resistance. Mostly during manufacturing of the flame retardant of epoxy resin, melamine was combined with PA, which reduced the pHRR, total smoke release (TSR), and fire growth rate of the epoxy resin-based composite.
The Techniques to Make the PMrG
The synthesized PMrG has been used as a fire retardant with in PLA as well as the PMrG/PLA composite production process. To reach an acceptable dispersion condition, we first created the PMrG/dichloromethane solution and then added PLA particles to ensure total dissolving. DSC was used to investigate the crystallization and thermal characteristics of PLA and its composites.
Furthermore, when the amount of melamine and PA in the PMrG/PLA composite grew, so did the crystallization temperature. As a result, the nucleation enhancement effect of PMrG was mostly attributed to its melamine and PA ingredients. Furthermore, the disappearance of the cold crystalline peak of the PM/PLA and PMrG-3/PLA composites demonstrates their increased crystalline ability, whereas the temperature dependence and melting temperature of PLA were little affected.
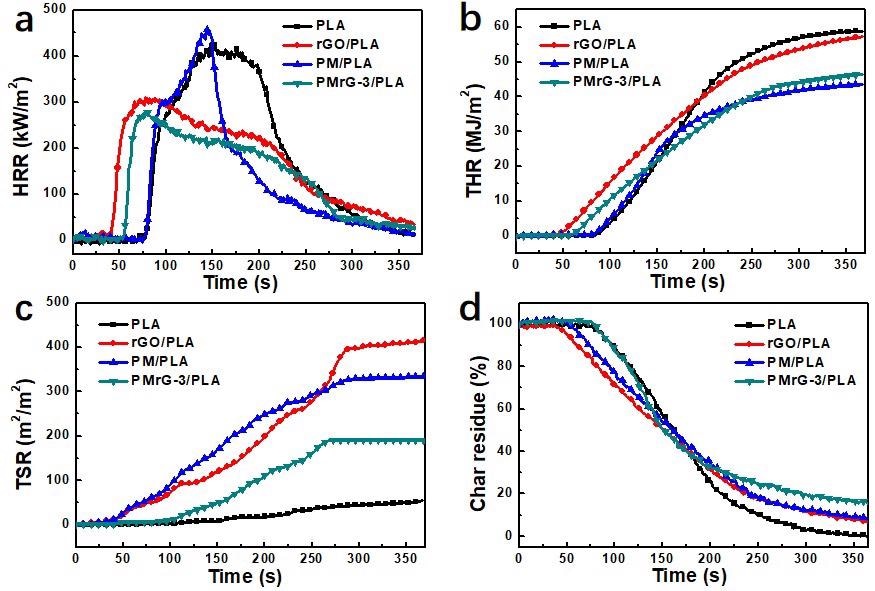
(a) Heat release rate, (b) total heat release, (c) total smoke release, and (d) char residue curves of the neat PLA and its composites under an external heat flux of 35 kW/m2 (the mass fractions of the additives in the composites are all 10%). Image Credit: Yang, P., et al., Polymers
Result of this Research
rGO, being the foundational element of PMrG that has a multilayer structure, offers a barrier effect, lowering the composite's burning rate. When PMrG is used as a flame retardant, the evaporation of the PA and the dissolution of the melamine exist immediately with the combustion of the composite, producing non-flammable vapors such as H2O and NH3, which water down the oxygen levels on the composite's surface.
As a result, the total heat release is significantly reduced. The synergistic impact of the rGO, melamine, and PA elements in PMrG, which support the creation of a compact char layer during burning, effectively limiting the emission of heat and smoke, is credited with the increased flame-retardant efficacy of PMrG-3/PLA materials.
The Best Advantages of this Flame Retardant
The production of smoke from materials is considered as one of the key factors contributing to death, and a reduced smoke production rate and TSR indicate a reduced smoke risk and a longer evacuation time in a fire disaster. The plain PLA produced very little smoke throughout the burning process, however, the introduction of rGO or PM dramatically enhanced the amount of smoke produced.
This was primarily ascribed to the rGO or PM causing incomplete combustion of the polymers. As a result, when rGO or PM was applied to PLA to reduce heat emission, the smoke suppression of the polymers worsened. When 10% wt PMrG was used as the flame retardant, the resulting PMrG/PLA composite had a lower TSR value due to the higher level of melamine and PA in the PMrG.
Further Research in Nano Layered Substances
Melamine's poor compliance with the bulk of polymeric composites, on the other hand, degrades its dispersal in composites, lowering its flame resistance. As a result, researchers are attempting to incorporate carbon nano-layered substances such as graphene, carbon nanotubes, as well as other carbon nano-layered substances.
Graphene has been employed as a component of several flame-retardant technologies because it is a nonflammable material with a multilayered structure that provides good heat insulation and improved thermostability.
Reference
Yang, P., et al. (2021). A Novel Self-Assembled Graphene-Based Flame Retardant: Synthesis and Flame Retardant Performance in PLA. Polymers 2021, 13(23), 4216; Published: 1 December 2021. https://www.mdpi.com/2073-4360/13/23/4216
Disclaimer: The views expressed here are those of the author expressed in their private capacity and do not necessarily represent the views of AZoM.com Limited T/A AZoNetwork the owner and operator of this website. This disclaimer forms part of the Terms and conditions of use of this website.