A team of researchers at the Changwon National University, South Korea have published a study in the journal Materials Research and Technology that investigates the use of wire arc additive manufacturing (WAAM) in machine tool remanufacturing.
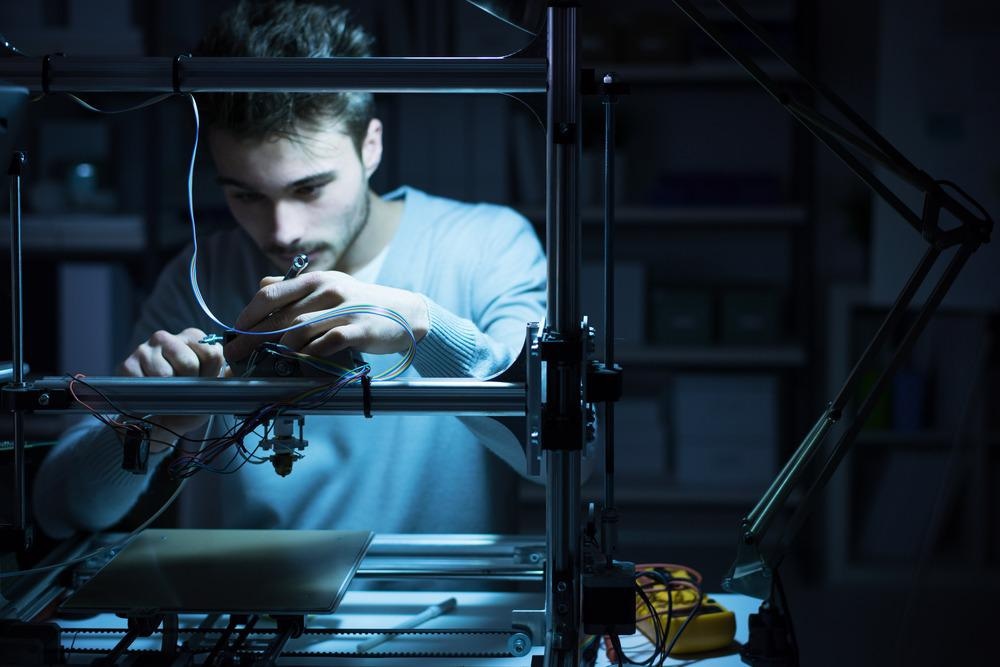
Study: Repair of damaged parts using wire arc additive manufacturing in machine tools. Image Credit: Stock-Asso/Shutterstock.com
Manufacturing is highly dependent on reproducibility which in turn is dependent on mechanical parts that perform in their intended usage. At times these parts may malfunction or require repair or replacement. This is true across a broad range of industries such as automotive, aerospace, and machine tools, therefore, research on damaged machine tool parts is required for repair/replacement.
Yet, such parts can be made up of complex geometries which are difficult and time/labor-intensive to fabricate using conventional processes including rolling, forging, and casting. A new study in the journal Materials Research and Technology considers how wire arc additive manufacturing (WAAM) can be used for machine tool remanufacturing.
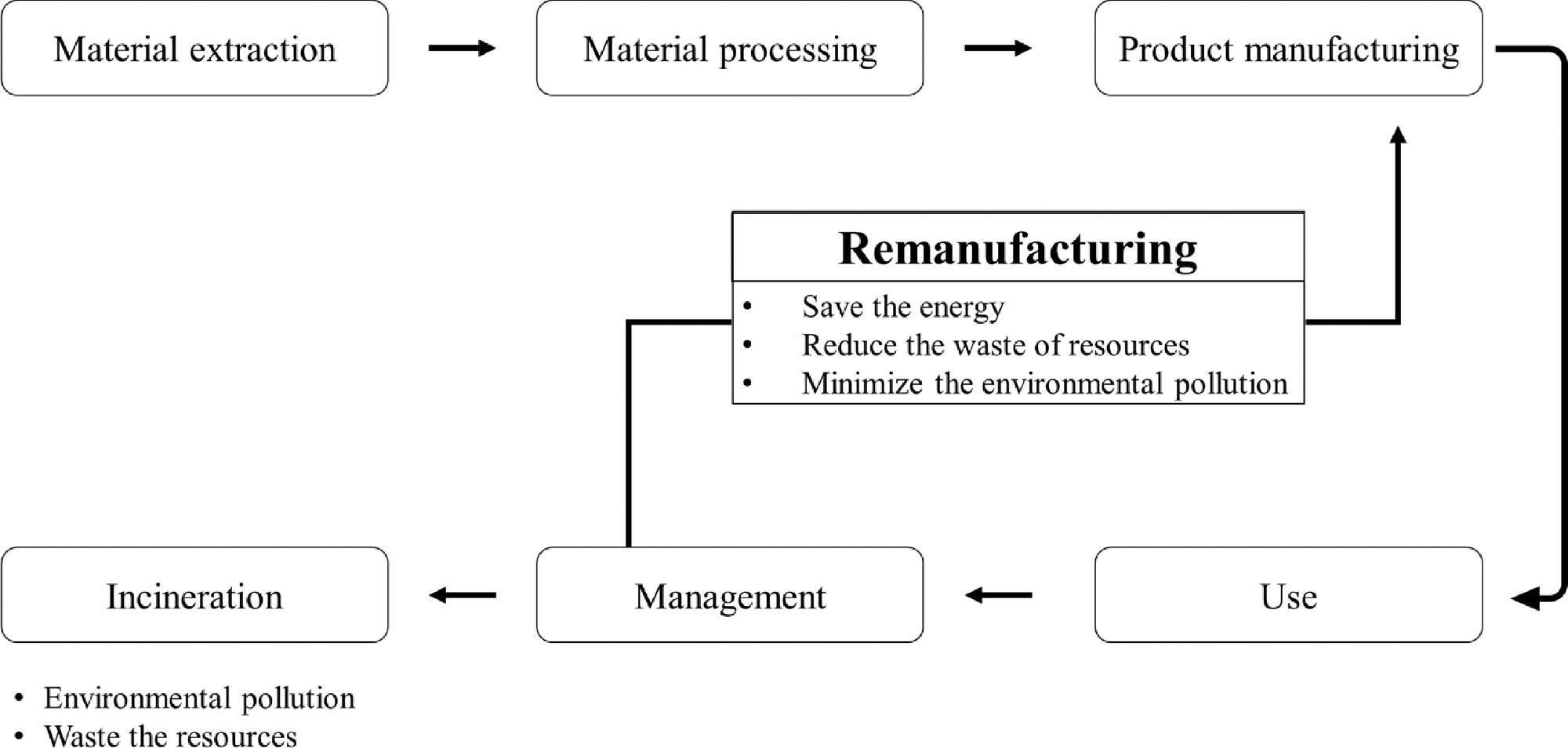
Lifecycle of a product for remanufacturing. Image Credit: Lee J-H et al., Journal of Materials Research and Technology
“In general, these parts are often damaged owing to falls of the workpieces and the inexperience of workers; the cross slide is one of the parts damaged most often in a lathe,” explains Dong-Hyeon Kim at the Mechatronics Research Center, Changwon National University.
Accordingly, the researchers selected the cross slide as an example for their study in order to demonstrate how effective WAAM could be in the repair of mechanical tools.
What is WAAM?
WAAM, or wire arc additive manufacturing is a 3D printing technique that utilizes arc welding to build up the component part in a sequence of layers. Belonging to the direct energy deposition (DED) family of additive manufacturing (AM) processes.
WAAM combines AM with gas metal arc welding (GMAW), a welding process used for fusing metal parts using an electric arc. Typically, the production of parts using WAAM is performed by an automated welding robot arm to melt the wire to form 3D parts of intricate and complex geometries.
WAAM outperforms conventional manufacturing processes and other DED techniques in several ways. These include material savings with targeted material application, additional design freedoms, low start-up costs (up to 60% cheaper than subtractive CNC manufacturing), and minimal distortions or aberrations in the parts.
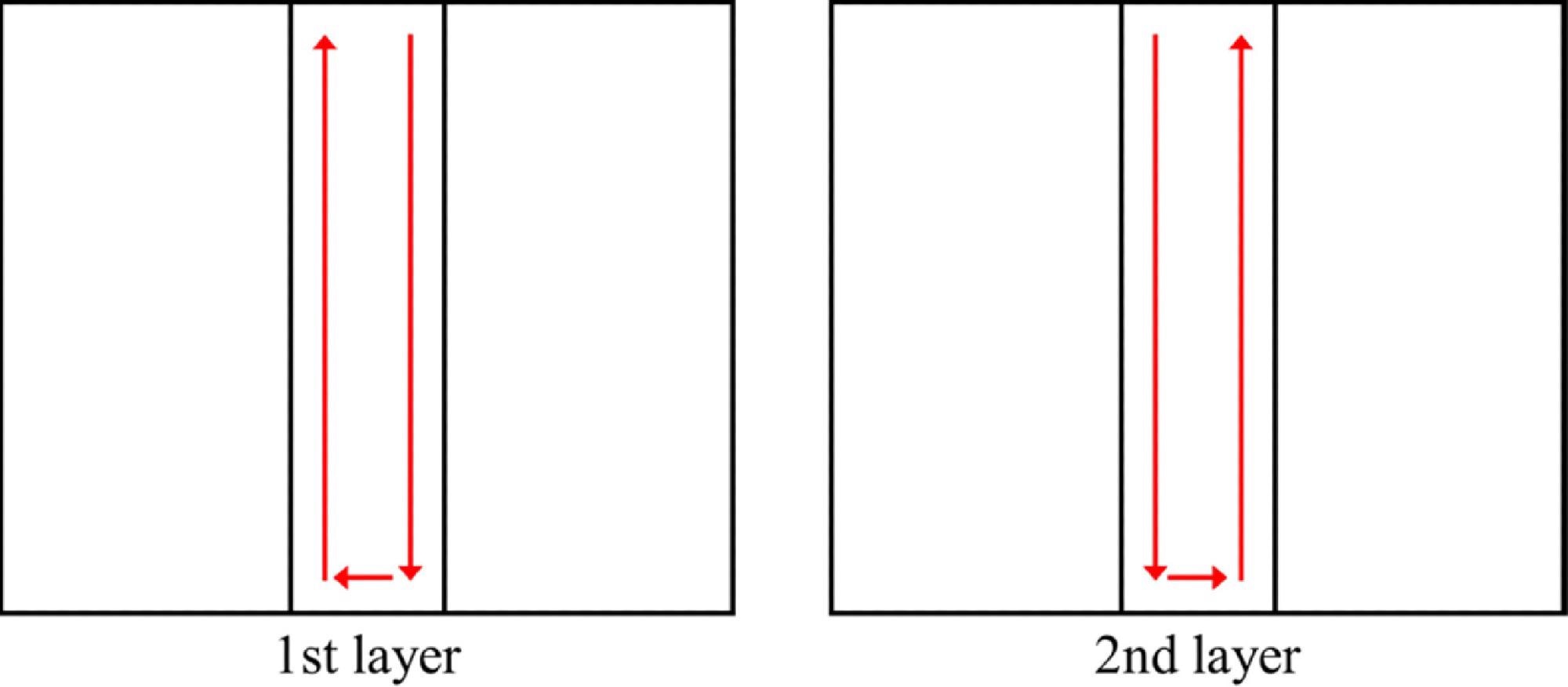
Deposition path used in experiments for parameter determination. Image Credit: Lee J-H et al., Journal of Materials Research and Technology
Repairing Parts with WAAM
Generally speaking, there are two kinds of defects in machine tool parts: structural defects and morphological defects. For the purpose of this study, Kim and his colleagues only considered morphological defects which include cracks, holes, notches, and surface marks.
As such, the damaged parts of a cross slide were repaired with the application of WAAM in machine tool remanufacturing. The cross slide was initially produced using gray cast iron, and nickel wire was employed as the WAAM deposition material for repair. A different material was selected for repair to simplify the analysis of the microstructure, chemical composition, and mechanical property of the repaired parts.
The team took the decision to partially cut the surface of the substrate flat so that the nickel deposition materials could be evenly applied in damaged areas: “Nickel wires were used as deposition materials to suppress cracks and pores in the WAAM,” stated Kim.
Repair of the cross slide was successfully achieved by filling the damaged area using WAAM at different current speeds set as parameters, 100 A, 180 A, and 260 A respectively.
The repaired cross slides were then subsequently analyzed at each of the current speeds to assess overall performance and properties.
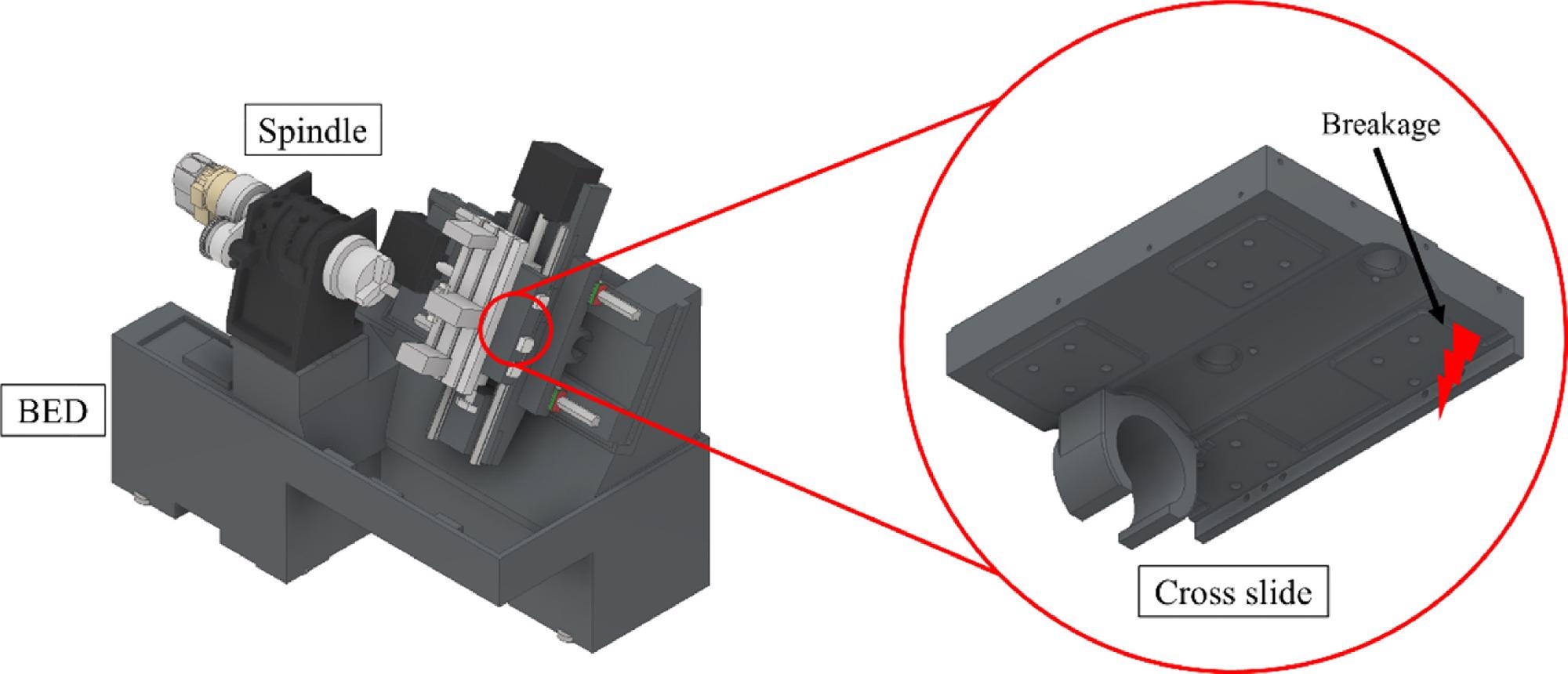
Example of the damaged parts in the lathe. Image Credit: Lee J-H et al., Journal of Materials Research and Technology
The team discovered that the parts repaired at 180 and 260 A were not dissimilar with the species at 180 demonstrating a 17% increase in hardness to the cast iron substrate whereas the species repaired at 260 showed an increase in hardness of 15%.
The researchers determined that post-processing was essential for adjusting the specifications of the original parts after AM was performed: Post-processing of the repaired specimen was performed with the same specifications as those for the original parts. Finally, the repair was successfully carried out on the original parts,” explains Kim.
Overall, the study demonstrates the successful application of WAAM for repairing machine tool parts using alternative materials on a cast iron substrate. The team state that this method can be applied to various mechanical parts including turbine blades, impellers, and machine tools. This opens up the window of opportunity for using WAAM in the repair of parts across a range of industries.
References and Further Reading
Lee J-H, Lee C-M, Kim D-H, Repair of damaged parts using wire arc additive manufacturing in machine tools, Journal of Materials Research and Technology, https://www.sciencedirect.com/science/article/pii/S2238785421014356?via%3Dihub
Disclaimer: The views expressed here are those of the author expressed in their private capacity and do not necessarily represent the views of AZoM.com Limited T/A AZoNetwork the owner and operator of this website. This disclaimer forms part of the Terms and conditions of use of this website.