A novel breakthrough of polymer assimilation from graphene oxide (GO) precursor allows for the controlled thermoplastic formation of graphene films, as stated in the journal Nano-Micro Letters. The thermoplasticity of GO solids is enabled by the intercalated polymer via thermally stimulated polymer chain activity.
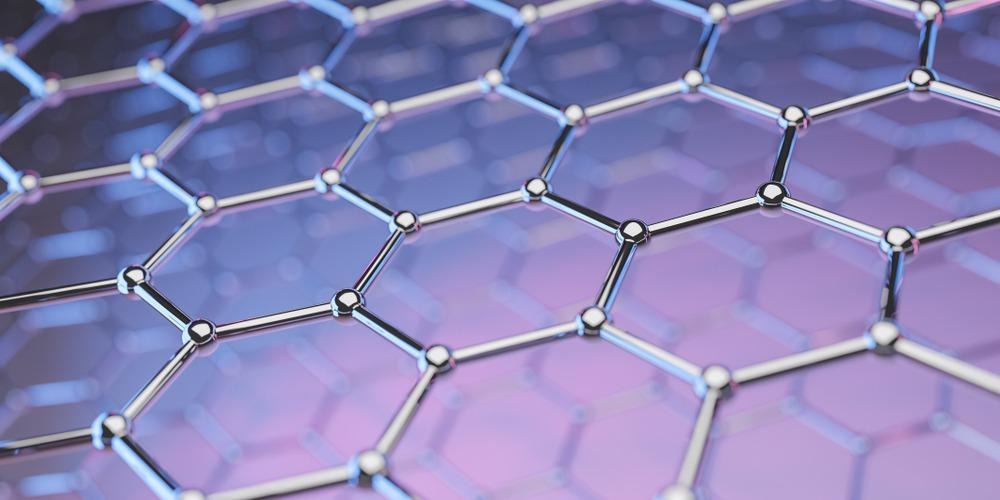
Study: Precise Thermoplastic Processing of Graphene Oxide Layered Solid by Polymer Intercalation. Image Credit: Production Perig/Shutterstock.com
Researchers discovered a defined threshold containing intercalated polymers that can increase interlayer spacing above 1.4 nm to activate thermoplasticity, which has become the criterion for the thermal plastic formation of GO solids. The flat GO-composite sheets are thermoplastically formed into Gaussian curved shapes and embossed with surface relief patterns.
The thermoplastic technique significantly expands the forming capabilities of GO materials and other multilayer materials, promising varied structural designs for a broader range of applications.
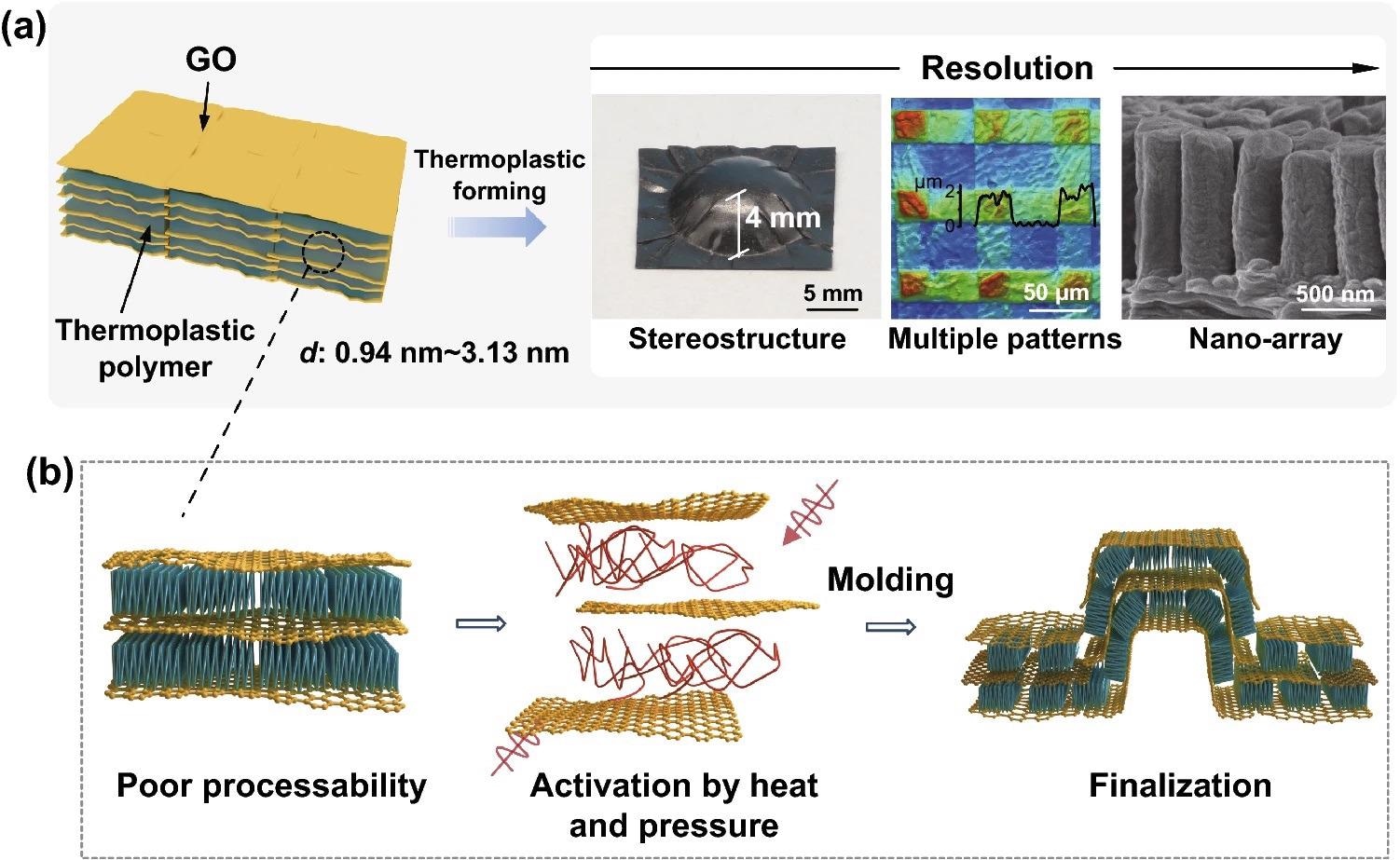
a The thermoplastic forming process of Pi-GOS from flat films into different embossed structures ranging from macro- to nano-scale. b Schematic diagram of the thermoplastic mechanism, including the sliding of GO sheets and the activation of polymer chains under pressure and heating. Image Credit: Li, Z., et al., Nano-Micro Letters
Graphene as a Substance
Graphene macroscopic substances have shown promising qualities and offer a wide range of applications in engineering structures, heating systems, sensors, and electrical devices. To keep up with the demands of more diversified graphene applications, various forming processes are required to design and create exact forms and structures.
Graphene processing has so far depended on solvent-mediated processes such as dilute-solution assembling and solvent-plasticized formation. Dilute dispersions of graphene and its derivatives are treated through solution casting, infiltration, spray coating, and wet-spinning in the former approach, yielding a variety of morphologies such as coatings, films, and fibers.
Because of the substantial volume loss during solution evaporation, dilute-solution processing offers poor structural precision.
Traditional Method on Diluting Graphene Oxide
Solution castings, infiltration, plasma spraying, and wet-spinning are used to treat dilute suspensions of graphene and its derivatives, resulting in a variety of forms such as coating, film, and fiber. Because of the substantial volume loss during solution evaporating, dilute-solution processing offers poor structural accuracy.
A hydroplastic forming approach, on the other hand, was recently developed to increase structural accuracy by reducing solvent contents and producing a near-solid manufacturing state with total solids of 20–50%.
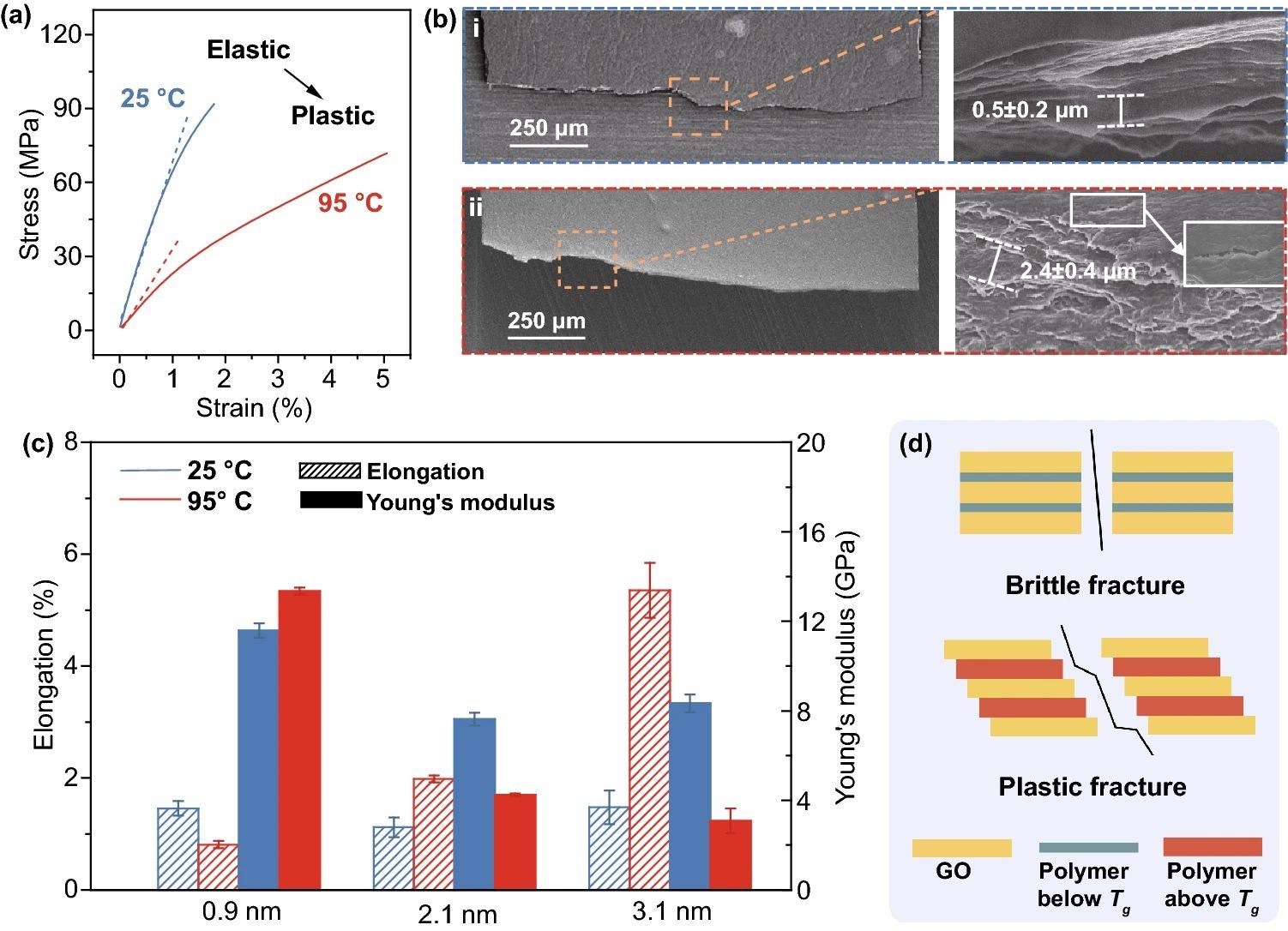
a Typical stress–strain curves of Pi-GOS (d = 3.1 nm) at 25 °C (blue) and 95 °C (red). b SEM images of transverse cross-section morphology of Pi-GOS (d = 3.1 nm) after tensile breaking at 25 °C (top) and 95 °C (bottom). c Young’s modulus and elongation of Pi-GOS with different d-spacing at 25 °C (blue) and 95 °C (red). d Schematics of brittle tensile fracture of Pi-GOS below Tg and plastic tensile fracture above Tg. Image Credit: Li, Z., et al., Nano-Micro Letters
It is an ultimate goal to advance the thermoplastic formation of graphene beyond dilute chemical functionalization for the environmental benefits of avoiding solvents with high processing accuracy for minor volume changes in the thermoplastic process.
Thermoplasticity in Graphene
A thermoplastic is a form of plastic comprised of natural polymers that soften when heated and harden when chilled. The physical properties of thermoplastics alter when they are heated, and then they become a homogeneous liquid that can be molded and resized.
Graphene thermoplastic manufacturing is restricted because of its extraordinarily high glass-transition temperature of up to 6300 K, which surpasses the graphene breakdown temperature. An intuitive deduction for achieving thermoplastic manufacturing of graphene is to combine graphene with the inherent thermoplastic polymer components.
Previous findings on graphene-polymer composites (typically less than 40% graphene) appear to have limited advice to the intended thermoplastic manufacturing of graphene in this polymer-rich processing spectrum.
Method of the Research
Solvent-free thermoplastic formation of graphene oxide solid by polymeric intercalation has a size accuracy ranging from macro- to sub-micrometer. The temperature transition of the intercalated polymer imparts plasticity to the bulk composite sheet. The authors show that when the interlayer spacing surpasses 1.4 nm, the glass-transition temperature appears and the rigid polymer-intercalated GO solid (Pi-GOS) can turn into plasticity, indicating thermal forming criteria of greater than 45 percent.
Researchers forged flat sheets into stereoscopic structures with varying Gaussian curvatures in the thermoplastic range. They devised a thermoplastic imprinting method for creating multiscale surface designs and periodic arrays with high size accuracy. Thermoplastic imprinting enables the modification of features such as Janus material for actuators and a reactive film surface with voltage-dependent wetting.
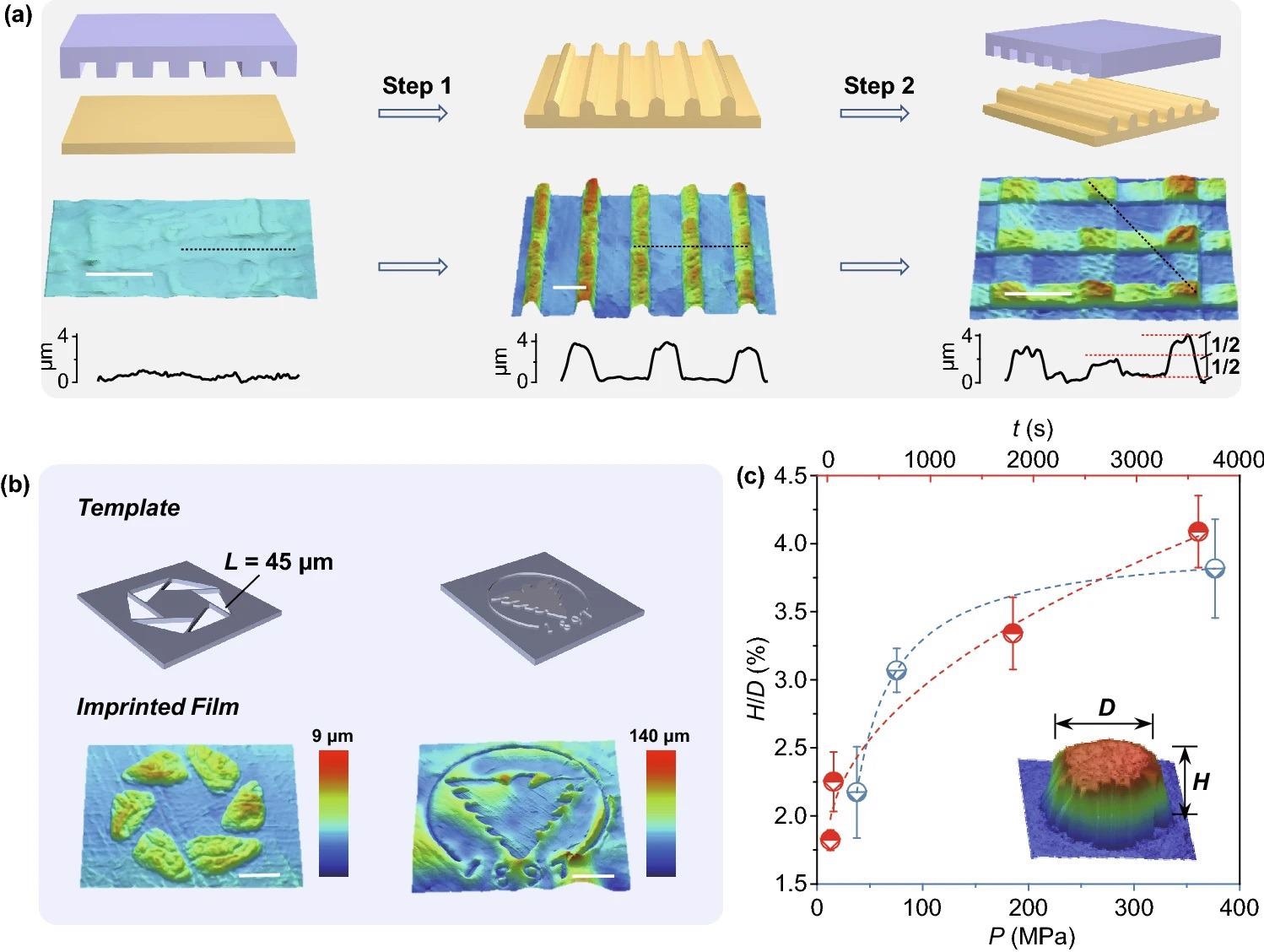
a Representation of multi-imprinting process from flat to micro-pattern stages. Scale bar, 50 μm. b Surface patterns on Pi-GOSs through micro imprinting: simple hexagon formed by triangles (left), embossment of the ZJU logo (right). Scale bars, 50 μm (left), 2 mm (right). c The curve of height-diameter ratio versus pressure and time. Dashed lines correspond to the fitting results and points represent experiment results (error bars are based on the standard error of the mean). Image Credit: Li, Z., et al., Nano-Micro Letters
The Advantage of Thermoplastic GO
These materials are used in a wide range of items, including garments, nonstick kitchenware, carpets, and scientific instruments. After thermal annealing, these complex deformations change the mechanical properties and sensitivity of Pi-GOS, while the thermoplastic building materials retain high thermal and electrical conductivity.
When GO sheets and PVA chains are pressed into nanoholes beneath high pressure at high temperatures, they create a hump enveloped in GO sheets when they cool to room temperature. It has a strong structure, according to the results. Polymers intercalation using graphene oxide precursor creates a solvent-free thermoplastic forming technique for graphene products.
Further Research
To construct micro-scale objects on the surface of Pi-GOS, researchers employed thermo-imprinting, which may be done twice. Templates of matching size may be used to shape the composites solids into micro-patterns, which can be changed using a programmed imprinting method. This result demonstrates how a single-sized template may be used to generate complicated structures.
Reference
Li, Z., et al. (2021). Precise Thermoplastic Processing of Graphene Oxide Layered Solid by Polymer Intercalation. Published: 04 December 2021. Nano-Micro Letters volume 14, Article number: 12 (2022). https://link.springer.com/article/10.1007/s40820-021-00755-8
Disclaimer: The views expressed here are those of the author expressed in their private capacity and do not necessarily represent the views of AZoM.com Limited T/A AZoNetwork the owner and operator of this website. This disclaimer forms part of the Terms and conditions of use of this website.