In a recent study published in the journal Metals, researchers from Germany analyzed a new patented low-cost steel that can resist corrosion at high temperatures and in a molten (solar) salt environment, when used for thermal energy storage (TES) and concentrated solar power (CSP) applications such as salt carrying pipes and containers.
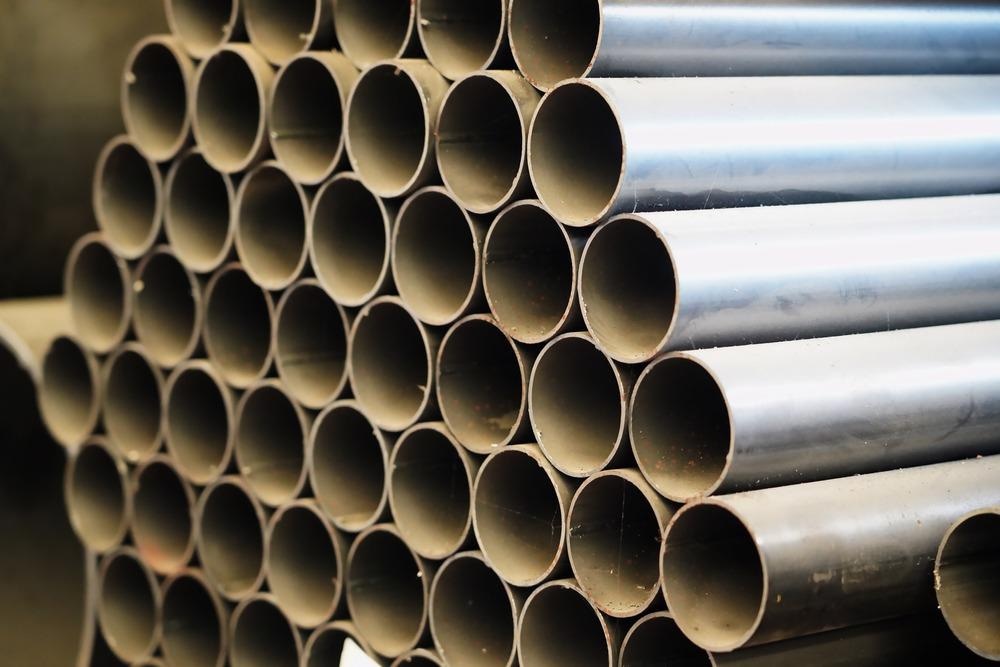
Study: A New Approach to Low-Cost, Solar Salt-Resistant Structural Materials for Concentrating Solar Power (CSP) and Thermal Energy Storage. Image Credit: pinkfloyd yilmaz uslu/Shutterstock.com
The new steel (LB2230) is ferritic in nature, forms a protective layer of alumina (Al2O3) when it comes in contact with the molten salt, and is internally strengthened by the formation of intermetallic Laves-phase. Also, it demonstrated longer stability against the other two commercially available steel viz. Haynes 214 and Crofer®22 H.
The Demand for Corrosion-Resist Steel in CSP and TES Power Plants
CSP-TES power plants are a new generation of renewable energy solution in which a heat transfer fluid or molten (solar) salt is heated by concentrated solar energy followed by storing in a TES system. This stored thermal energy is further used for steam generation and thereby electrical energy is generated using steam downstream of the process.
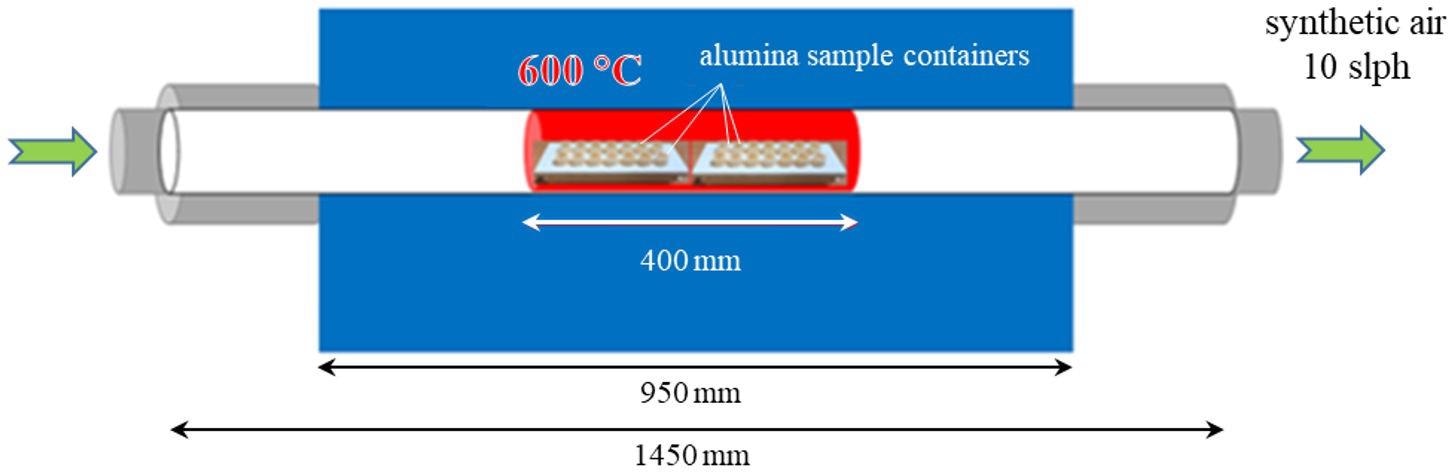
Schematic of the salt corrosion experimental set-up utilized at Forschungszentrum Jülich GmbH. Image Credit: Aarab, F et al., Metals
Currently, the commercially used solar salt, for heat transfer and storage, is a eutectic mixture of 60 weight % sodium nitrate (NaNO3) and 40 weight% potassium nitrate (KNO3). However, these molten metal nitrates are highly corrosive towards metal pipes and container walls, which hinders their long-term operation. Nickel (Ni)-based superalloys or austenitic stainless-steel grades are highly corrosion resistant, but they are highly expensive as well.
Moreover, the thermal efficiency of these CSP power plants ranges from 30-40%, which is well below the most advanced steam power plants with 46% efficiency. To increase the efficiency, the CSP power plants need more concentrated solar energy, which will result in a further increase in the operating temperature of molten salts and related corrosion issues.
About the Study
In this study, researchers compared the new steel LB2230 with Crofer®22 H and Haynes 214 for its potential application in the CSP-TES system. LB2230 is an aluminum (Al) based derivative of chromia (Cr2O3) forming Crofer®22 H, which means LB2230 forms an α-Al2O3 corrosion protective layer, whereas Crofer®22 H forms Cr2O3 layer, when it comes in contact with the molten salt.
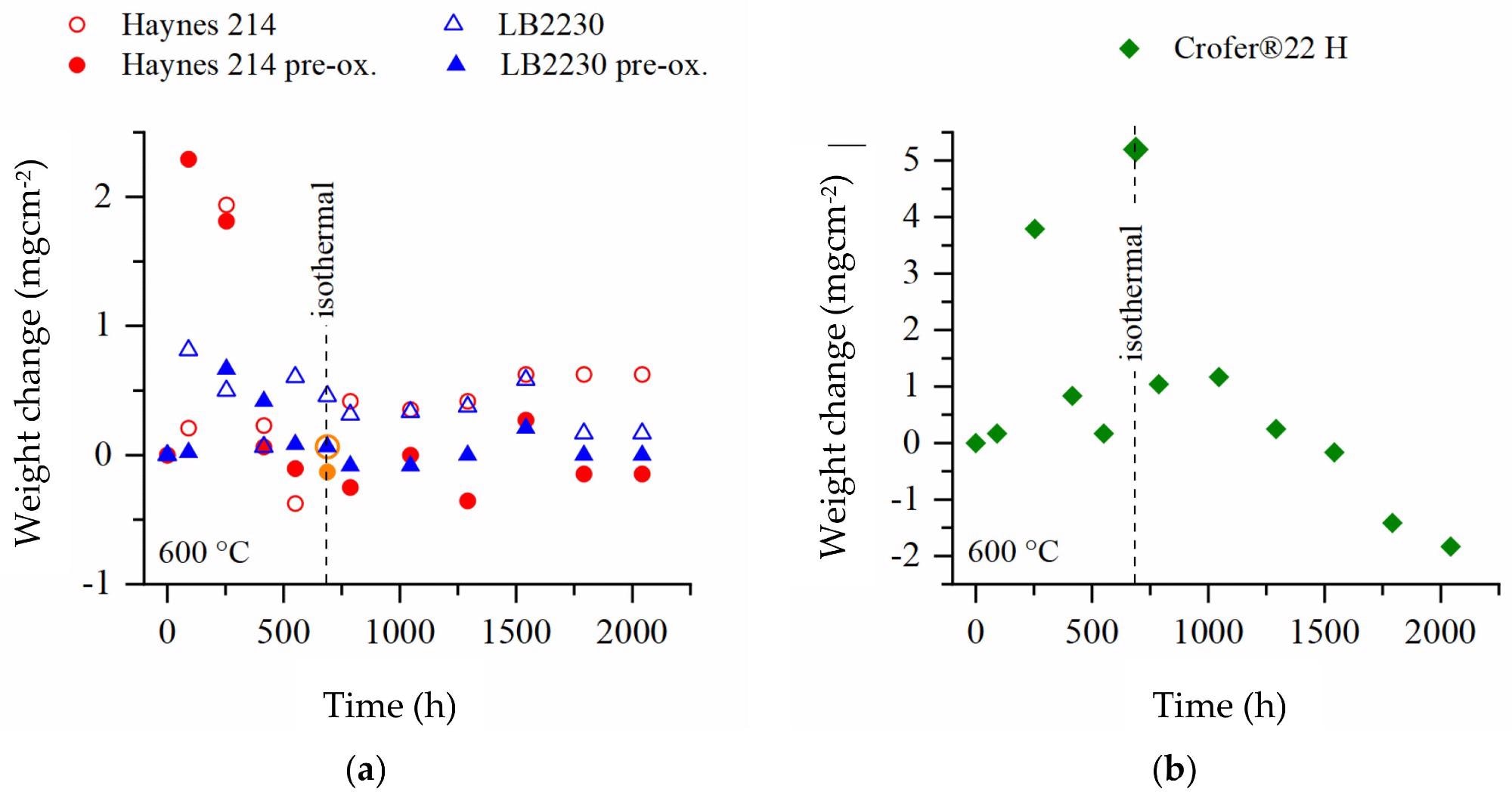
Weight changes of corrosion specimens during annealing in solar salt at 600 ℃ (discontinuously performed by FZ Jülich, IEK-2; isothermally by DLR): (a) Al2O3-formers and (b) Cr2O3-formers (mean values of 2 specimens in case of discontinuous testing, single value in case of continuous exposition). Image Credit: Aarab, F et al., Metals
Both types of steels have similar compositions of additive metals and they are internally strengthened by the formation of intermetallic Laves-phase, but Crofer®22 H contains 22 weight % chromium (Cr), which is replaced by Al for LB2230. Similarly, the other corrosion-resistive steel Haynes 214 forms an Al2O3 protective layer at 955 ℃ and above, while below 955 ℃, it forms a low corrosion-resistive mixed chromia/alumina layer. However, the issue with Haynes 214 at higher temperatures (595-925 ℃) is that it is susceptible to strain-age cracking due to precipitation of γ’-Ni3Al particles.
Furthermore, two different types of corrosion tests were performed on all three steel samples. In the first test, steel samples with their respective containers were placed inside a horizontal alumina tube furnace followed by filling each container with salt and discontinuous annealing at 600 ℃ for 2042 hours.
In the second test, all the steel samples were placed in a common alumina crucible followed by filling the crucible with the salt and heating it inside a stainless-steel chamber under isothermal conditions and a continuous flow of synthetic air of 6 sl/h.
Observations
Scanning electron microscopy (SEM) shows the austenitic Haynes 214 and ferritic LB2230 form a protective Al2O3 layer at a temperature higher than 1000 ℃. Also, a temperature of 1075 ℃ was necessary to prevent uncontrolled precipitation of Laves phase in LB2230. The mean Al2O3 layer thicknesses of Haynes 214 and LB2230 in the pre-oxidation state were 0.2 µm and 0.8 µm, respectively.
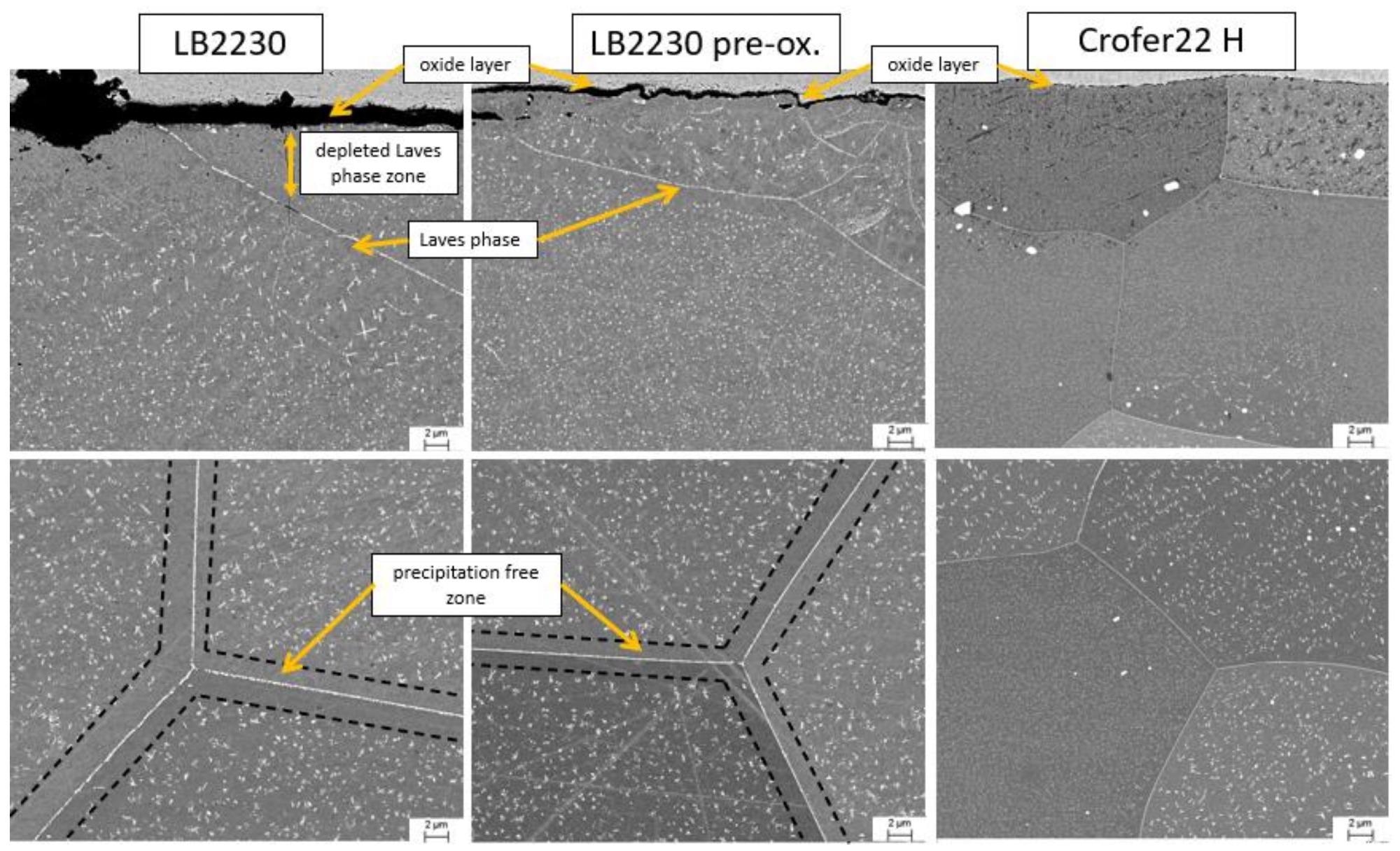
SEM images of Laves phases precipitation in LB2230, pre-oxidized LB2230 and Crofer®22 H after 550 h of discontinuous corrosion testing in solar salt at 600 °C. Image Credit: Aarab, F et al., Metals
Moreover, all samples indicated initial weight gain followed by a series of weight loss/grain and finally a continuous weight loss over time. The Crofer®22 H demonstrated double weight gain or loss than both Haynes 214 and LB2230 before entering into continuous weight loss after 1046 hours.
Only Crofer®22 H displayed macroscopic indications of spallation and scale cracking whereas LB2230 did not show any scale cracking owing to the lower mismatch between thermal expansion coefficients of the ferritic matrix and the formed oxide scales.
As Al2O3 is more stable than Cr2O3, compared to Haynes 214 and Crofer®22 H, pre-oxidized LB2230 consumed less Al and Cr during oxidation at the surface, thus there were more Al and Cr available for Laves phase precipitation and strengthening in LB2230. Also, the molten metal dissolved the highest Cr from Haynes 214 followed by Crofer®22 H.
Conclusions
The researchers analyzed an Al-alloy-based, low cost, ferritic, and Laves phase-precipitated patented LB2230 steel and compared it with two other commercial high corrosion-resistive steel namely, chromia forming Crofer®22 H and austenitic alumina forming Haynes 214.
LB2230 demonstrated more long-term stability and high operating temperature withstanding ability without scale cracking and strain-age cracking. Additionally, it does not facilitate Cr diffusion, provides the thickest alumina layer and higher Laves-phase formation that internally strengthens it; thus LB2230 is a suitable corrosion-resistive structural steel for high-temperature CSP_TES application.
Reference
Aarab, F., Kuhn, B., Bonk, A., Bauer, T., A New Approach to Low-Cost, Solar Salt-Resistant Structural Materials for Concentrating Solar Power (CSP) and Thermal Energy Storage (TES). Metals, 2021, 11, 1970. https://www.mdpi.com/2075-4701/11/12/1970/htm
Disclaimer: The views expressed here are those of the author expressed in their private capacity and do not necessarily represent the views of AZoM.com Limited T/A AZoNetwork the owner and operator of this website. This disclaimer forms part of the Terms and conditions of use of this website.