By Susha Cheriyedath, M.Sc.Reviewed by Skyla BailyJan 13 2022
A team of researchers recently published a paper in the journal Materials that showed the viability of using the gas nitriding process and duplex aging to modify the surface of titanium alloys in order to make them wear-resistant.
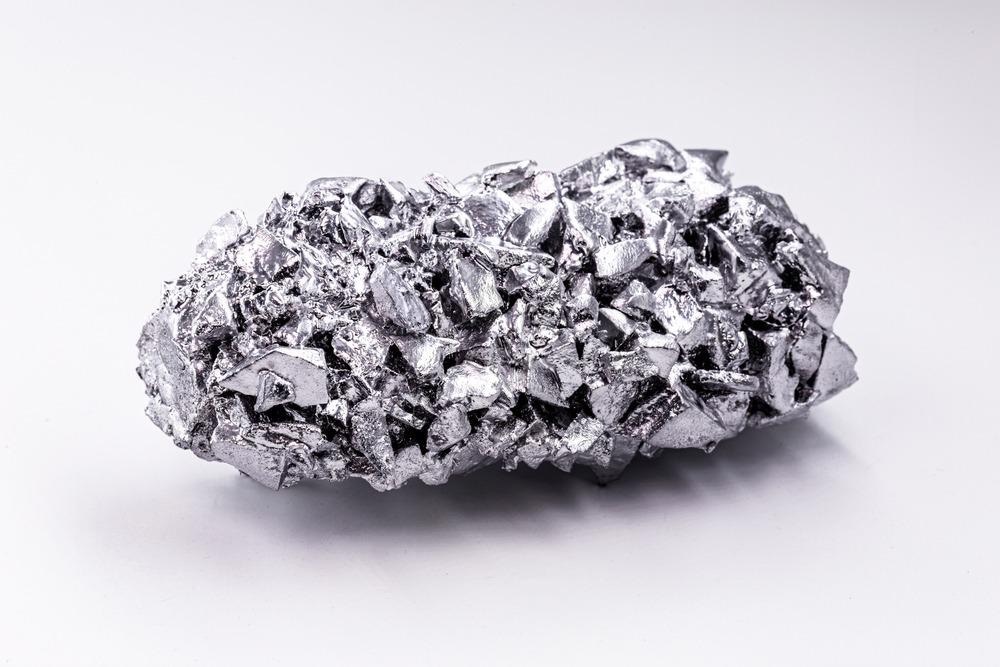
Study: Duplex Aging and Gas Nitriding Process as a Method of Surface Modification of Titanium Alloys for Aircraft Applications. Image Credit: RHJPhtotoandilustration/Shutterstock.com
In the study, the researchers observed the effect of nitriding and duplex aging on the wear resistance of BT22, a double-phase titanium alloy. Both heat treatment and nitriding were applied simultaneously to observe their effects.
Importance of Titanium
Aerospace is one of the major sectors that require advanced engineering solutions and structural materials, such as titanium alloys, owing to their excellent strength-to-weight ratio and high corrosion resistance. However, untreated titanium alloys demonstrate a low wear resistance, which limits their use in several applications.
Although adhesion is critical for every coating, diffusion-saturation is more suitable for improving the wear resistance of metals. However, the titanium alloys absorb gases when heated at 250-300 oC temperatures, which makes the diffusion-saturation process ineffective for such alloys. Thus, a thermochemical treatment was proposed for the titanium alloys to realize controlled saturation of the alloy surface with interstitial atoms in order to increase the wear resistance.
Positioning of the specimens and pin counterparts: (a)—tested specimens, (b,c)—dimensions and positioning of the counterparts on the disc surfaces and the order of the wear tests. Image Credit: Tisov, O et al., Metals
Study Background
Currently, the two-phase high-strength BT22 titanium alloy is widely used in high load applications. The major features of the BT22 include higher heat and corrosion resistance, greater ease of handling, and better weldability and machinability. The high strength of the alloy can be attributed to α + β microstructure, obtained by the aging and solid solution treatment of the alloy.
Although the microstructures and mechanical properties of the BT22 alloy were thoroughly studied, its ability to be thermochemically processed has not been studied until now. The current study mainly focused on the effectiveness of thermochemical treatment and duplex aging in improving the wear resistance of the heavy-duty BT22 titanium alloy.
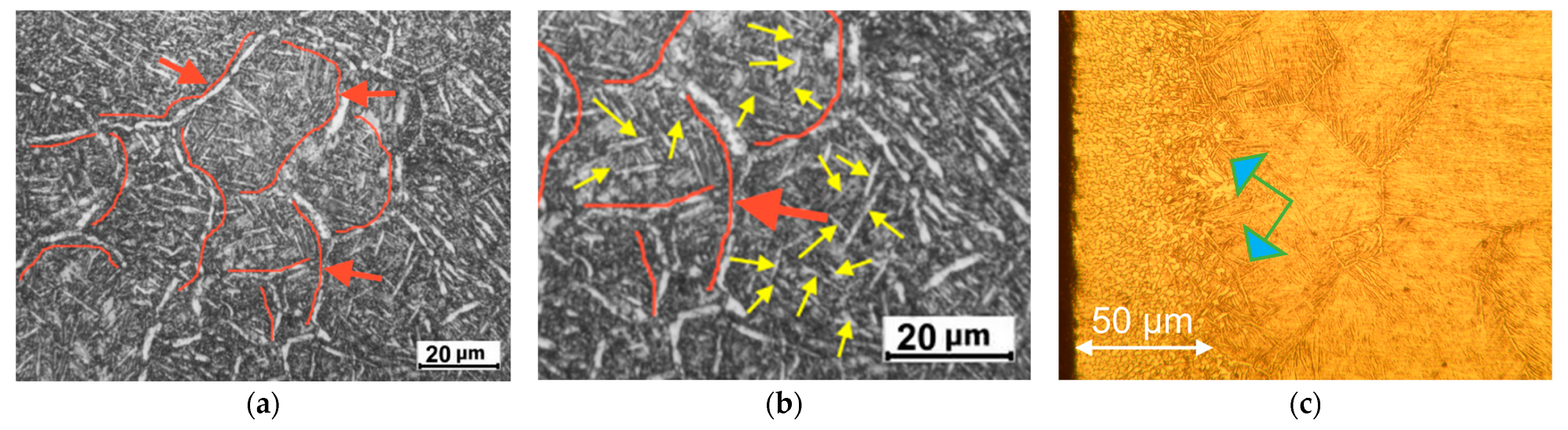
Microstructure of the BT22 alloy: (a) α phase on the boundaries of β grains, in the as-supplied condition; (b) randomly oriented α phase inside β grains, in the as-supplied condition; (c) after nitriding. The arrows show the boundary of the nitrided layer. Image Credit: Tisov, O et al., Metals
The Study
In this study, the tribological performance of the treated alloy was tested in a pin on disc configuration under dry sliding conditions. An ultrasonic alcohol bath was used to degrease the discs before the wear and nitriding tests. The wear and the coefficient of friction (COF) of the tribocouple were also observed.
An SEM-FIB DualBeam Scios 2 was used for determining the dominant wear modes of both non-heat-treated and treated samples. Gas nitriding was applied to the treated BT22 alloy, and a DRON-3.0 X-ray diffractometer was used for the phase analyses of the nitride surface, while a T11 pin-on-disc tribometer was used for the wear tests.
An atmospheric nitrogen pressure and a temperature range between 750 oC and 850 oC were selected as the process parameters in the study as higher gas pressure and temperatures often lead to harder and thicker surfaces.
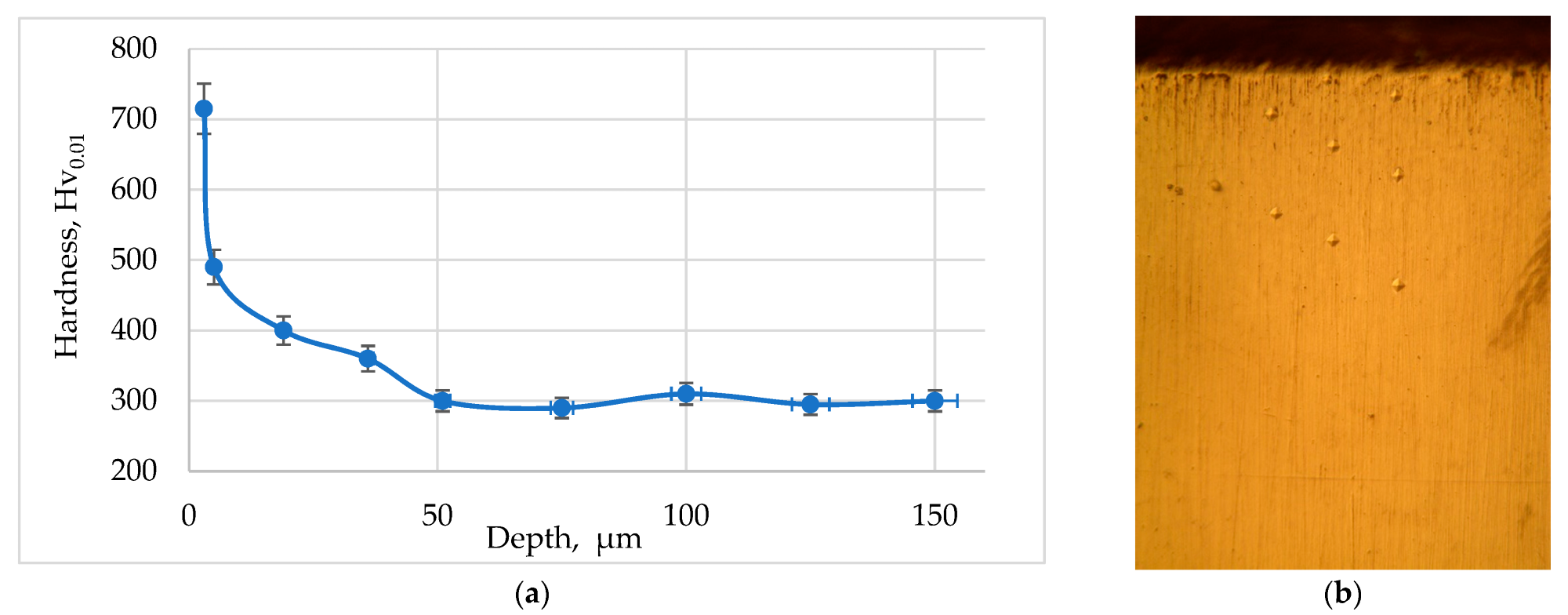
Hardness profile of the nitrided BT22 alloy (a) and the oblique section with indents (b). Image Credit: Tisov, O et al., Metals
Observations
After the initial nitriding tests, the surface color of the treated alloy changed from silvery to yellow-gold, which indicated the presence of titanium nitrides. Additionally, the content of the α-phase was similar to that of the β-phase. After double step nitriding, the thickness of the nitride layers was measured at 50 µm, and the alpha phase particles became finer. The size of the beta particles cannot be measured due to the change in the morphology of the grain boundary phase.
Using the microhardness measurements, the thermodiffusion layer thickness was measured at 40-50 µm, which is normal for this surface modification technology and similar to that of the nitride layer. The hardness of the alloy was measured at 300 HV0.01, indicating a significant increase after the treatment. The hardness of the surface was uniform, which indicated a stable saturation process. The microhardness of the subsurface was 715 HV0.01, while the maximum hardness of the surface was measured at 1190 HV0.01.
Observations from the wear resistance test indicated that the wear resistance of the nitride alloy was higher than the untreated alloy. The nitride layer in the surface prevents contact between the two metals. The average COF value decreased from 0.6 to 0.5 after the surface of BT22 was saturated with nitrogen. Moreover, the abrasive wear was dominant in the nitride samples, while adhesive and delamination wear was dominant in the untreated alloys.
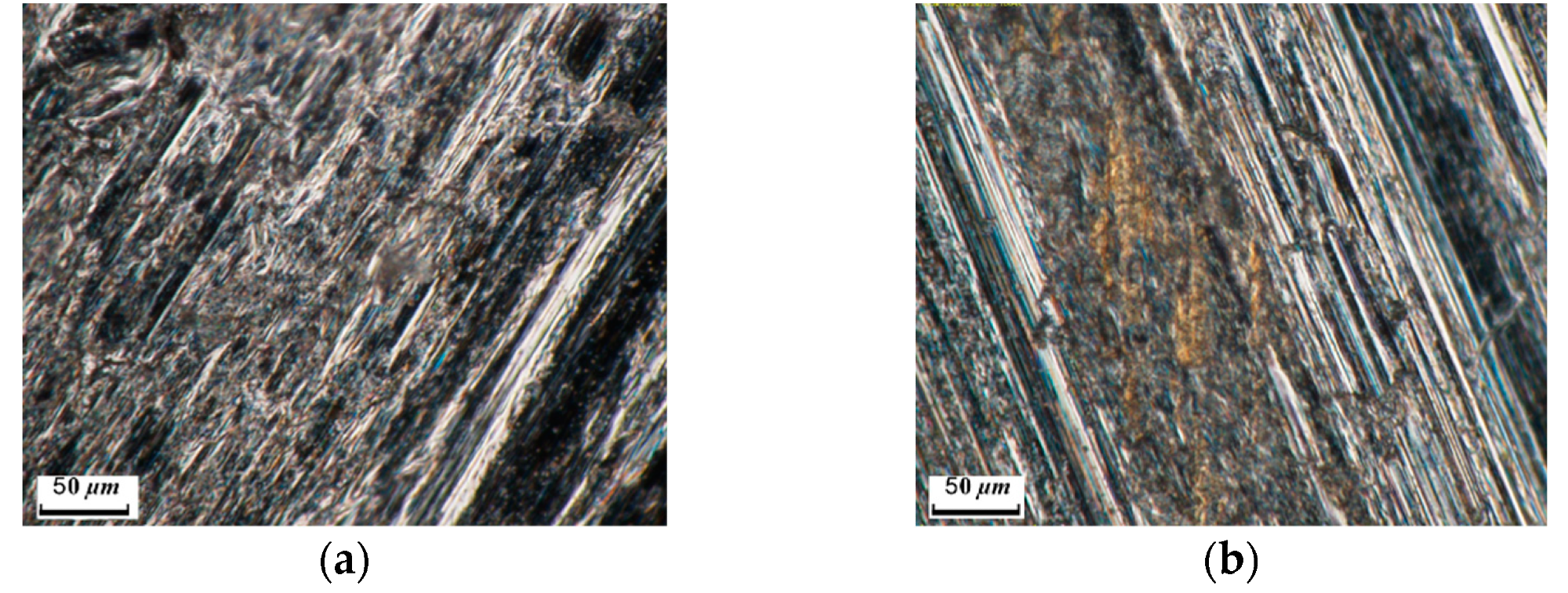
Wear tracks of the BT22 alloy: (a) untreated; (b) nitrided (light microscopy). Image Credit: Tisov, O et al., Metals
Future Scope of the Study
In this study, the surface microhardness and maximum hardness of the treated alloy were improved by gas nitriding during the heat treatment. Additionally, nitriding reduced the adhesion reactions between the counterparts and the treated sample. The fatigue wear was dominant in the nitride alloy.
Although the alpha case adversely impacts the mechanical performance of titanium, applying the nitriding process can reduce the COF and improve the wear resistance at the same time. Thus, nitriding during the aging method can be used to produce wear-tolerant alloys in a simple and cost-efficient manner without requiring any additional energy or time.
Disclaimer: The views expressed here are those of the author expressed in their private capacity and do not necessarily represent the views of AZoM.com Limited T/A AZoNetwork the owner and operator of this website. This disclaimer forms part of the Terms and conditions of use of this website.
Source:
Tisov, O., ٞepicka, M., Tsybrii, Y. et al. Duplex Aging and Gas Nitriding Process as a Method of Surface Modification of Titanium Alloys for Aircraft Applications. Metals 2022, 12, 100. https://www.mdpi.com/2075-4701/12/1/100/htm.