By Susha Cheriyedath, M.Sc.Reviewed by Skyla BailyJan 17 2022
According to recent research in the journal Materials, the mechanical and thermal properties of iron-rich Al-Si alloys are associated with the presence of a large amount of the iron-rich phase (-Al5FeSi), whose unfavorable physiology not only separates the matrix but also induces tensile stress and interface incompatibility with the Al matrix.
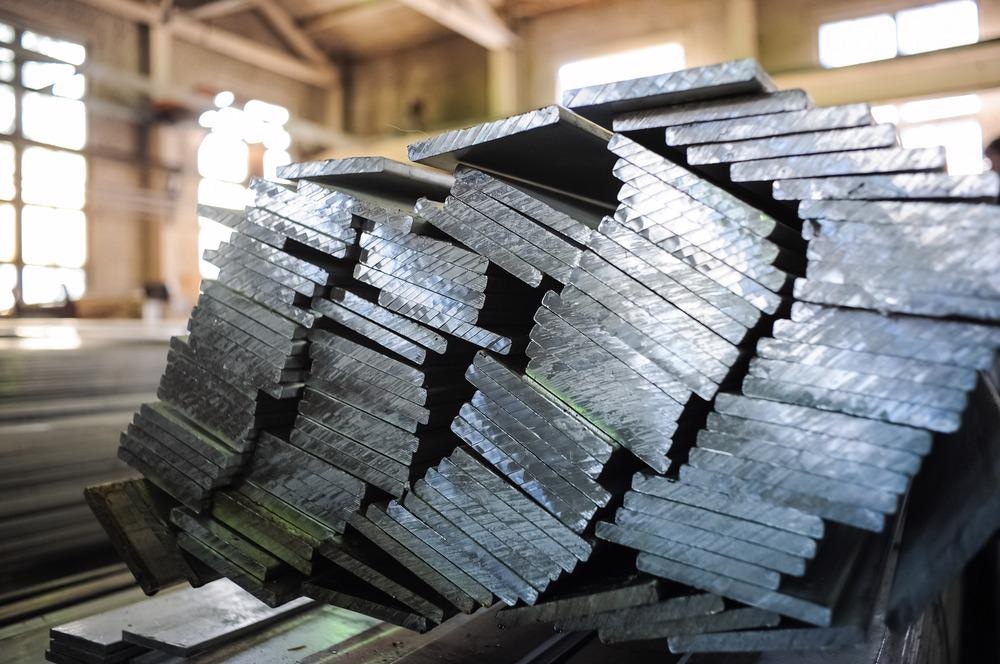
Study: Effect of Cooling Rate on the Microstructure Evolution and Mechanical Properties of Iron-Rich Al–Si Alloy. Image Credit: Yulia Grigoryeva/Shutterstock.com
Importance of Aluminum Alloys
Aluminum alloys are extremely flexible, strong, and dependable. As a result, they are in high demand in aerospace, architecture, and automobile industries, making them one of the most common metallic alloys, alongside steel.
Owing to the benefits of superior properties, high ease of processing, primarily anti-erosion, enhanced permeability, eco-friendliness, and reusability, alloys of aluminum are utilized in a wide range of battery-powered component wrapping, digital components, various automotive configurations, solar and wind power energy management as well as several daily items.
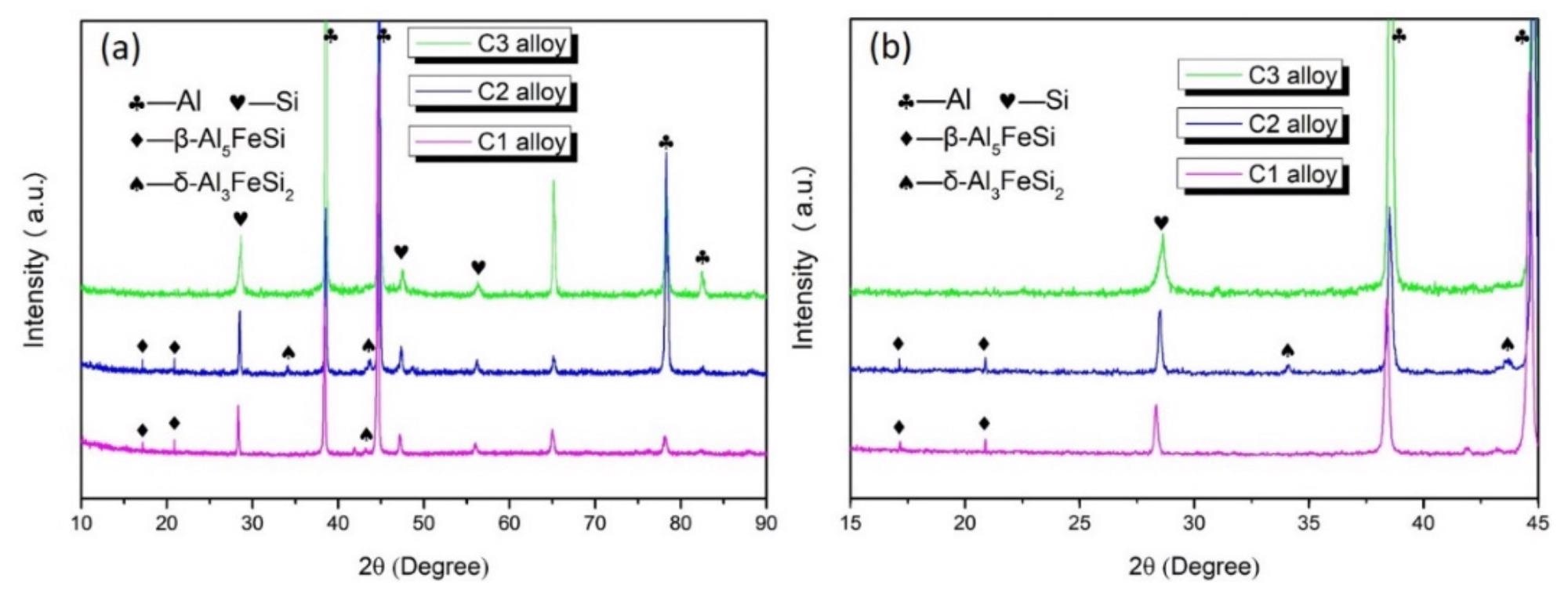
(a) XRD spectra of the C1, C2, and C3 alloys. (b) Shows the partially amplified spectra of (a). Image Credit: Shen et.al., Materials
Effect of Iron on Aluminum Alloys
The regeneration of scrap aluminum products yields recycled aluminum. The energy consumed during manufacturing is just 3% to 5% of the power consumed during basic aluminum manufacture.
This has clear benefits in terms of energy savings and pollution reduction, and as a result, it is now one of the research hotspots in the domain of ultralight composite parts. Iron is regarded to be the most dangerous contaminant component in reclaimed aluminum. The fundamental reason is that the solid solubility of iron in cast aluminum-silicon alloy is low (about 0.05 wt. percent), allowing for the formation of a range of iron-rich intermetallic phases during crystallization. On two-dimensional micrographs, β-Al5FeSi is long and needle-like, and the 3D space has a lath structure.
Intermetallic β-Al5FeSi Phase
The size and shape of the phase structure are the most important elements influencing the alloy's characteristics. The needle-like -Al5FeSi phase easily promotes tensile stress and matrix splitting, which is detrimental to the mechanical characteristics of aluminum.
Furthermore, high iron concentration severely impairs melting mobility and reduces castings performance. As a result, many scientists are striving to change the topology of -Al5FeSi phases, such as by introducing intermetallic compounds like Mn, Nb, Co, Sc, Er, and so on. Enhancing the melt superheat and heating process is an additional useful method for improving the structure of the iron-rich phase.
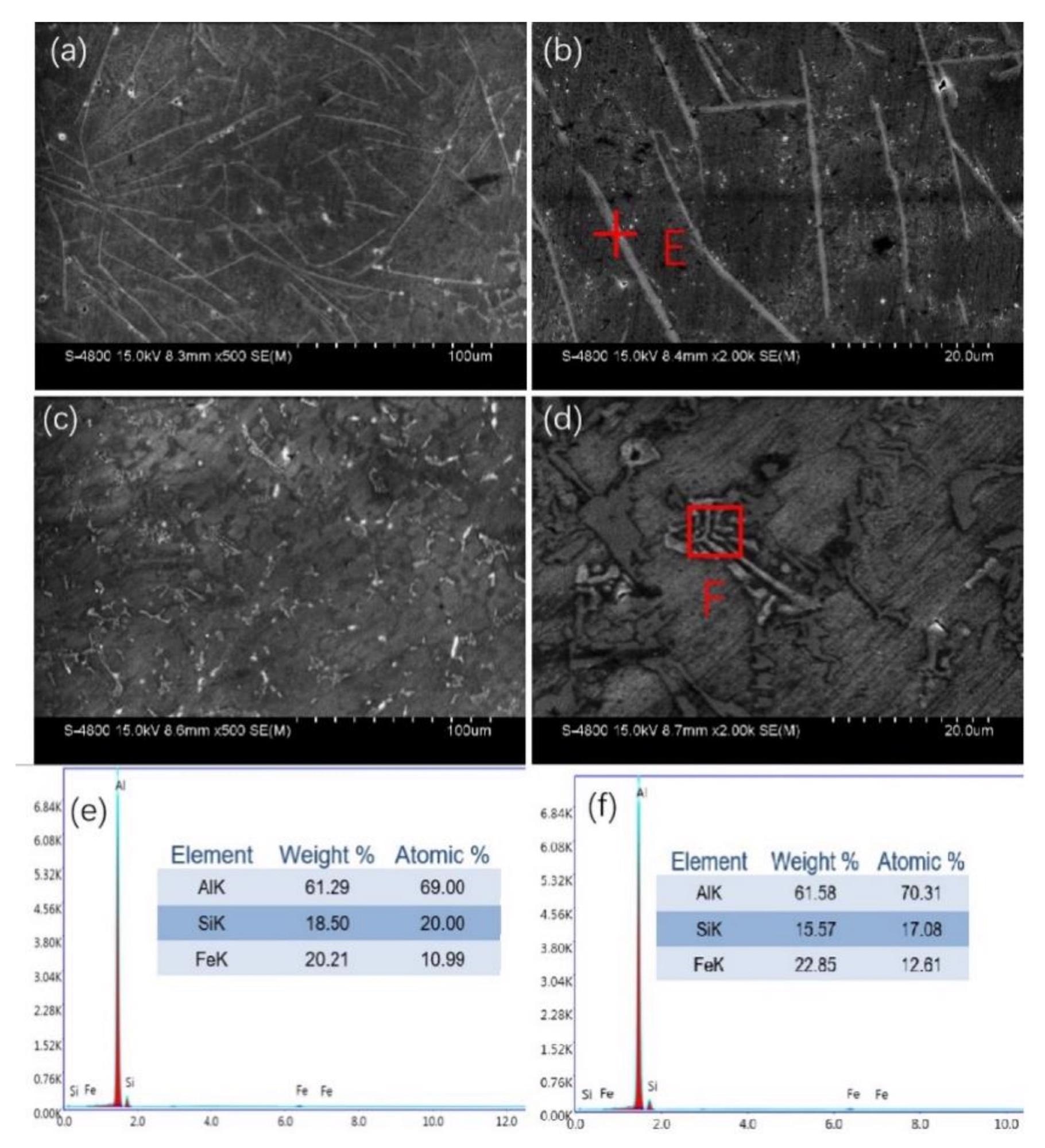
SEM images of the (a,b) C1 alloy and (c,d) C2 alloy. (e,f) are the EDS results of the (b,d) corresponding areas. Image Credit: Shen et.al., Materials
The inclusion of the aforesaid components simply modifies the shape of the iron-rich phase, introduces certain technical issues, and increases the risks of recovering secondary sources from Al-Si alloys. As a result, developing high-performance Al-Si alloys with a high Fe concentration is critical.
Does Cooling Rate Effect Alloys?
Varying the operating temperature is a powerful approach to alter the topology of microstructures. Because of its biochemical homogeneity and high solid absorption, melt spinning is a common quick crystallization procedure used in the manufacture of biostimulants.
Furthermore, the microstructure development of the Al-Si alloy has been observed to be reliant on the cooling rate and Fe concentration. Cooling rates in typical mold castings range from 1 to 10 K/s to 10 K/s–100 K/s in high-pressure die casting. It is necessary to investigate the microstructure under fast solidification conditions with cooling speeds of more than 103 K/s.
Research Findings
The Al-10Si-1.5Fe alloy studied in this study was made from as-cast ingots of commercialized alloys using three separate samples labeled C1, C2, and C3. The C1 alloy showed three sets of strong diffraction patterns at a cooling rate of 30 K/s, corresponding to the Al, Si, and β-Al5FeSi phases, respectively. The -Al3FeSi2 phase was visible in the C2 alloy when the chilling rate went up to 6.7 x 102 K/s. It is worth noting that the iron-rich phases vanished in the matrices when the cooling rate increased to 2.4 x104 K/s.
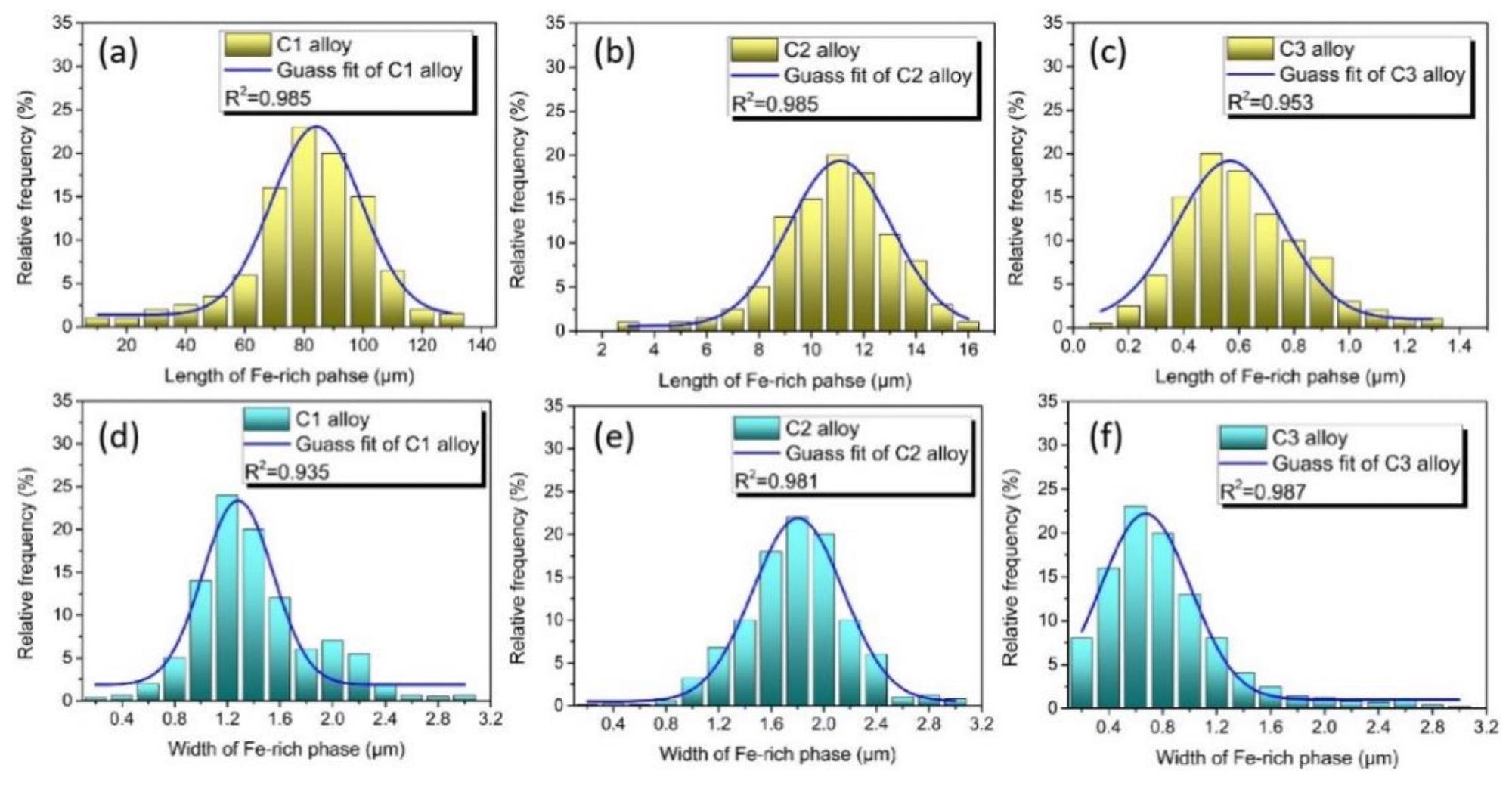
Statistical distribution of the length of Fe-rich phase of the (a) C1, (b) C2, and (c) C3 alloys, (d,e,f) are the statistical distribution of the width of Fe-rich phase of the C1, C2 and C3 alloys, respectively. Image Credit: Shen et al., Materials
Raising the cooling temperature not only modifies the morphology of the Fe-rich phase but also transforms the eutectic Si phases in the C2 alloy from rough acicular-like to fine particulate. The phases scattered in the C3 alloy substrate were more homogeneous and diffused when compared to the C1 and C2 alloys. The Fe-rich phase changed from a pointed long needle-like shape to a shorter rod-like morphology, with a more dispersed diffusion state and nearly no visible interweaving link.
Most importantly, when the cooling rates rose, the alloys' elongation at break improved dramatically. The tensile characteristics of the C2 alloy and the as-cast C1 alloy did not differ significantly. However, the mechanical characteristics of the C3 alloy with the fast-cooling rate are superior to those of the C1 and C2 alloys.
As the cooling rates rose higher, the ratio of the silicon phases decreased noticeably. Overall, the reinforcing process is thought to be connected with a modification in the geometry of the needle-like step process and a reduction in the ratio of the eutectic silicon phase.
In short, the cooling rate had a significant impact on the shape of the Fe-rich phase in Al-Si alloy. The spin coating technique converted sudden fracture of Fe-rich Al-Si alloy to a ductile failure, which is important for the recovery and recycling of Fe–rich Al-Si alloy and has significant industry potential uses.
Further Reading
Shen et. al. Effect of Cooling Rate on the Microstructure Evolution and Mechanical Properties of Iron-Rich Al–Si Alloy. Materials. 2022. 15(2). 411. Available at: https://www.mdpi.com/1996-1944/15/2/411
Disclaimer: The views expressed here are those of the author expressed in their private capacity and do not necessarily represent the views of AZoM.com Limited T/A AZoNetwork the owner and operator of this website. This disclaimer forms part of the Terms and conditions of use of this website.