Published in the journal Additive Manufacturing, a team demonstrates how a dynamic slicing algorithm for conformal additive manufacturing uses existing multi-directional slicing strategies without adding any additional computations into the process.
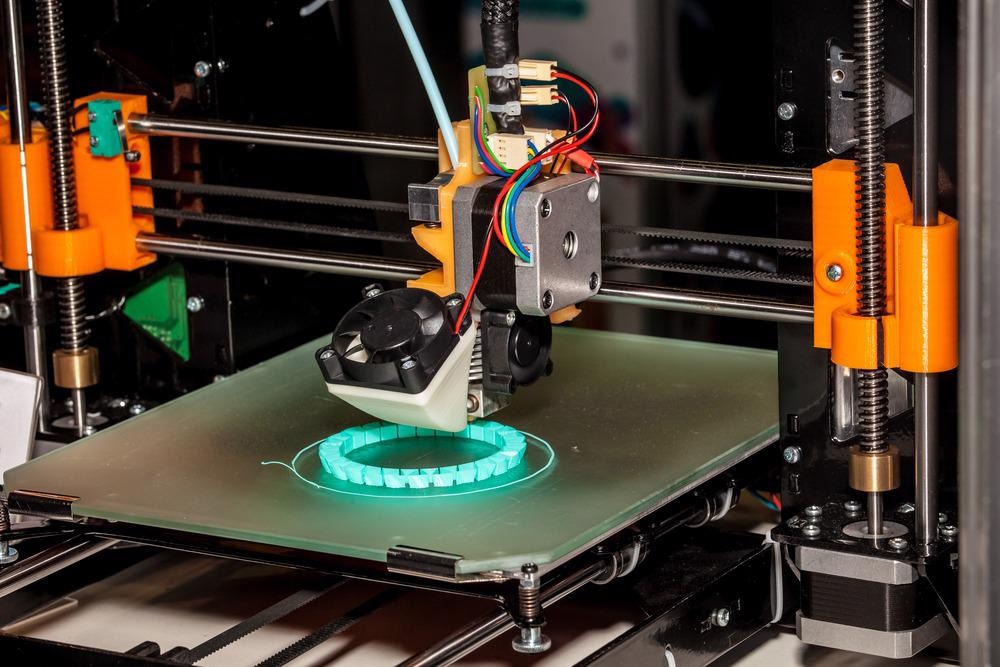
Study: A dynamic slicing algorithm for conformal additive manufacturing. Image Credit: Alexander Tolstykh/Shutterstock.com
In recent years, additive manufacturing (AM), a technique more commonly known as 3D printing, has become a crucial part of manufacturing. This is driven by the fact that AM is capable of fabricating extremely complex geometries which in today’s world offers manufacturers and developers maximum geometric design freedom.
One of the main challenges in AM is finding an algorithm with the capacity to slice 3D models with minimal support structures. A team of researchers at the School of Mechanical Engineering, Sichaun University, China have developed a new strategy for multi-directional slicing in AM.
Overcoming Limitations
Current uniform-directional slicing is limited by the need for the supporting architecture of any overhangs which typically results in material waste and poor surface finishes. In order to overcome these limitations efforts have been made to design non-supporting AM technologies.
It was reported that suspended geometries could be printed without supports by the robotic AM system. For non-supporting AM, the uniform-directional slicing algorithm is not applicable; thus, an effective multi-directional slicing algorithm is required for multi-directional deposition during non-supporting AM
Jie Wang, Corresponding Author, School of Mechanical Engineering, Sichaun University
Accordingly, the research focus has shifted from developing new uniform-direction slicing strategies to multi-directional slicing techniques. In order to do so, two primary approaches are considered: volume decomposition and skeleton extraction.
However, both of these approaches are limited by their own set constraints including computational complexity and limited precision on extractions of the models. Thus, Wang et al. proposed a dynamic multi-directional slicing algorithm for nonsupporting conformal additive manufacturing.
New Multi-Directional Strategy
The new strategy that was realized directly determined the slicing plane of each layer, and once the slicing plane was found slicing points were calculated. The idea of identifying the current slicing plane from the previous slicing point and the thickness is thus introduced.
Since the advanced multi-directional slicing algorithm is fundamentally different from existing multi-directional slicing algorithms the accuracy and effectiveness of the proposed slicing algorithm were elaborated.
The team set about conducting 3D printing comparison experiments: “The conformal 3D printing with proposed slicing algorithm is proved to be competent to reduce the staircase effect and fabricate the overhang structures without support materials,” states Wang.
In order to identify the optimal slicing plane of each layer, the geometric relationship between each slicing plane and the 3D model was used. The slicing contour was then acquired through the application of coordinate transformation according to the optimal slicing plane.
The team was able to demonstrate this through a series of slicing tests with models with the representative feature. The results demonstrated that the new multi-directional strategy was effective and had better accuracy than other pre-existing multi-directional methods.
The team also compared their results against uniform-directional 3D slicing methods and found that the new strategy did not produce the ‘staircase effect’ as rather produced a smooth surface without the need for additional support structures.
Next Steps
Effectively, the researchers were able to show that the new multi-directional strategy outperforms other slicing methods and provides solutions for downfacing overhang structures without the need for support materials.
So, while the team was able to demonstrate that their strategy was an improvement in comparison to pre-existing methods, concerns were raised that further research would be needed to improve the algorithm at the base of the strategy as difficulties may be encountered with multi-branch structures.
Therefore, the researchers call for an additional study that focuses on enhancing the “computational cost, exception handling, and algorithm extension” to improve the efficiency and accuracy of the new strategy.
The team remains confident that an effective multi-directional slicing approach for non-supporting conformal additive manufacturing (3D printing) can be developed and improve an ever-growing technology. In turn, this could usher in new potentialities and improve fabrication methods for the fabrication of extremely complex geometries in fields as varied as tissue engineering and electronic device manufacturing.
Reference
Jigang Huang, Qin Qin, Cheng Wen, Zhuoxi Chen, Kunlan Huang, Xia Fang and Jie Wang, A dynamic slicing algorithm for conformal additive manufacturing, Additive Manufacturing, (2021) https://www.sciencedirect.com/science/article/pii/S2214860422000306?via%3Dihub
Disclaimer: The views expressed here are those of the author expressed in their private capacity and do not necessarily represent the views of AZoM.com Limited T/A AZoNetwork the owner and operator of this website. This disclaimer forms part of the Terms and conditions of use of this website.