By Susha Cheriyedath, M.Sc.Reviewed by Skyla BailyFeb 4 2022
In a research paper posted to the Research Square preprint* server for future inclusion in The International Journal of Advanced Manufacturing Technology, scientists reported the preparation of different nanocomposites, namely Al-10Cu/2.5Al2O3, comprised of 2.5% alumina, 10% copper, and varying graphene (GN) weight ratios up to 1.5% by using a combination of powder metallurgy technique and hot rolling secondary process.
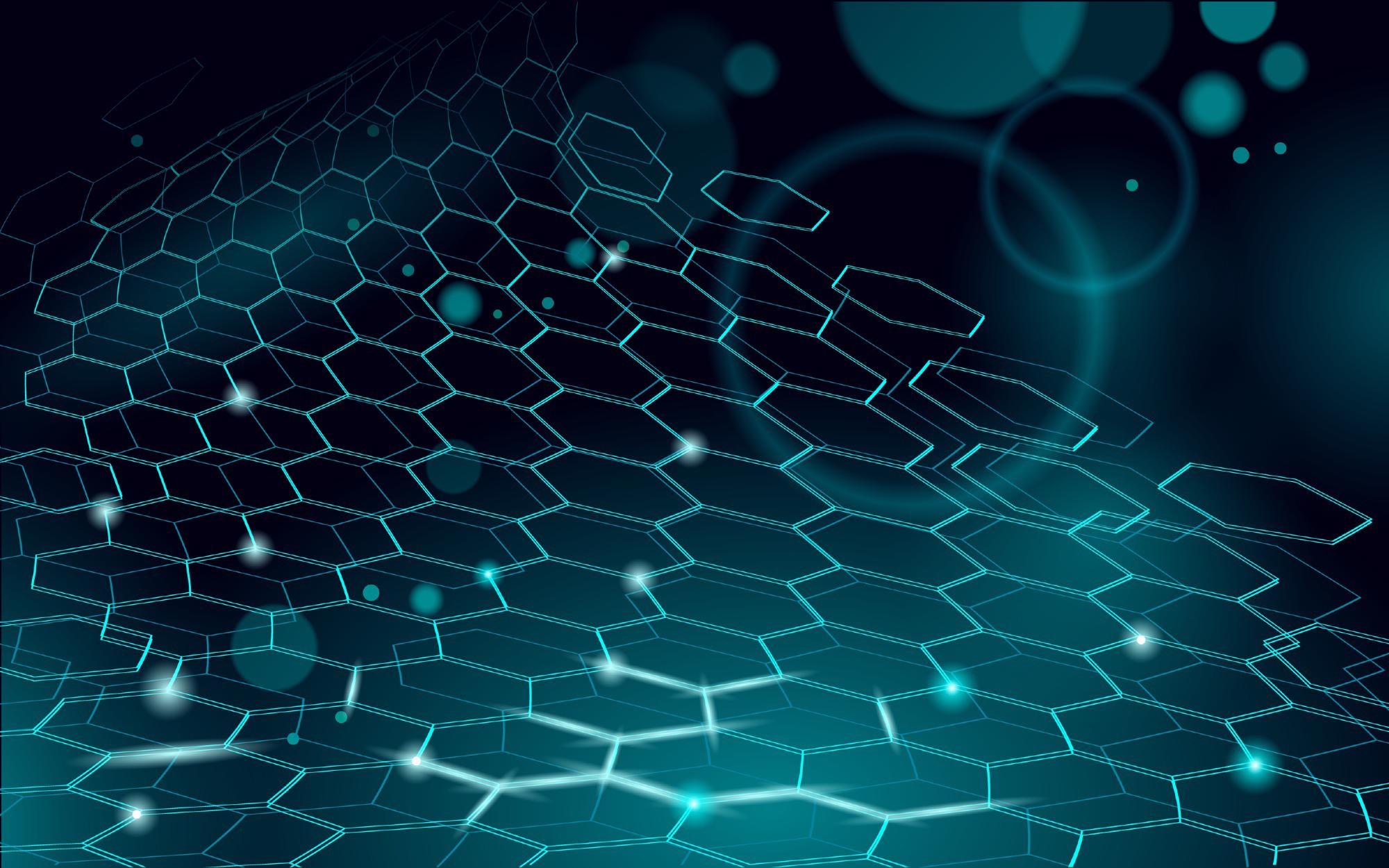
Study: Impact of Graphene and Hot-Rolling on the Microstructure and Mechanical Properties of Aluminum Matrix Nano-Composite. Image Credit: LuckyStep/Shutterstock.com
The researchers also evaluated the impact of graphene content on the structural and physicomechanical properties of these aluminum-based composites.
Background
The strength-to-weight ratio has become a significant material selection parameter in many industrial applications during the last few years. Because of its low density and high specific strength ratio, aluminum metal has become the preferred choice of designers.
However, its low mechanical characteristics, poor tribological qualities, and increased coefficient of thermal expansion limit its applications in industries. There are numerous reports present in the literature discussing the effect of graphene nano-sheets on the mechanical characteristics of aluminum matrix composites.

The sintering cycle curve of Al-Cu-Al2O3/Gr nano composites at 565 °C for 60 min. Image Credit: El-Bitar, T et al., Research Square
Powder metallurgy is known to be one of the finest methods for the production of suitable aluminum composites. However, the inclusion of nano-metric components for the enhancement of the physical and mechanical properties of aluminum composites remains a challenge.
This could be potentially achieved by using the metallurgical powder method in combination with secondary forming operations like hot rolling. However, there are sparse reports available in the literature on the effect of the hot rolling process on the behavior of graphene/metal composites deposited using the powder metallurgy method.
About the Study
In the present study, researchers synthesized six aluminum-based powder samples, including pure aluminum, Al/10%Cu, Al-10%Cu/2.5%Al2O3, and Al-10%Cu-2.5Al2O3/GNs (0.5, 1, and 1.5 wt%) using the powder metallurgy method followed by a secondary procedure of hot rolling.
Mechanical alloy milling was used to mix the components for 45 hours by utilizing a ball to powder ratio of 10:1 and 12 mm balls in the presence of 5% hexane as protocatechuic acid. Following that, the samples were pressed at 600 MPa and subjected to heating at 565°C for 1 hour in a vacuum oven. The heating speeds ranged from 2 to 4 °C/min.
Subsequently, the chemical composition, hardness, relative density, mechanical wear rate, compressive strength, electrical conductivity, morphological and microstructural properties of the sintered as well as rolled aluminum nanocomposites were investigated using various experimental methods.
The effects of alumina, copper and varying graphene ratios on the chemical, physical, and mechanical characteristics of the as-fabricated aluminum-based nanocomposites were also demonstrated.
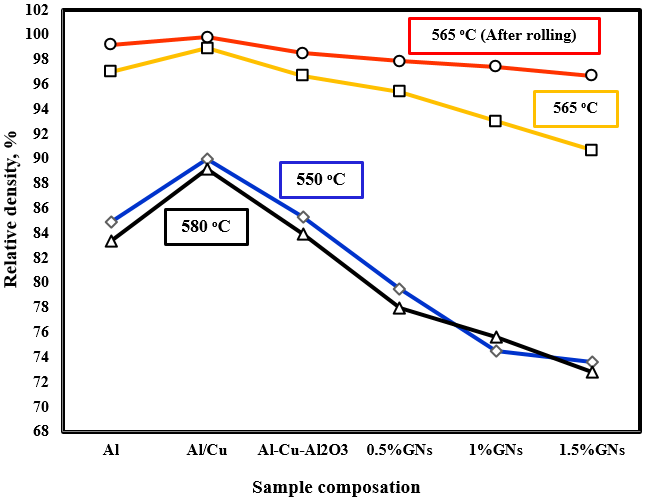
The relative density of the powder metallurgy and hot rolled samples. Image Credit: El-Bitar, T et al., Research Square
Observations
In this study, the ideal manufacturing conditions for the powder metallurgy method were observed to be 565°C and 600 MPa for 1 hour. Microstructures of the aluminum nanocomposite samples synthesized by the powder metallurgy technique demonstrated a decent distribution of components with a few graphene layer accumulations.
However, microstructures of the samples fabricated by the rolling process revealed a uniform distribution of all the elements, with no accumulations of graphene flakes, no pores, and effective amalgamation with the Al base metal as well as other components.
No foreign elements were discovered in the X-ray crystallographic study, which indicated the development of CuAl2 intermetallic between copper and aluminum. No evidence of any interactions between graphene and aluminum for the creation of the Al4C3 aluminum carbide compound was established.
The rolling procedure facilitated the removal of graphene flake accumulations, which resulted in the elimination of internal pores among these layers. This led to an improvement in the samples' relative density. The hardness of powder metallurgy-produced aluminum samples was increased by the addition of alumina, copper, and graphene up to 1%. However, it decreased at 1.5% graphene. T
he hardness degradation in the sample with 1.5% graphene improved by 78.4% after the rolling procedure, which was attributed to the removal of any internal pores or accumulations. Due to refining of the particles and eradication of the defects in the samples deposited by the powder metallurgy technique, the stiffness and compressive strength of the aluminum samples increased after the addition of alumina, copper, and graphene after the rolling procedure.
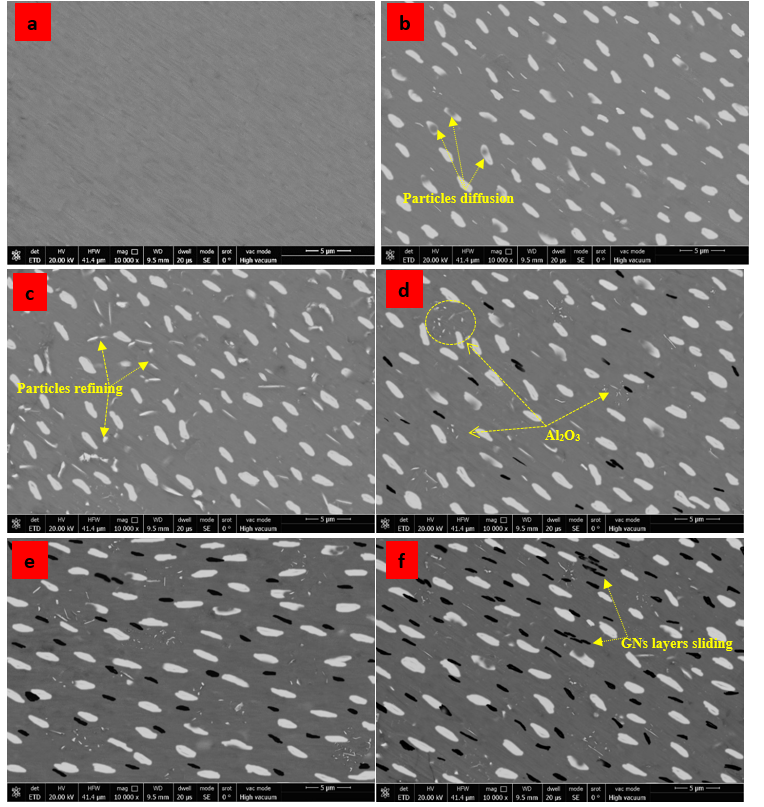
The microstructure of rolled samples. Image Credit: El-Bitar, T et al., Research Square
Conclusions
In conclusion, this study examined the impact of different graphene ratios, alumina, and copper on the physical and mechanical properties of various aluminum nanocomposites synthesized by powder metallurgy and hot rolling methods. The powder metallurgy method was used to determine suitable temperature, pressure, and sintering time for the manufacturing process.
The aluminum nanocomposite samples fabricated by the powder metallurgy technique demonstrated a general improvement in the physicomechanical and microstructure characteristics up to a 1% graphene ratio. However, the outcomes were unfavorable at 1.5% graphene, which was attributed to the existence of graphene accumulations. The adverse results associated with 1.5% graphene improved when the hot rolling procedure was used after the powder metallurgy method. In general, both before and after the hot rolling process, the microstructure was found to be optimum.
*Important Notice
Research Square publishes preliminary scientific reports that are not peer-reviewed and, therefore, should not be regarded as conclusive, guide clinical practice/health-related behavior, or treated as established information.
Disclaimer: The views expressed here are those of the author expressed in their private capacity and do not necessarily represent the views of AZoM.com Limited T/A AZoNetwork the owner and operator of this website. This disclaimer forms part of the Terms and conditions of use of this website.
Source:
El-Bitar, T., Nouh, F., El-Kady, O. A. et al. Impact of Graphene and Hot-Rolling on the Microstructure and Mechanical Properties of Aluminum Matrix Nano-Composite. The International Journal of Advanced Manufacturing Technology (2022). https://www.researchsquare.com/article/rs-1258597/v1