Reducing the carbon footprint of the industry is a key concern in the 21st century, and replacing the fossil fuels used for energy in iron and steelmaking with renewable fuels is a current focus of research. A new study published in the Journal of Cleaner Production has investigated how hydrogen can help reduce emissions.
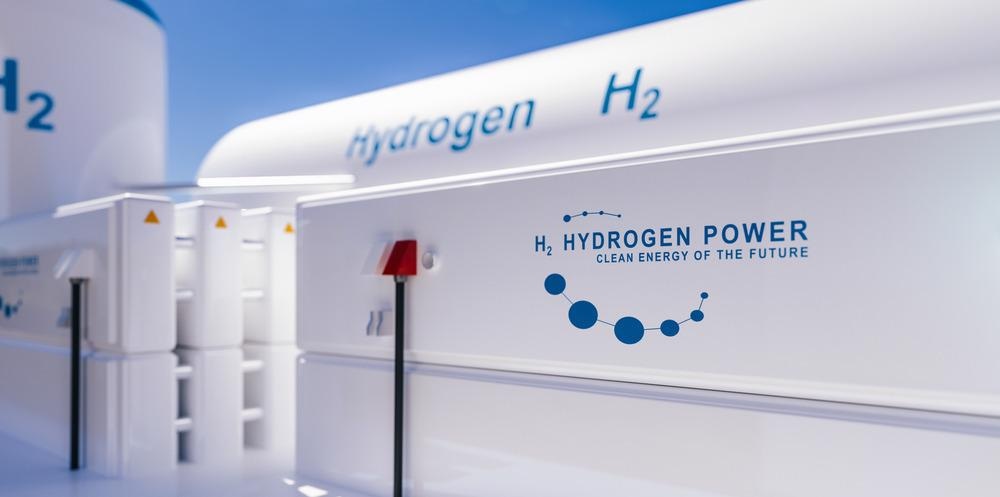
Study: Green steel at its crossroads: Hybrid hydrogen-based reduction of iron ores. Image Credit: Audio und werbung/Shutterstock.com
A Green Future for the Iron and Steelmaking Industry?
Human activity has been well documented as a cause of climate change. With the increasing frequency of extreme weather events, rising global sea levels, acidification of marine environments, environmental destruction, loss of biodiversity and the real possibility of economic and social impacts on human society, a more sustainable future needs to be realized.
Iron and steel have literally built the modern world. These important materials are utilized widely in industries such as construction for their superior mechanical properties, but their manufacture comes at a price: the global iron and steelmaking industry accounts for 7% of all global carbon emissions, with 1.9 tons of CO2 emitted per ton of produced steel.
Overwhelmingly, the industry relies on fossil fuels to provide the energy required for manufacturing. If the industry follows a business-as-usual model, this figure is predicted to massively increase over the coming decades.
Replacing carbon with renewable energy sources for the manufacturing process is, therefore, key to reducing carbon dioxide emissions of the industry and curtailing the impact of this commercially important activity on climate change. The industry is at a crossroads.
Hydrogen has been widely touted as a potential energy source to replace carbon-emitting fossil fuels as the by-product of using hydrogen is water, compared to CO2. Whilst the majority of hydrogen currently produced is “grey hydrogen” which is obtained from natural gas, the opportunities presented by “green hydrogen,” which is produced by renewable sources, confer significant advantages for achieving true sustainability and eco-friendliness within the iron and steelmaking industries.
Current Challenges with the Move to Green Hydrogen Within the Industry
However, there is a significant challenge associated with replacing fossil fuels with green hydrogen as the reducing agent in the iron and steelmaking industries. Demand for crude steel worldwide is around 1.8 billion tons, with rapidly increasing urbanization and industrialization likely to increase this demand still further over the coming decades.
To meet this demand and completely phase out fossil fuels in the production of iron and steel would require a stoichiometric amount in excess of ~97 million tons of green hydrogen annually. This presents a bottleneck for the production of green hydrogen in the sector for at least the next two decades. Current and near-term global production of green hydrogen, which is also utilized for multiple other industrial activities such as power generation, will struggle to satisfy the demands of the industry.
Proposed Technological Approaches
Currently, most iron and steel are produced using carbon-intensive blast furnaces and basic oxygen furnaces. There are three main proposed technological approaches to utilizing hydrogen as a reducing agent in iron and steel manufacture: using hydrogen directly in current blast furnaces to replace part of the coke, direct reduction (DR) in fluidized bed reactors or shaft furnaces, where iron ore is exposed to gases containing hydrogen, and hydrogen-based reduction (HPR) which simultaneously melts and reduces ores.
More from AZoM: Laser Diffraction Particle Size Analysis of Cement
The Study
Writing in the Journal of Cleaner Production, the authors have presented a hybrid process where hematite pellets are partially reduced to 38% global reduction at 700 oC using DR and then transferred into an HPR process to achieve full reduction into liquid iron. A lean gas mixture of Ar-10%H2 was used in the process in an arc-melting furnace.
This hybrid production process takes advantage of both technologies’ characteristics and favorable kinetic regimes and reduces hydrogen and energy consumption, improving sustainability. Additionally, by limiting overexposure to plasma energy, process stability and furnace longevity are improved.
When processing partially reduced iron oxides rather than hematite, the arc plasma proceeds much more efficiently. Results indicated that the residence time in DR furnaces could be reduced as semi-reduced oxides rather than sponge iron are the products. Additionally, the results of the research demonstrated that reducing iron pellets in this hybrid process consumed six times less hydrogen than in a pure lab-scale direct reduction route at 700 oC.
The authors behind the study have stated that more compact, correspondingly adjusted reactors could be used for the purpose of reducing iron with hydrogen, and the reduced amount of costly hydrogen gas that is needed during the process can reduce efforts, cost, and energy.
The aim of the study is to provide sound scientific foundations that enable improved decision-making that will enable a more sustainable ironworking industry to avoid energy expenses associated with unnecessary hydrogen gas recirculation in plasma reactors and blast furnaces whilst producing pure iron at competitive conversion rates.
Further Reading
Souza Filho, I.R. et al. (2022) Green steel at its crossroads: Hybrid hydrogen-based reduction of iron ores [online] Journal of Cleaner Production 340 130805 | sciencedirect.com. Available at: https://www.sciencedirect.com/science/article/abs/pii/S0959652622004437
Disclaimer: The views expressed here are those of the author expressed in their private capacity and do not necessarily represent the views of AZoM.com Limited T/A AZoNetwork the owner and operator of this website. This disclaimer forms part of the Terms and conditions of use of this website.