In a recent study published in the journal Additive Manufacturing, researchers from the USA conducted a detailed review on three-dimensional (3D) printing of optical devices.
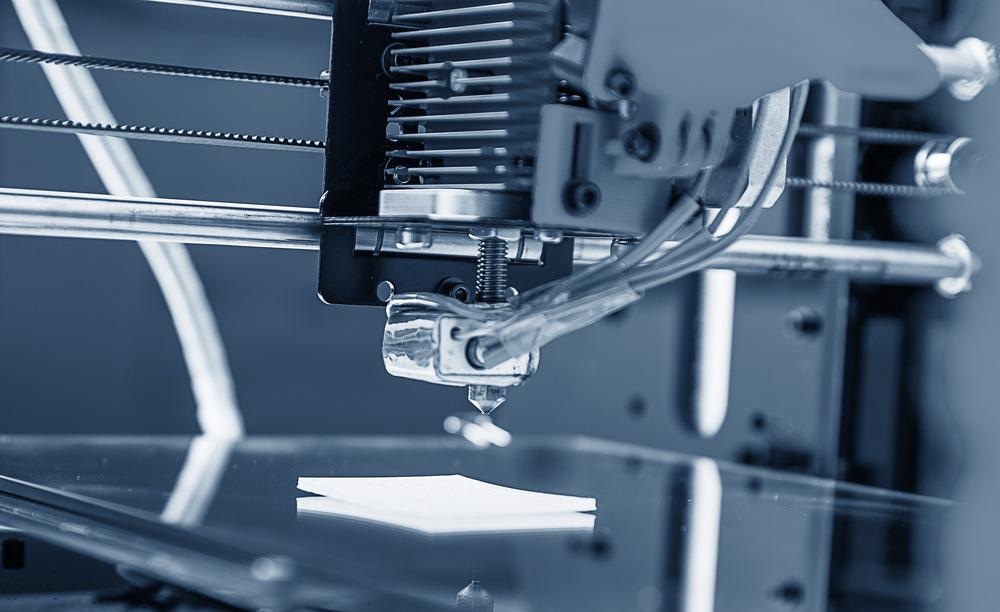
Study: Recent Advancements and Applications in 3D Printing of Functional Optics. Image Credit: Alex_Traksel/Shutterstock.com
Recent developments in optical science have led to various optical devices with unique functionality. As optical devices are used in modern technologies, the recent research and development trend is to develop advanced optical instruments. However, due to the structural complexity and multi-material distribution of advanced optical devices, it is challenging to manufacture them using traditional manufacturing techniques. Moreover, this limitation in manufacturing restricts the advancement of functional optics at a commercial scale.
Additive manufacturing (AM), or 3D printing, has demonstrated its ability to produce multi-scale, multi-material, and multi-functional optical devices with improved sensing, imaging, and light modulation performance.
In the present study, advances in AM of functional optics were discussed in detail. The study focused on optical devices such as optoelectronics, lenses, metamaterials, and photonics. The researchers also investigated material selection, design scenarios, 3D printing strategies, and property evaluation of the 3D printed optics.
3D Printing of Different Functional Optics
In photoelectronics, photons manipulate the signals sent by electronic devices. 3D printing has significant potential in the field of photonics fabrication. It can develop crystal color patterns, structural colors, and display fiber, which is difficult to create using traditional manufacturing. The main advantage of 3D printing photoelectronic is that the devices' critical shapes can be developed easily and manufactured using a variety of materials.
3D printing can also be used to develop optical lenses at different scales such as nanoscale, microscale, macroscale, and multi-scale. 3D printing can reduce the limitation of traditional lens manufacturing technologies and provide higher fabrication quality and resolution. However, some challenges to 3D printed optical lenses include surface quality, time, and material selection.
Optoelectronics are types of electronic devices that can transmit, emit, and detect different forms of radiation. 3D printing can be used to develop optoelectronics such as light-emitting diodes (LEDs), solar cells, and waveguides. Additionally, 3D printing allows optoelectronics to be customized, which is critical for increasing efficiency, but manufacturing them with 3D printing is a technological challenge.
Materials with novel artificial structures made up of subwavelength units are known as optical metamaterials. 3D printing can manufacture optical metamaterials such as optical laser, cloak, modulation, and optical field modulation. The use of 3D printing technology in manufacturing complex structures of optical metamaterials is also a recent trend.
More from AZoM: How Can AI Overcome 3D Printing Defects?
The high processing precision of 3D printing is beneficial to the design of metamaterial microstructures. Additionally, the action frequency band of the material can be improved using this technology. However, 3D printing of optical metamaterials has challenges related to synchronous manufacturing.
Advantages and Limitation
The main advantages of 3D printing in optical devices are large-area manufacturing, high resolution, less material consumption, and high fabrication speed. Additionally, using computer modeling with 3D printing reduces the cost of optics manufacturing. Moreover, 3D printing can be used to develop any shape surface, which improves the capability of optical device development.
The major limitation in developing 3D printing of functional optics is the variation in material properties that are generated during the 3D printing process. For example, in 3D printed optical lenses, obtaining accurate material transparency is challenging.
Moreover, most 3D printing processes were designed for rapid prototyping, and mass production is challenging. Another major stumbling block is that 3D printing was designed with single-material fabrication and commercial 3D printers find it challenging to fabricate using multi-materials, which affects optical component functionality. Moreover, significant research is yet to be done in developing 3D printing technologies of optical devices based on new principles.
Conclusions
The advancement of 3D printing as a manufacturing method will significantly improve advanced optical device applications. Moreover, it is reasonable to expect an increase in the number of AM applications in the fabrication of optical devices. Furthermore, functional components such as lenses, light-emitting diodes (LEDs), waveguides, and photonics will add new possibilities for developing advanced optical devices for various applications in biomedical engineering, computational imaging, aerospace, energy harvesting, and camouflage.
A tradeoff between efficiency and resolution in the fabrication process of optical devices is a significant achievement in the 3D printing of optical devices. The applications of 3D printing in beam splitting, structural color, art, combiner circuits, and light manipulation for display have yet to be investigated in detail for industrial applications. Further, the scope of 3D printing optical devices can be extended from visible light to microwave band by optimizing the structure design and improving fabrication accuracy.
Disclaimer: The views expressed here are those of the author expressed in their private capacity and do not necessarily represent the views of AZoM.com Limited T/A AZoNetwork the owner and operator of this website. This disclaimer forms part of the Terms and conditions of use of this website.
Source:
Yizhen Zhu, Tengteng Tang, Suyi Zhao, Dylan Joralmon, Zachary Poit, Bhushan Ahire, Sanjay Keshav, Aaditya Rajendra Raje, Joshua Blair, Zilong Zhang, Xiangjia Li, Recent Advancements and Applications in 3D Printing of Functional Optics, Additive Manufacturing,2022,102682, ISSN 2214-8604, https://www.sciencedirect.com/science/article/pii/S2214860422000872?via%3Dihub