In a recent study published in the open-access journal Materials, researchers compared the mechanical properties between computational and experimental models of honeycomb lattice structures of polymer and metals.
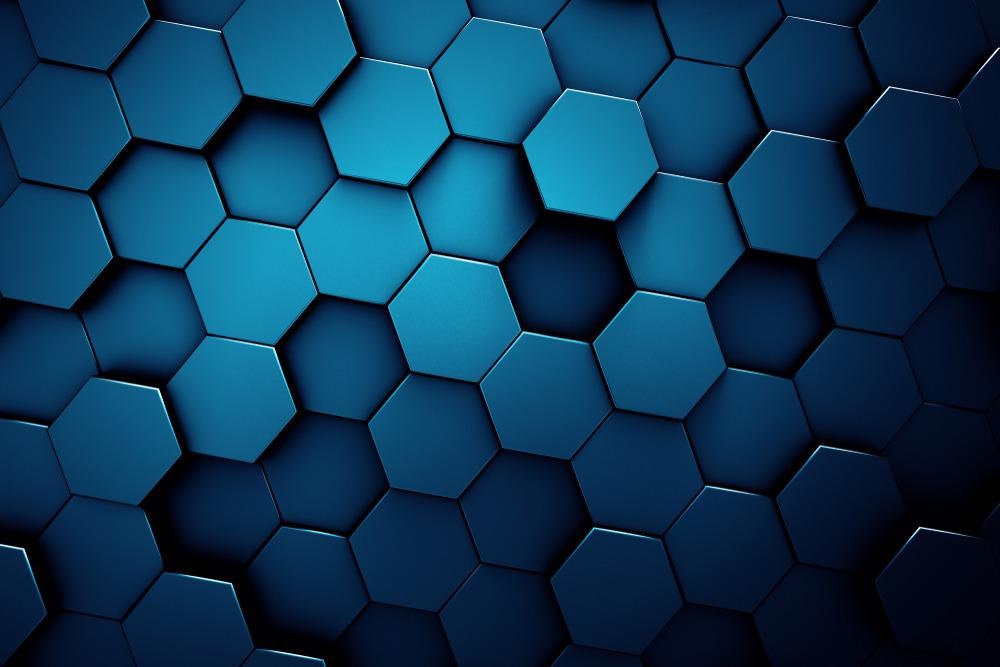
Study: Additive Manufacturing of Honeycomb Lattice Structure—From Theoretical Models to Polymer and Metal Products. Image Credit: BokehStore/Shutterstock.com
The honeycomb structure of Stratasys Vero PureWhite polymer was fabricated using PolyJet technology and that of stainless steel 316L and titanium alloy Ti6Al4V was achieved by laser powder bed fusion. The finite element model (FEM) accurately predicted the stiffness of the metal structure but overestimated the stiffness of the polymer structure.
Background
Additive manufacturing (AM) can produce structures with intricate design and tunable mechanical, thermal, electrical, and acoustic properties. However, unlike subtractive manufacturing (SM), the properties of the finished structure are difficult to predict.
In SM, the properties of the final product and the initial workpiece are almost the same, but in AM, a subtle variation in the operating temperature, deposition rate, and environmental conditions can significantly deviate the properties of the finished structure from its intended goal.
![Dimensions of the hexagonal honeycombs [14]. A unit cell of material is highlighted.](https://www.azom.com/images/news/ImageForNews_58416_16463008363576275.jpg)
Dimensions of the hexagonal honeycombs. A unit cell of material is highlighted. Image Credit: Goldmann, T et al., Materials
Furthermore, the prediction of optimal processing parameters and state of material during AM is crucial to minimize intrinsic manufacturing imperfections, defects, and reduce the number of required prototypes. Computer-aided design (CAD) has been a versatile tool to predict the mechanical properties of structures made by SM. The availability of initial material properties, process parameters, and environmental factors are enough to anticipate the properties of the finished structure in SM. However, it faces substantial challenges when it comes to AM.
Each type of material, viz. ceramics, polymers, and metals, and their properties have a different correlation with the processing parameters in AM. Thus, AM requires a detailed study of the difference between the properties of CAD and experimental models based on the type of material.
About the Study
In this study, researchers fabricated hexagonal honeycomb lattice structures of a polymer and two metals and compared the mechanical properties of their FEM and experimental models. Stratasys Vero PureWhite RGD837 acrylic-based photopolymer was fabricated by the PolyJet method with a layer thickness of 27 µm and a resolution of 600 dpi.
The stainless steel 316L and titanium alloy Ti6Al4V were fabricated by laser powder bed fusion method using an ‘M2 cusing’ 3D printer. The sizes of the particles ranged from 20 to 50 µm. The laser beam had a power of 200 W with a scan speed of 0.5 m/s, a layer thickness of 20 µm, and an operating temperature of 840 °C.
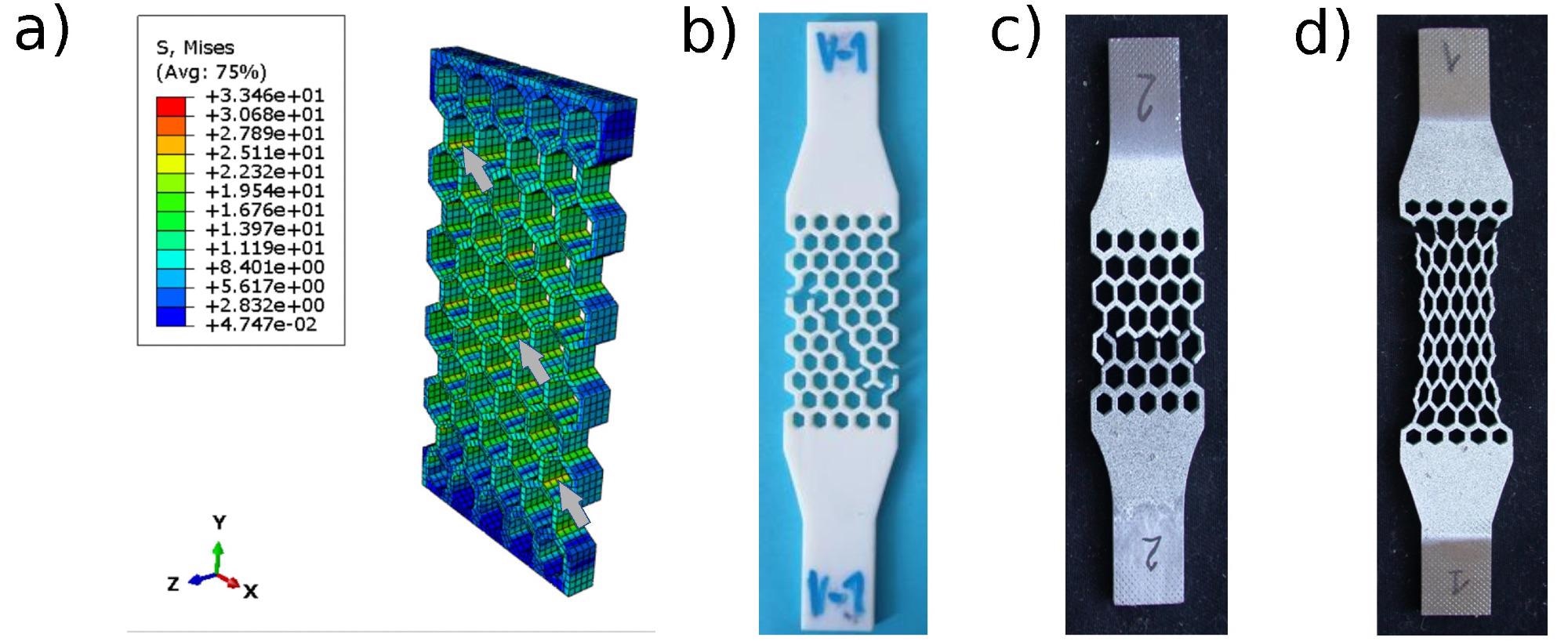
(a) von Mises stress distribution for Stratasys Vero PureWhite specimen loaded by the axial tensile force of 200 N. Value of stress is expressed in MPa. Values of stress are expressed in MPa. Maximum stress is identified at connecting nodes of individual honeycomb cells. Few nodes with stress concentration are marked by arrows. Experimental specimens from Stratasys Vero White polymer (b), titanium alloy Ti6Al4V (c) and stainless steel 316L (d) show fractures at connecting modes. Image Credit: Goldmann, T et al., Materials
FEMs of the honeycomb structures were constructed and meshed using ABAQUS/CAE software and analyzed with an equivalent elastic material model. This gave the effective Young’s modulus (E*) and Poisson’s ratio (ν). A 3D scanner was used to measure the dimension of the honeycomb structures. Finally, for experimental data, an electromechanical testing system was used for uniaxial tests at a constant strain rate of 0.04 s at room temperature.
Observations
Stratasys Vero PureWhite polymer exhibited the lowest stiffness among all samples. Ti6Al4V alloy exhibited the lowest extensibility with an average elongation at break of 3.5 ± 0.3%, whereas stainless steel samples exhibited the highest plastic deformation with an average elongation at break of 25.2 ± 0.2%.
Each sample showed maximum stress concentration at the nodes of honeycomb cells; therefore, most of the cracks were generated at these points after the loading test. Scanning electron microscope (SEM) images revealed that both metal samples had a ductile transcrystalline fracture.
Experimentally obtained E* of the polymer, Ti6Al4V alloy, and stainless steel had z-test values of (z = −144.2, p < 0.001), (z = −4.7, p < 0.001), and (z = −2.37, p = 0.018), respectively. E* values obtained from FEM analysis for the same samples had z-test values of (z = −122.16, p < 0.001), (z = 0.02, p = 0.98), and (z = 0.003, p = 0.99), respectively. This showed that both metal alloys had very similar E* values for experimental model and FEM, whereas the Stratasys Vero PureWhite polymer had a huge difference between experimental and FEM values of E*.
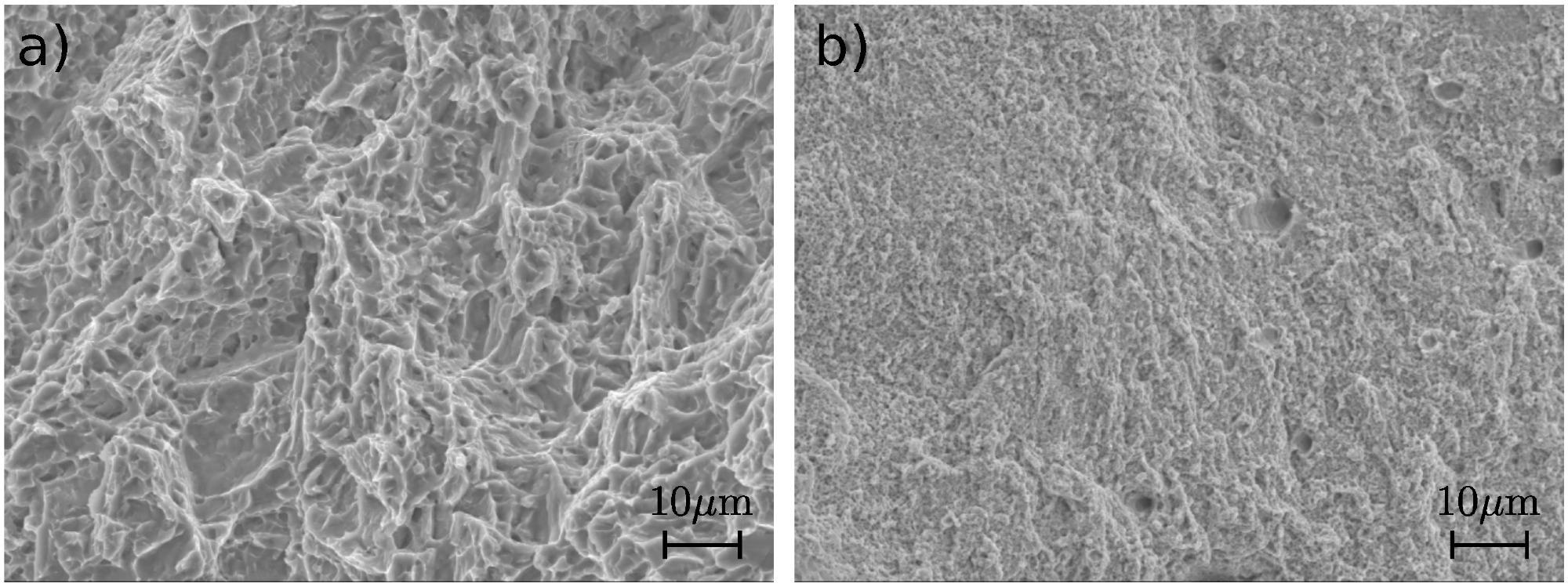
Micrographs of fracture surfaces of the specimens after tensile test made of (a) titanium alloy Ti6Al4V and (b) stainless steel 316L. Image Credit: Goldmann, T et al., Materials
Conclusions
To conclude, researchers of this study analyzed the difference in stiffness, i.e., E* of Stratasys Vero PureWhite polymer, Ti6Al4V alloy, and stainless steel 316L honeycomb structures obtained from the experimental model and FEM. FEM overestimated the value of E* for the polymer, whereas it was a close approximation for both metal alloys.
This shows FEM is a suitable tool for predicting mechanical properties of 3D-printed metals and alloy structures. However, it can be used only for the first-order approximation of the mechanical properties of polymer structures.
Disclaimer: The views expressed here are those of the author expressed in their private capacity and do not necessarily represent the views of AZoM.com Limited T/A AZoNetwork the owner and operator of this website. This disclaimer forms part of the Terms and conditions of use of this website.
Source:
Goldmann, T., Huang, W., Rzepa, S., Džugan, J., Sedláček, R., Daniel, M., Additive Manufacturing of Honeycomb Lattice Structure—From Theoretical Models to Polymer and Metal Products. Materials 2022, 15, 1838. https://www.mdpi.com/1996-1944/15/5/1838