In a recent study published in the journal Polymers, researchers from China demonstrated a new method to recycle the waste produced by the rubber industry.
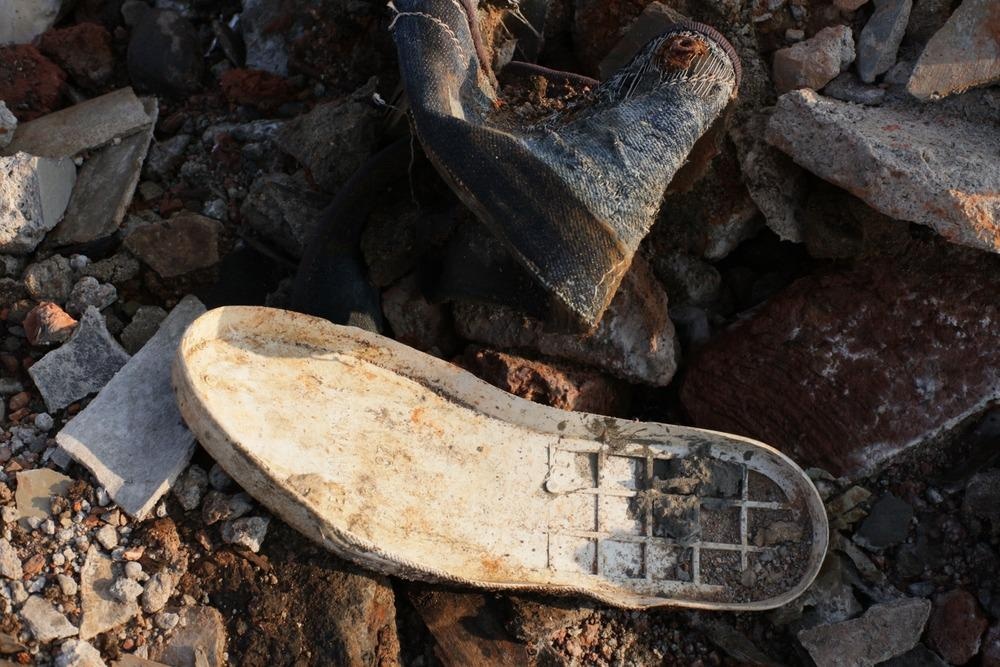
Study: Selective Decomposition of Waste Rubber from the Shoe Industry by the Combination of Thermal Process and Mechanical Grinding. Image Credit: cornerstock/Shutterstock.com
Rubber Industry and Waste
The rubber sector contributes significantly to the global economy, and rubber output from the footwear and tire industries increases each year. The substantial quantity of trash produced during the manufacturing process of rubber is one of the critical environmental issues faced by the rubber industry.
Due to this, waste rubber disposal remains an economic, social, and ecological challenge worldwide. The inappropriate disposal of waste rubber leads to a considerable volume of garbage being burnt which causes air pollution. Additionally, rubber waste also increases the danger of disease transmission and reduces sustainability.
In the present study, the waste rubber (WR) from the shoe industry was crushed and recovered using a torque rheometer, and the effects of varied filling rates and grinding temperatures on the structure of WR were analyzed.
Torque (M) of the WR samples as a function of the grinding time at different temperature. Image Credit: Xiao, Q et al., Polymers
Methodology
The materials used for the study were WR, xylene and tetrahydrofuran (THF), analytical reagents, and styrene-butadiene rubber. The main ingredients of the rubber were carbon black (CB), stearic acid, zinc oxide, and sulfur.
Initially, the WR was washed and dried before being crushed into particles in a crusher to prepare the samples. Further, the WR was ground in a torque rheometer with two roller rotors at various temperatures and filling rates. During the crushing process, the rotor speed was set to 40 revolutions per minute, and the grinding duration was set to 10 minutes.
Additionally, the rheological torque of the samples was continually measured at varying temperatures and filling rates. Overall, reclaimed waste rubber (RWR) and styrene-butadiene rubber (SBR) were mixed in different formulations to produce six samples.
The Fourier transform infrared spectroscopy (FTIR), laser particle size analyzer, sol-fraction analysis, gel permeation chromatography (GPC), differential scanning calorimeter (DSC), and scanning electron microscope (SEM) were used by researchers to investigate the structure evolution, particle size distribution, and morphology of recycled rubber.
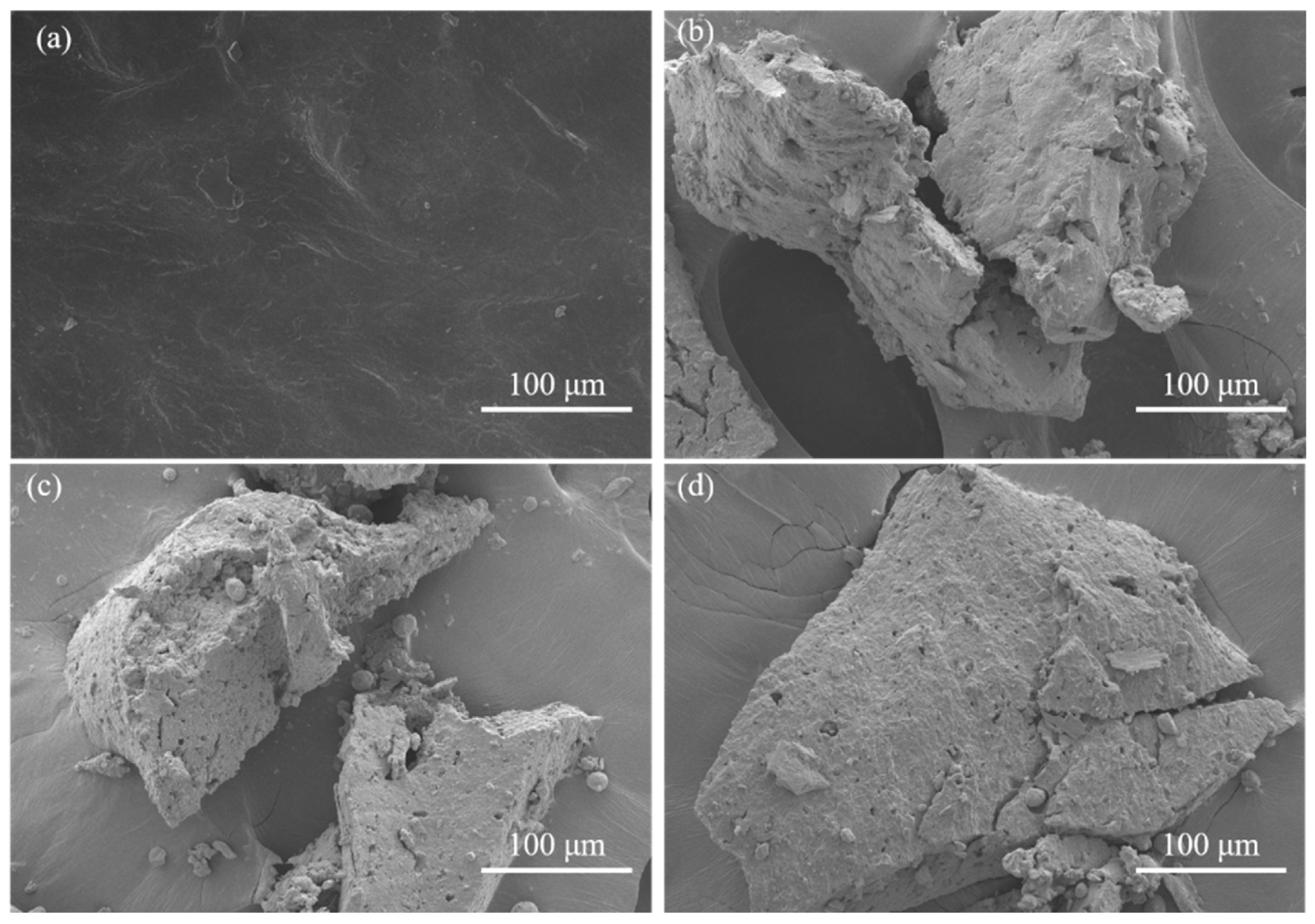
SEM images of different temperature fractured surface of WR: (a) untreated; (b) at 30 °C; (c) at 80 °C; and (d) at 140 °C. Image Credit: Xiao, Q et al., Polymers
Results
The findings demonstrated that temperature and filling rate significantly impact the chemical and physical structure of WR. As the grinding temperature and sol-fraction increased, the sample energy consumption and glass transition temperature decreased. Moreover, the sol-fraction and sample energy consumption increased as the particle size decreased.
The thermo-mechanical approach used by the researchers reduced the particle size of WR, which is an essential parameter for recycled rubber. The mechanism study conducted by the researchers demonstrated that major chain fracture was obliterated by the grinding temperature and filling rate. It must be noted that the reason for significant chain fracture was the oxidation reaction that takes place during the thermal-mechanical grinding process. Moreover, according to researchers, the Rosin's equation could describe the particle size distribution of WR after it has been ground.
The results further indicated that the optimum impact of thermal-mechanical grinding was achieved at a temperature of 80 °C and a filling rate of 85%. The sol-fraction, DSC, and GPC results demonstrated that heat produced during the mechanical grinding caused the crosslinking fracture and primary chain fracture.
The re-vulcanization characteristics of samples exhibited a similar trend as pure SBR. The increase in MH was dependent on the content of RWR and the SBR, RWR with a reclamation degree exhibited high dispersibility and reinforcement. Also, adding RWR to SBR showed no negative effects on mechanical qualities but improved in the case of SBR.
The SEM results demonstrated that the WR without treatment had a smooth surface, and the grinding produced uneven particles with a rough surface. Compared to WR particles ground at 80 °C and 140 °C, the morphology of WR particles ground at 30 °C showed smaller fractures on the surface. Rubber particles become coarser as the grinding temperature increases. Overall, the SEM results showed that the crosslinked rubber was subjected to high pressure and shear stress during the grinding process. Additionally, the network's inhomogeneity caused the stress concentration that led to the breakage of network chains in the samples.
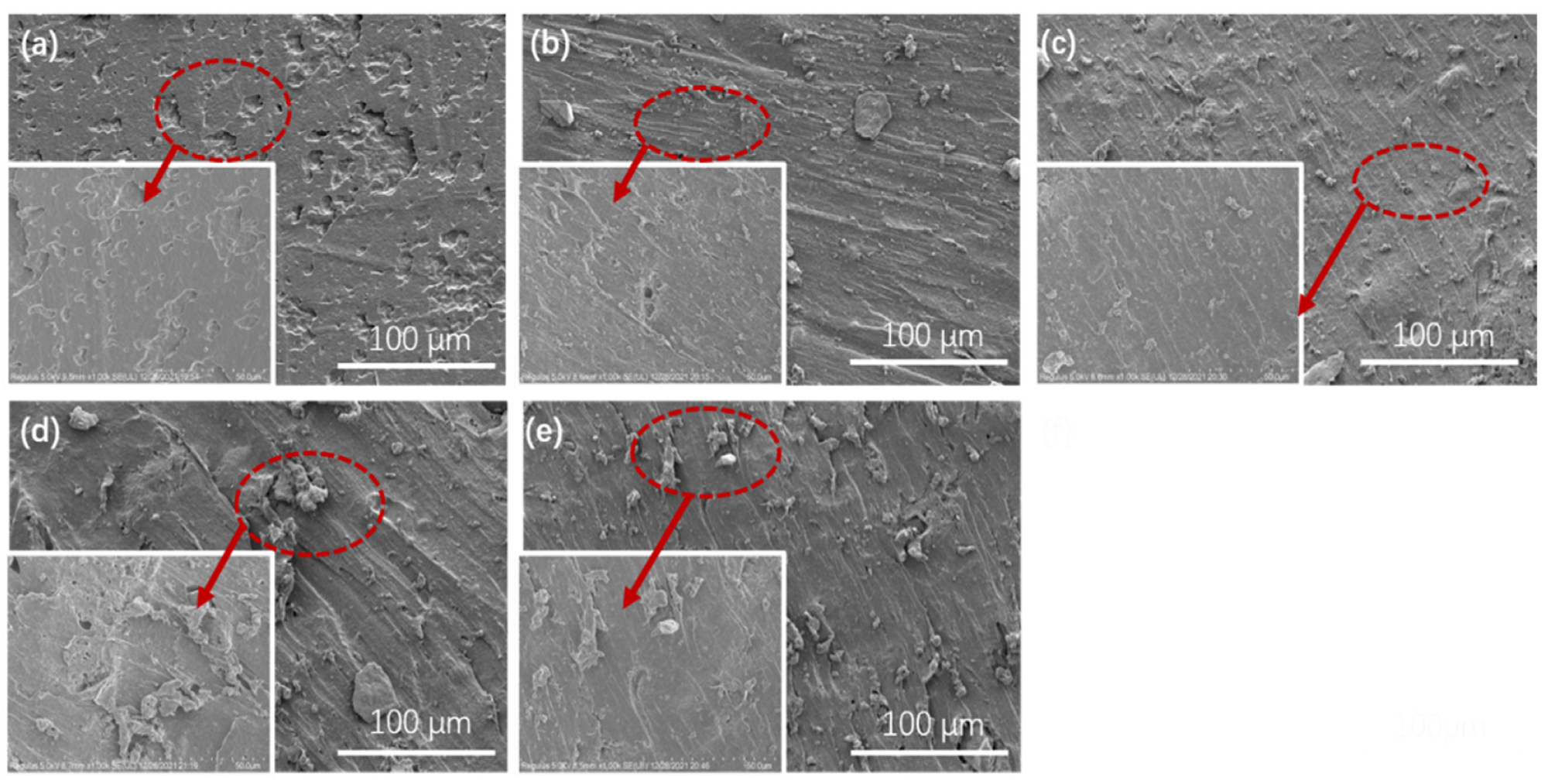
SEM images of RWR/SBR composites: (a) 100SBR/0RWR; (b) 90SBR/10RWR; (c) 80SBR/20RWR; (d) 70SBR/30RWR; and (e) 60SBR/40RWR. Image Credit: Xiao, Q et al., Polymers
Conclusions
To summarize, the thermo-mechanical method reduced the size of WR particles, and the Rosin's equation can be used to characterize the particle size of WR after it has been ground. The oxidation reaction, thermal-mechanical grinding process, sol-proportion, grinding temperature, and filling rate are critical parameters to produce high-quality recycled rubber.
Furthermore, the recycled rubber produced with SBR exhibited vulcanization properties similar to pure SBR. The selective waste rubber breakdown technique demonstrated by the researchers in the current study can be used to reuse the WR produced in the shoe industry.
Disclaimer: The views expressed here are those of the author expressed in their private capacity and do not necessarily represent the views of AZoM.com Limited T/A AZoNetwork the owner and operator of this website. This disclaimer forms part of the Terms and conditions of use of this website.
Source:
Xiao, Q.; Cao, C.; Xiao, L.; Bai, L.; Cheng, H.; Lei, D.; Sun, X.; Zeng, L.; Huang, B.; Qian, Q.; et al. Selective Decomposition of Waste Rubber from the Shoe Industry by the Combination of Thermal Process and Mechanical Grinding. Polymers 2022, 14, 1057. https://www.mdpi.com/2073-4360/14/5/1057