Researchers from Japan have prepared synthetic rubber which possesses identical tensile strength as natural rubber, with implications for the global rubber industry and the possibility of reducing reliance on this important natural material. Their research has been published online in the journal ACS Applied Polymer Materials this week.
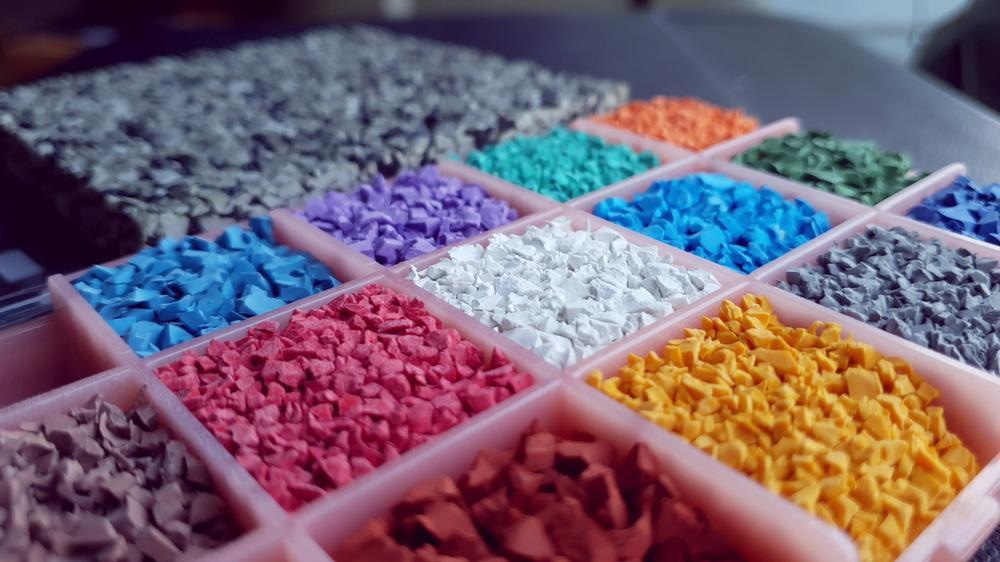
Study: Synthetic Rubber with the Tensile Strength of Natural Rubber. Image Credit: Wongsakorn Dulyavit/Shutterstock.com
Reducing the Reliance on Natural Rubber
Natural rubber has a multitude of applications, including radial tires, seals and padding in automobiles, flooring, clothing, adhesives, coating, anti-vibration pads and mounts, erasers, rubber gaskets, flotation devices, ducting, hoses, linings, and sound-proofing materials. Plants are sources of natural rubber, with the Brazilian rubber tree, Hevea brasilensis, being the main commercial source. More than 40,000 commercial products use rubber.
Rubber has attractive properties such as resilience, efficient heat dispersion, elasticity, impact resistance, superior electrical insulation, and abrasion resistance. Synthetic rubbers, whilst they have been explored in recent decades, cannot easily mimic the properties and performance of natural rubber.
However, despite its usefulness, extracting and processing natural rubber is hugely environmentally damaging. Rubber plantations are a significant cause of deforestation and social issues in vulnerable communities. Additionally, a lack of resource biodiversity leads to supply insecurity due to factors such as diminishing acreage and potential crop failure. Alternative natural sources have been explored in recent decades. Reducing reliance on natural rubber is a key focus for researchers.
Research on the Structure and Biosynthesis of Natural Rubber
Since the early nineteenth century, the structure of natural rubber has been studied and analyzed by many researchers. Early studies focused on the primary structure of natural rubber.
More recent studies have demonstrated that rubber is a nanocomposite. Its main component is cis-1,4-polyisopropene, with minor non-rubber components such as proteins and lipids. Research has indicated that the vulcanization of natural rubber involves the role of non-rubber components through interactions between proteins and zinc ions.
Reactions and phase separations during biosynthesis cause the formation of a nanophase-separated structure in natural rubber. The structure consists of natural rubber particles with a diameter of approximately 1 μm and a non-rubber component matrix which have a thickness of several tens of nanometers.
More from AZoM: Analyzing Membrane Fouling with Atomic Force Microscopy
Producing a Synthetic Rubber Inspired by Natural Biosynthesis in Rubber Plants
Presenting their research in ACS Applied Polymer Materials, a team of scientists has developed synthetic rubber that is identical to natural rubber. The synthesis process is inspired by the biosynthesis of natural rubber and the process that forms what the researchers have referred to as an “island-nanomatrix structure,” which refers to the multiple tens of nanometer-thick size of the matrix.
In their research, the authors chemically attached nanoparticles to synthetic rubber particles ~ 1 μm in size dispersed in water. This process was followed by coagulation and drying steps. The authors favored organic nanoparticles due to the organic nature of proteins. Graft-polymerization at low temperatures of a suitable monomer which is a precursor of a polymer that possesses a relatively high glass-transition temperature onto rubber particles facilitated the attachment of organic nanoparticles.
The researchers used a synthetic cis-1,4-polyisoprene which contained a minimum of 98.5% cis-1,1-isoprene as a source. The material was prepared using solution polymerization. The synthetic material was dissolved in volatile followed by emulsification with water and solvent evaporation steps to create synthetic latex. The researchers stabilized the latex by coating the cis-1,4-polyisoprene particles with rosin, followed by replacement with sodium dodecyl sulfate immediately before the graft copolymerization of styrene.
Conversion of the styrene during graft copolymerization at room temperature was found to be insufficient, at only 15%, increasing only slightly when the concentration of the initiator was increased. This was markedly lower than the target of 80% conversion. The presence of rosin inhibited graft polymerization. Increasing the incubation temperature to 90 oC solved this.
Results of the Study
The authors observed that synthetic rubber possesses identical mechanical performance to natural rubber. TEM was used to image the nanostructure of the prepared synthetic rubber, revealing that it was the same natural rubber’s island-nanomatrix structure. The stress-strain analysis demonstrated that when the synthetic rubber contains this structure, the mechanical properties of the material are identical to those of natural rubber.
Additionally, the results of the research indicated that the optimal vulcanization time for this synthetic rubber was the same as its natural counterpart. Overall, the results of this research indicate the synthesis of a synthetic rubber which solves the traditional problems associated with its manufacture.
Further Reading
Kawahara, S et al. (2022) Synthetic Rubber with the Tensile Strength of Natural Rubber [online] ACS Appl. Polym. Mater. | pubs.acs.org. Available at: https://pubs.acs.org/doi/10.1021/acsapm.1c01508
Disclaimer: The views expressed here are those of the author expressed in their private capacity and do not necessarily represent the views of AZoM.com Limited T/A AZoNetwork the owner and operator of this website. This disclaimer forms part of the Terms and conditions of use of this website.