By Surbhi JainReviewed by Susha Cheriyedath, M.Sc.Mar 14 2022
In a review recently published in the open-access journal Materials, researchers presented a detailed discussion on the development and upgrading of recovered carbon black through pyrolysis of end-of-life tires.
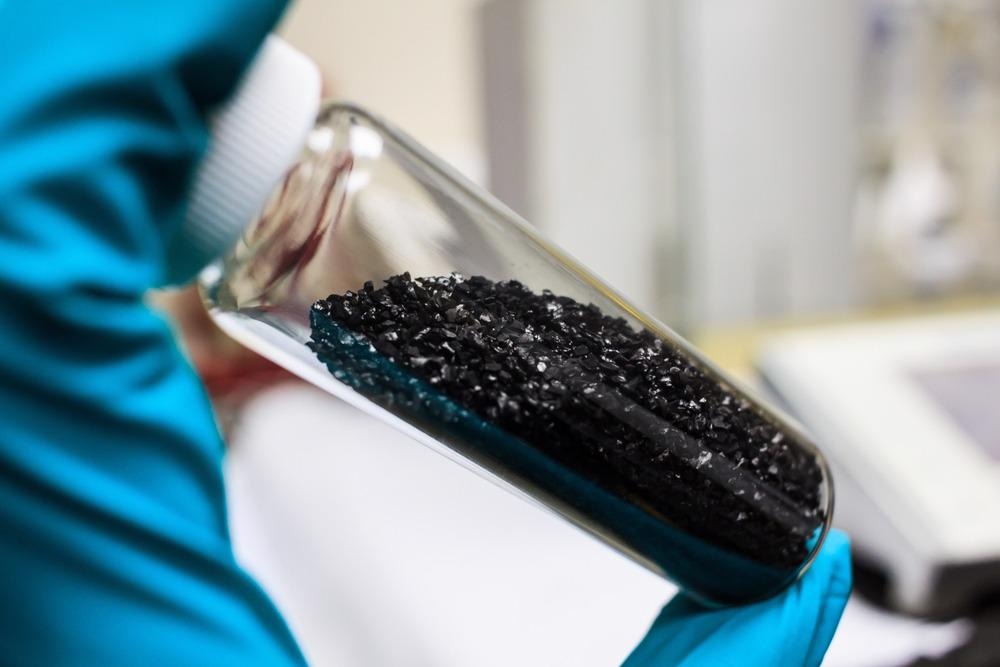
Study: Production and Upgrading of Recovered Carbon Black from the Pyrolysis of End-of-Life Tires. Image Credit: Eaum M/Shutterstock.com
Background
Over the last few decades, growing awareness of fossil fuel dependence, waste valorization, and greenhouse gas emissions has encouraged the introduction of new solutions for a variety of markets. With the global production of more than 1.5 billion tires each year, the tire business is no exception, generating environmental issues about end-of-life recycling and disposal.
End-of-life tires (ELT) have gradually been supplanted by recycling initiatives due to their nonbiodegradability and bulkiness. Tire recovery strategies are highly dependent on their condition, with scrap tires and part-worn tires being the two most common classifications. Tires cannot be retread indefinitely, and when used at high speeds, retreaded tires have a worse quality and safety rating.
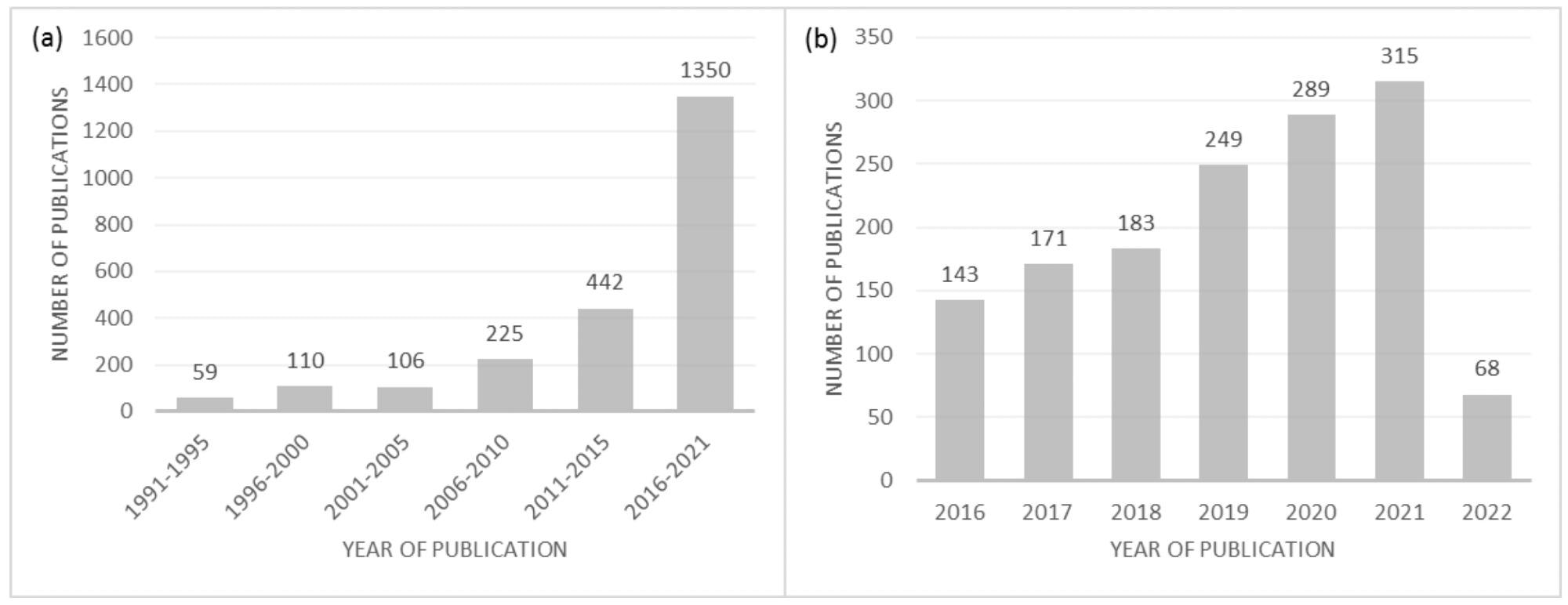
Number of publications on the subject—selected from Web of Science, with the keywords: “pyrolysis” and “end-of-life tires”, “waste tires”, or “used tires”. (a) Number of publications between 1991 and 2021; (b) Number of publications per year between 2016 and 2022 (March). Image Credit: Costa, S. M. R., et al., Materials
Despite the fact that significant progress has been made in ELT management, additional study is required to improve existing methods and offer more efficient alternatives. Pyrolysis technologies have a lot of potential for waste tire recycling because they allow for both material and energy recovery in the circular economy, resulting in valuable gas, liquid, and solid fractions.
Recovered carbon black (rCB), has undergone rigorous testing in recent years to verify its suitability for commercial use. Recent advancements in the activation and demineralization procedures have aimed to produce rCB with unique chemical, physical, and morphological features. The automotive industry, which consumes the most carbon black, has set specific goals for incorporating recycled materials in accordance with sustainability and circular economy concepts.
About the Study
In the present study, the authors reviewed the process parameters, product yield, and the composition of pyrolysis of end-of-life tires for the generation of syngas, oil, and rCB. A thorough examination of the solid material's properties was carried out, as well as their impact on the use of rCB as a commercial CB substitute in the tire business was evaluated.
The purification and modification post-treatment techniques used in rCB upgrading were also examined. The process of the development of syngas, oil, and recovered carbon black (rCB) via ELT pyrolysis was also discussed. The effect of process operating parameters on each product's yield and composition were explored.
An extensive investigation of rCB applications as a substitute for virgin carbon black (CB) in the tire industries and other potential fields was carried out. The use of pyrolysis oil in automobile engines is being investigated as a way to cut down on fossil fuel consumption.
Recent research on rCB upgrading for specific applications, such as purification or reduction of organic contamination and/or modification (ash removal and activation) was also discussed. The Web of Science platform was used to conduct a literature search.
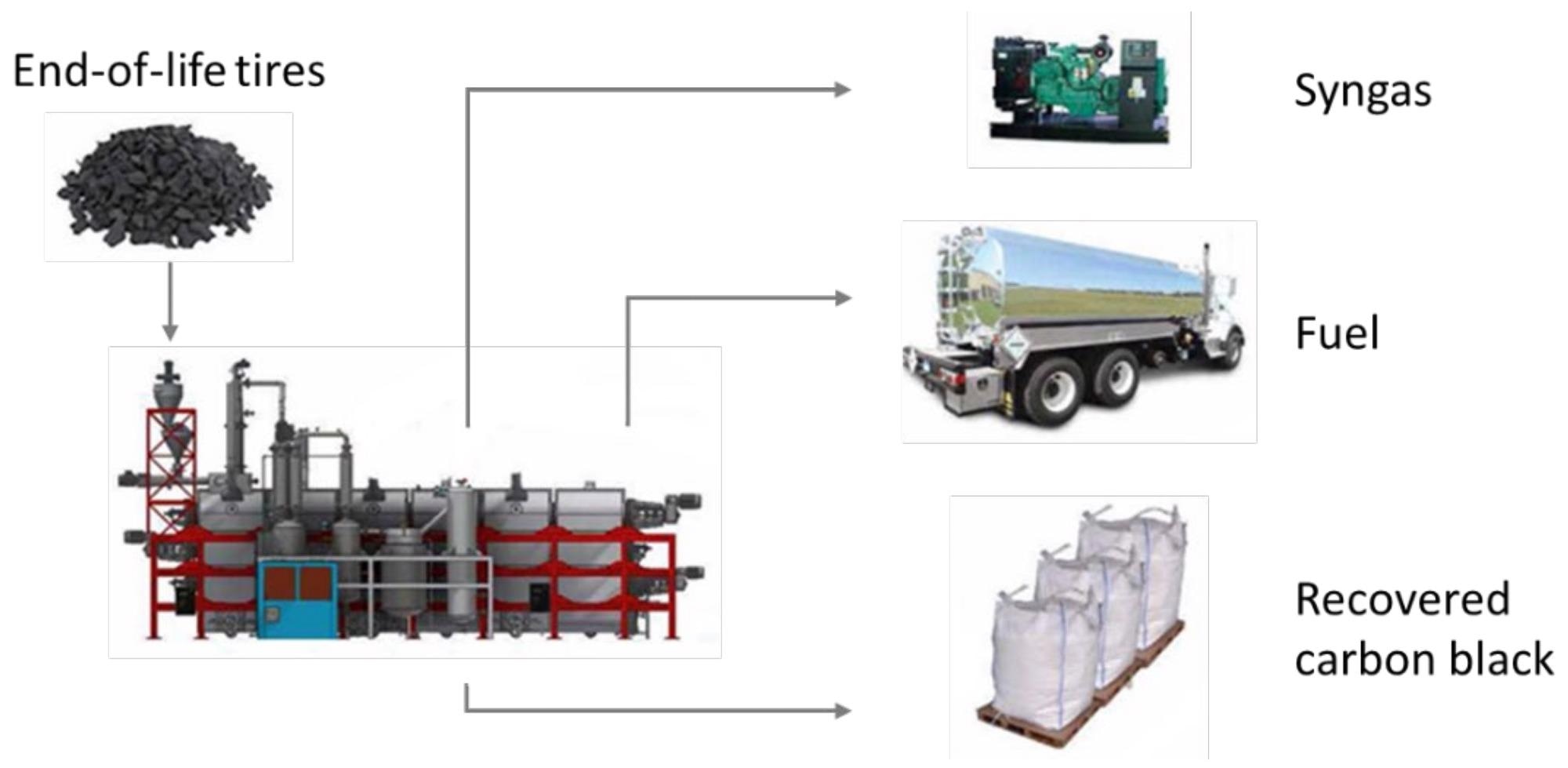
Schematic representation of ELT pyrolysis and ensuing products. Image Credit: Costa, S. M. R., et al., Materials
Observations
Some studies report that Bridgestone has set a target of using completely renewable/recycled resources in place of carbon black (CB) in tire manufacture by 2050 (ca. 1.8 billion tires per year). Several other studies demonstrated the Continental proposal, which aims for 10% recycled materials such as rCB N300 in the tire's composition (~190 million tires per year) by 2025.
Pyrolysis allowed trash, i.e., ELT, to be converted into new useful compounds and energy. However, to optimize the production and qualities of the pyrolytic fuel and rCB, constant development was required. Although it was observed that rCB materials could be made from ELT with morphological and chemical characteristics similar to commercial CB, incorporating it into tires as a reinforcing filler remained a hurdle.
More research is needed to determine whether rCB could completely replace traditional CB grades. This integration was predicted to reduce global CB production by roughly 90%, lowering CO2 emissions wherein preparation of 5.7 kg CO2 eq. per kgCB was evaluated in the case of CB developed by the furnace process.
Furthermore, the conversion of pyrolysis oil to carbon black was observed to be a long-term solution for rCB production. In terms of particle size distribution, yield, absorption capacity, and surface area, many studies showed that rCB materials made from pyrolysis oil and standard feedstock (e.g., ELT) were similar in nature.
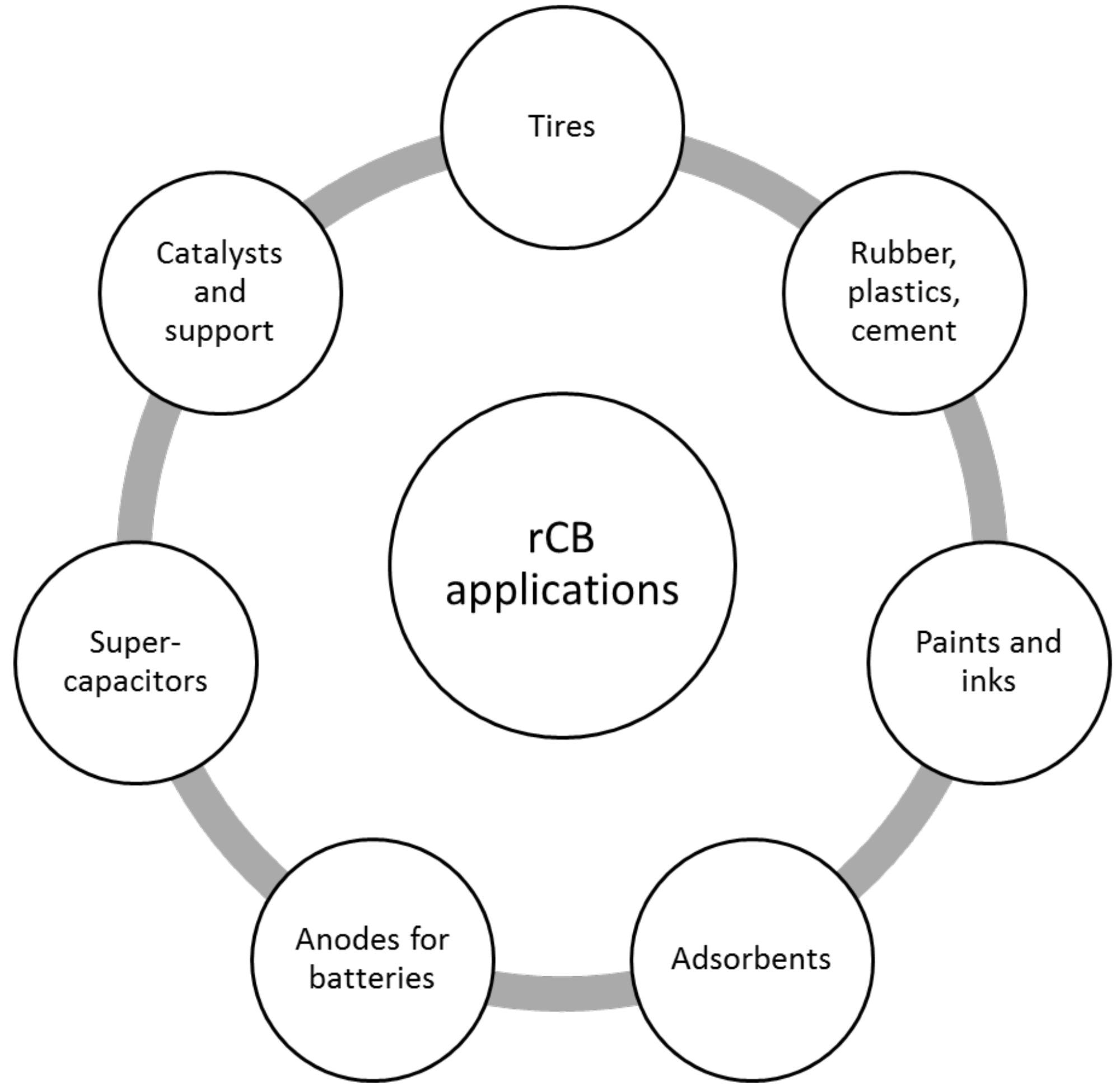
Prospective application fields of rCB. Image Credit: Costa, S. M. R., et al., Materials
Conclusions
In conclusion, this review elucidated the necessity for an industrial paradigm owing to climate change and global warming. The authors emphasized that the path to sustainability must prioritize the reduction of fossil fuel dependence and CO2 emissions, as well as the adoption of circular economy principles.
They also believe that these objectives could be met by using recovered materials in the tire manufacturing sector.
Disclaimer: The views expressed here are those of the author expressed in their private capacity and do not necessarily represent the views of AZoM.com Limited T/A AZoNetwork the owner and operator of this website. This disclaimer forms part of the Terms and conditions of use of this website.
Source:
Costa, S. M. R., Fowler, D., Carreira, G. A., et al. Production and Upgrading of Recovered Carbon Black from the Pyrolysis of End-of-Life Tires. Materials 15(6), 2030 (2022). https://www.mdpi.com/1996-1944/15/6/2030