By Surbhi JainReviewed by Susha Cheriyedath, M.Sc.Mar 16 2022
In an article recently published in the journal ACS Applied Polymer Materials, researchers discussed the utility of simulated polypropylene and maleated polypropylene recycling for highly filled wood plastic composite (WPC) fabrication.
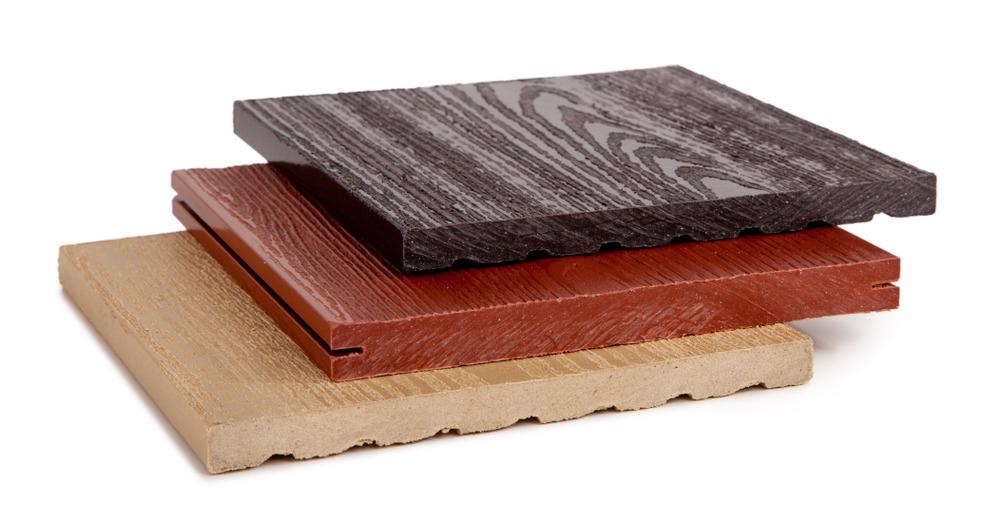
Study: Simulated Recycling of Polypropylene and Maleated Polypropylene for the Fabrication of Highly-Filled Wood Plastic Composites. Image Credit: Krashenitsa Dmitrii/Shutterstock.com
Background
When compared to designed polymers, polypropylene (PP) is one of the most frequently used thermoplastics due to its simplicity of processing which allows it to be used in a wide range of industries. However, there are a few drawbacks to using PP, including its ultraviolet degradation and oxidation sensitivity, poor bonding with polymers and fillers, and a high coefficient of thermal expansion.
The popularity and strong demand for wood-plastic composites (WPC) are due to the aesthetics of composites that resemble wood, while also extending the durability and longevity of natural wood.
The material's high viscosity during processing is one of the key impediments to fabricating densely filled composites. Although the effects of simulated recycling on maleic anhydride grafted polypropylene (MAPP) or its blends and composites have been examined extensively, the impacts of PP reprocessing and compounding maleic anhydride (MA) with PP have not been studied sufficiently.
About the Study
In the present study, the authors illustrate the recycling of PP and MAPP by reprocessing them one to three times. To make highly filled WPCs, 30% of reprocessed PP and MAPP were mixed with 70% wood filler.
A batch mixer and injection molder were used to make the neat and composite samples. Light scattering, nuclear magnetic resonance, rheology, microscopy, and other physical/mechanical properties were used to investigate the effect of PP recycling and maleation. The effect of thermomechanical processing on the chain scission reactions, melt viscosity and weight-average molecular weight was also evaluated.
The highly packed WPC was with up to 70% wood flour (WF) with frequent reprocessing, while the maleation allowed for greater interactions and the composite's strength. The impact of MAPP recycling on polymer and composite functionality and performance was assessed and the probable degradation pathways were investigated. Additionally, the effectiveness of maleating recycled PP (e.g., revived polypropylene (rePP)) to revitalize or retain characteristics, while offsetting virgin and petro-based PP feedstocks for MAPP manufacture, was examined. The thermomechanical reprocessing of MAPP and PP made from single-use plastics i.e., packaging type material was illustrated.
Observations
Due to molecular fragmentation, the viscosities of all the samples dropped after reprocessing, which was proportionate to Mw loss. Also, the mechanical properties were only marginally altered, showing that the degradation was low. MAPP3 and rePP3, on the other hand, showed improved interaction with the WF filling, resulting in superior composite characteristics due to the reprocessing's improved flowability.
More from AZoM: Photoresist Coatings and The Semiconductor Industry
Furthermore, as compared to composite systems, the MAPP3- and rePP3-based WPCs had a consistent fracture morphology with fewer boundary layers, resulting in greater stress transfer.
The modulus increased significantly from 1100 to a maximum of 4850 MPa after the addition of 70 wt% WF. Subsequently, as the transition temperature increased from 22 to 13 °C, adding WF to the polymer matrices had a predominantly negative influence on the damping factor.
The improvement in the interaction among matrices and filler that led to higher mechanical properties in comparison to the other two WPCs was further supported by the reduction in contact angle and modest shift in polarity from PP3 to MAPP3 and rePP3. While the WPCs showed a slight decrease in tensile strength with UV aging (4-12%), it was minor compared to the non-filled PP (PP1), which showed a 47% decrease in tensile strength after 750 hours of UV exposure.
Conclusions
In conclusion, this study elucidated ways to improve the compatibility of polar lignocellulosic biomass, wood fiber, and recycled polypropylene, and discovered that reprocessing MAPP with low grafting content is sustainable for future use due to minimal deterioration. Furthermore, recycled PP maleation has been found to be a viable alternative to virgin PP in WPCs, as it provides a higher level of compatibility at lower Mw than virgin PP.
Because of their enhanced tensile properties and lack of oxidation or severe deterioration, the WPCs containing maleic anhydride had desirable physical properties. The authors emphasized that the maleation of reprocessed PP could be a useful method for lowering virgin and petroleum-based MAPP while restoring mechanical characteristics in WPCs.
They suggested that the effect of recycling or reprocessing on higher MA grafted PPs could be studied in the future. Furthermore, they believe that impact of PP maleation on WPC water/humidity absorption properties is critical.
Disclaimer: The views expressed here are those of the author expressed in their private capacity and do not necessarily represent the views of AZoM.com Limited T/A AZoNetwork the owner and operator of this website. This disclaimer forms part of the Terms and conditions of use of this website.
Source:
Jubinville, D., Tzoganakis, C., Mekonnen, T. H., Simulated Recycling of Polypropylene and Maleated Polypropylene for the Fabrication of Highly-Filled Wood Plastic Composites. ACS Applied Polymer Materials (2022). https://pubs.acs.org/doi/10.1021/acsapm.1c01671