By Surbhi JainReviewed by Susha Cheriyedath, M.Sc.Mar 17 2022
In an article recently published in the open-access journal Materials, researchers discussed the development of highly drug-loaded, reinforced, composite pharmaceutical printlets by using selective laser sintering towards the discovery of suitable excipients for pharmaceutical 3D printing.
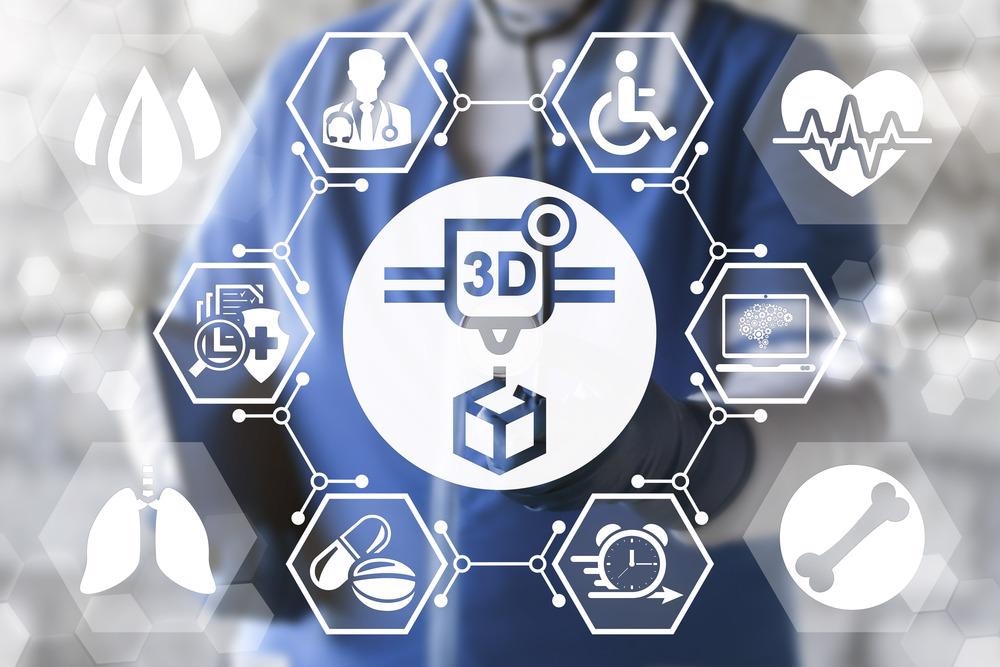
Study: Development of Composite, Reinforced, Highly Drug-Loaded Pharmaceutical Printlets Manufactured by Selective Laser Sintering—In Search of Relevant Excipients for Pharmaceutical 3D Printing. Image Credit: Panchenko Vladimir/Shutterstock.com
Background
The principal approach of increasing gastric residence duration is to use floating drug delivery systems (FDDS). Additive manufacturing techniques such as 3D printing have been used to create medicine delivery formulations in the recent decade.
The employment of selective laser sintering (SLS) is quite uncommon among the numerous 3D printing techniques utilized to construct medication delivery systems. Moreover, the utilization of powders is one of the most significant advantages of the SLS process.
Pharmaceutical-grade materials are primarily used for tableting. Aliphatic polyamides such as nylons are the preferred materials for SLS. Nylon was utilized to make amitriptyline erodible and monolithic matrix tablets. Early in the development of 3D printed pharmaceutical items utilizing SLS, nylon drug delivery methods were developed.
Unfortunately, medication release has been extended up to 7–9 days, which is ineffective when it comes to oral dose types. Another challenge that has yet to be resolved is the inclusion of high-dose active pharmaceutical ingredients (APIs) in printed drug delivery devices. Nylon 12 (PA12) is a semi-crystalline thermoplastic polymer that is extensively utilized for SLS due to the availability of commercially dyed PA12 powders.
The example of printlet: (a) technical drawing (dimensions in mm), (b) printed Formulation A (80/20/0/100). Image Credit: Kulinowski, P et al., Materials
About the Study
In this study, the authors presented the development of composite printlets made of metronidazole (Met) and sintered carbon-stained polyamide (PA12) by using SLS. Differential scanning calorimetry (DSC) and infrared (IR) spectroscopy, as well as an assessment of mechanical properties, were used to characterize the printlets. The printlets' functional qualities, such as drug release in the USP3 and USP4 apparatus and flotation assessment, were also assessed.
The composite material's thermal stability and the identity of its ingredients were both validated. 3D SLS printing was used to create composite printlets made up of elastic insoluble PA12 mesh loaded with crystalline Met in high concentrations. The addition of an osmotic agent to the dissolution process was demonstrated. Moreover, the team illustrated the need for defining the requirements for excipients used in 3D printing and in search for appropriate materials.
PA12 was chosen as an excipient for the corresponding sintering matrix tablets comprising Met. The feasibility of creating a polymer-reinforced and highly drug-loaded composite formulation utilizing FDDS as a working example was demonstrated. The properties of an inert 3D SLS printable excipient, i.e., nylon for Met incorporation were assessed. The extended in vitro drug release characteristics were investigated and probable degrees of freedom corresponding to dissolution tuning were evaluated.
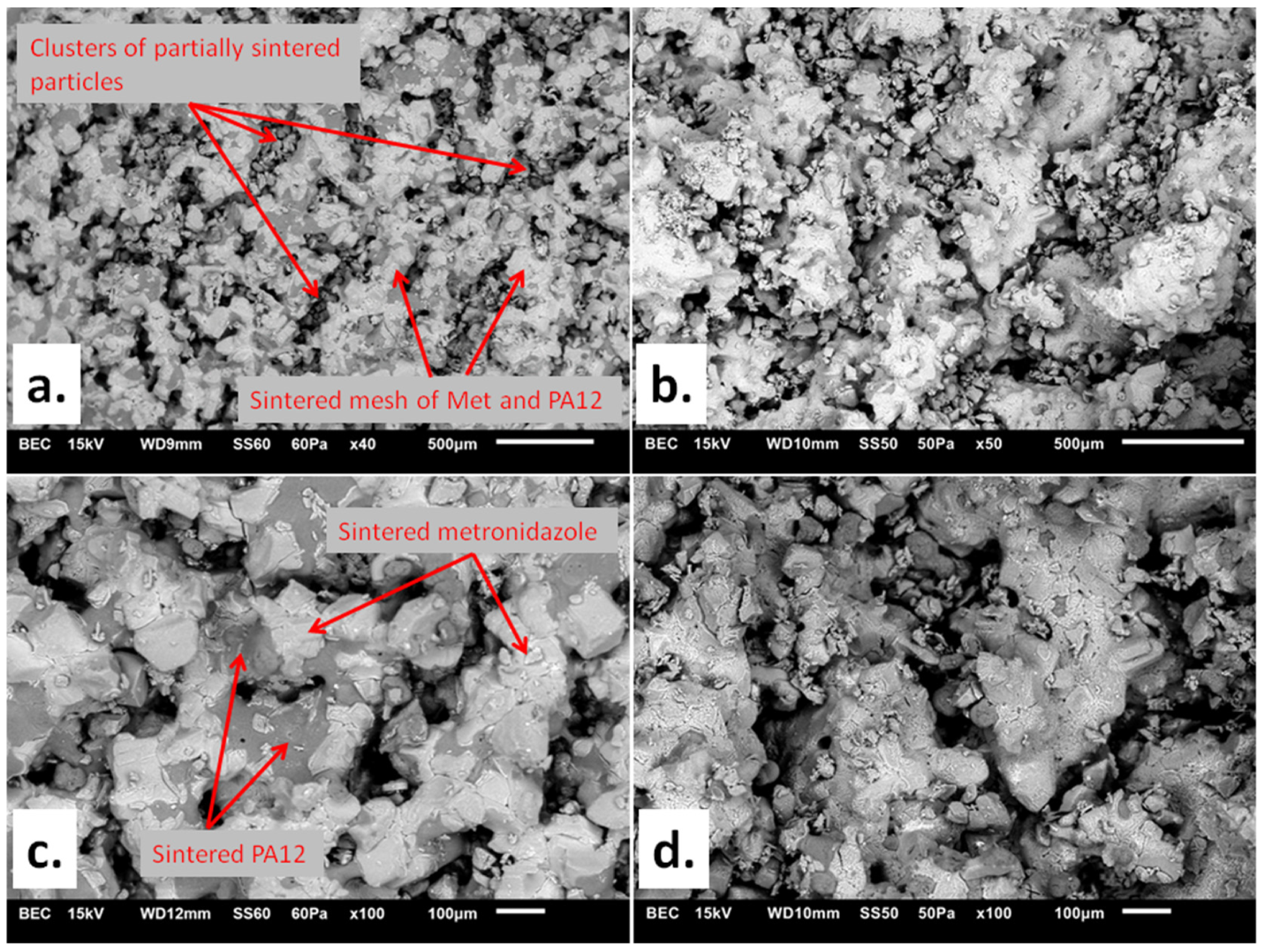
SEM images of (a) Formulation A (80/20/0/100) at 40× magnification; (b) Formulation D (90/10/0/75) at 50× magnification; (c) Formulation A (80/20/0/100) at 100× magnification; (d) Formulation D (90/10/0/75) at 100× magnification. The markings are commented on in the text. Image Credit: Kulinowski, P et al., Materials
Observations
The printlets that had 80% to 90% Met with a therapeutic dose of ca. 600 mg, had a hardness of more than 40 N, and were of fine quality, with an interior porous structure that ensured floating. During drug breakdown and floating, the elastic PA12 mesh maintained the printlets' shape and structure.
The inclusion of low content osmotic agent impacted medication release without modifying the printlet's composition; the releasing time of 80% of Met ranged from 0.5 to 5 hours. Because the mesh made up 10 to 20% of the printlet, a high therapeutic API dose, such as ca. 600 mg of Met, could be included. Despite the high concentration of brittle medicinal components, excellent mechanical characteristics were attained. Formulation D (90/10/0/75), which included only 10% v/v PA12, released about 80% of Met in the first 2 hours.
The developed drug delivery systems, when combined with the printlets' potential gastro-retentive qualities, had the potential to treat H. pylori. DSC measurements revealed differences in thermal properties between powder mixtures and printlets. Drug dissolution from composite PA12/Met printlets could be influenced by the addition of a small number of osmotic agents, such as 2% v/v NaCl.
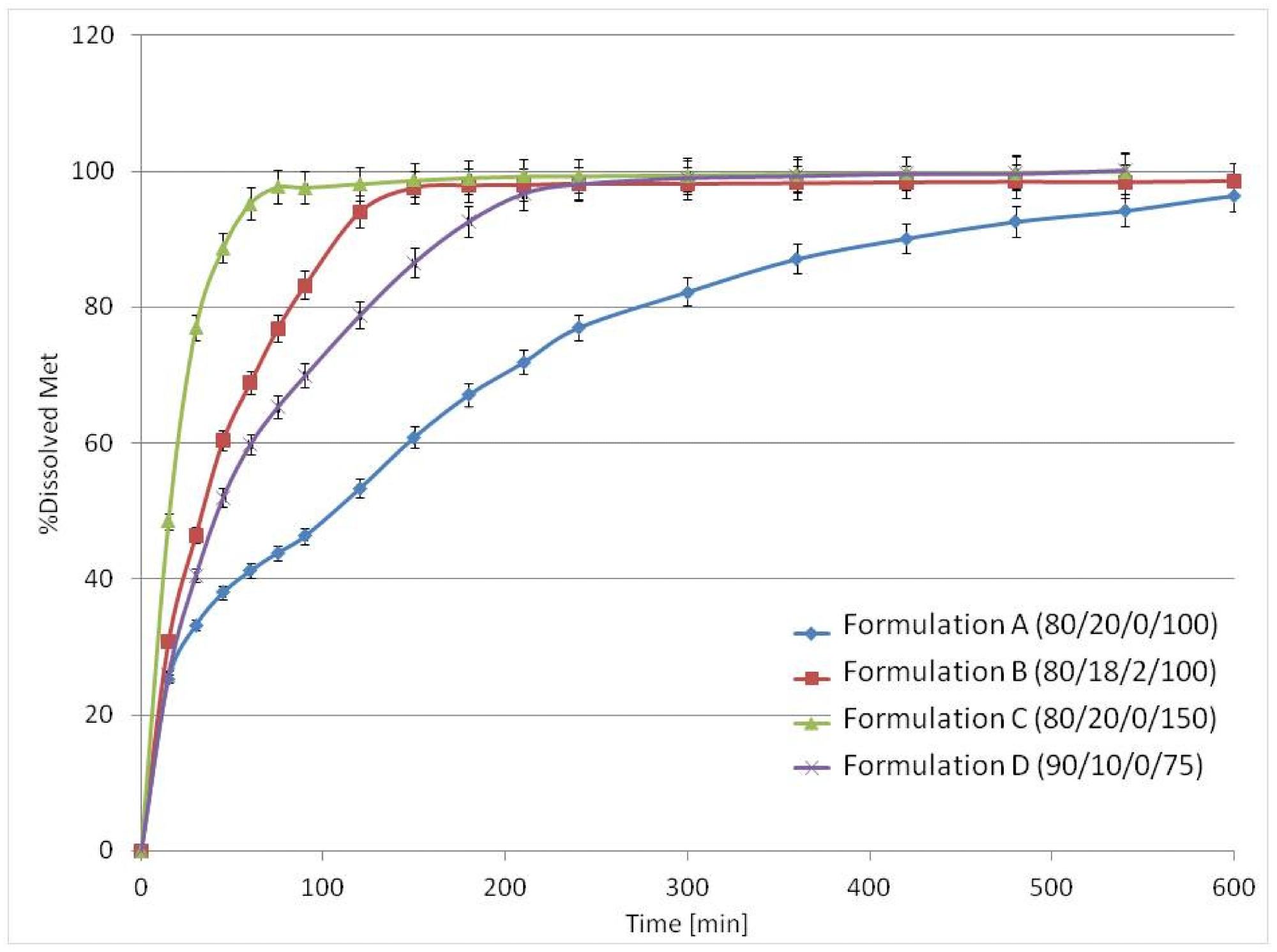
The mean release profiles (n = 3) of Met from 3D printlets in the USP3 apparatus. Image Credit: Kulinowski, P et al., Materials
Conclusions
In conclusion, this study elucidated the preparation of a composite material comprising of elastic insoluble PA12 mesh having a high proportion of brittle (crystalline) Met using SLS. The drug-excipients combo was demonstrated to produce complex thermal patterns in terms of DSC curves, which should be taken into account while choosing printing parameters. A new degree of freedom for shaping and modifying medication release profiles has been offered.
The authors emphasized the need for defining the requirements for excipients used in 3D printing and searching for appropriate materials. They also believe that other printlet formulas can be designed using the developed ideas.
Disclaimer: The views expressed here are those of the author expressed in their private capacity and do not necessarily represent the views of AZoM.com Limited T/A AZoNetwork the owner and operator of this website. This disclaimer forms part of the Terms and conditions of use of this website.
Source:
Kulinowski, P., Malczewski, P., Łaszcz, M., et al. Development of Composite, Reinforced, Highly Drug-Loaded Pharmaceutical Printlets Manufactured by Selective Laser Sintering—In Search of Relevant Excipients for Pharmaceutical 3D Printing. Materials 15(6) 2142 (2022). https://www.mdpi.com/1996-1944/15/6/2142